Materials for mass production of 3D printed products have become more specialised to meet the demand of various sectors. The diversity of requirements has given way for more companies to embark on research and development to come up with targeted materials geared to serve specific industry sector.
Evonik has developed the world’s first bioresorbable polymer in powder form suitable for the high-resolution printing of implantable medical devices on Selective Laser Sintering (SLS) equipment. EOS launched a flexible polymer material, which is a big step towards 3D printing mass production.
World’s first bioresorbable polymer
Evonik announced the development of the world’s first bioresorbable polymer in powder form suitable for the high-resolution printing of implantable medical devices on Selective Laser Sintering (SLS) equipment. RESOMER® PrintPowder is a free-flowing powder with tight specifications and an optimised particle size distribution for efficient processability. Evonik’s advanced powder preparation capabilities can facilitate the supply of ISO 13485-certified formulations for development and commercial use. A range of customisation options are available upon request.
Mechanical properties and degradation characteristics of devices utilising RESOMER® PrintPowder can be precisely engineered to meet key application requirements such as strength, durability and the prevention of stress shielding. Craniomaxillofacial (CMF) plates, spinal fusion cages, scaffolds for soft tissue repair and dental mesh are among the implantable products that can leverage the powder-based polymers to improve patient healing and device performance across orthopaedic, dental and soft tissue application areas.
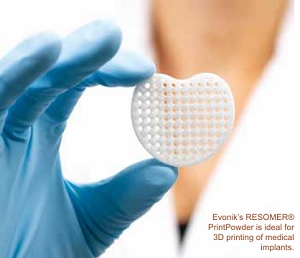
In addition to the supply of RESOMER® PrintPowder, Evonik can also support customers in the 3D printing of feasibility samples on its own SLS equipment, as well as providing other associated testing, analysis, characterisation and regulatory services.
“The free-flowing processability of RESOMER® PrintPowder will, for the first time, allow medical device companies to utilise SLS 3D printing technologies to create complex bioresorbable implants with precisely tailored mechanical properties,” said Dr. Jean-Luc Herbeaux, SVP and General Manager of the Health Care business line. “With the launch of RESOMER® PrintPowder, Evonik becomes the first commercial GMP supplier of bioresorbable polymers with a complete portfolio of powders, filaments and granules suitable for use with all core 3D printing technologies.”
The Health Care business line, which is part of the Nutrition & Care segment of Evonik, serves more than 1,000 pharmaceutical, nutraceutical and medical device customers worldwide. Its portfolio of RESOMER® bioresorbable polymers, Endexo® surface modification technologies and application technologies services is a core element of the Health & Care growth engine, which helps drive Evonik’s profitable and balanced growth.
Flexible material for serial 3D printing
EOS, a technology supplier in the field of industrial 3D printing of polymers and metals, launched flexible polymer material for industrial 3D printing: EOS TPU 1301. This material is a big step towards 3D printing mass production, as TPU materials are widely used in applications that demand elastomeric properties and that need easy to process capabilities. To achieve the flexibility and corresponding damping levels needed for different applications, these properties can be adjusted via structural design and the build process parameters used.
Tim Rüttermann, Senior Vice President Polymer Systems & Materials at EOS said: “The EOS TPU 1301 offers a great resilience after deformation, very good shock absorption, and very high process stability, at the same time providing a smooth surface of the 3D printed part. As such the material is particularly suited for applications in footwear, lifestyle and automotive – such as cushioning elements, protective gears, and shoe soles."
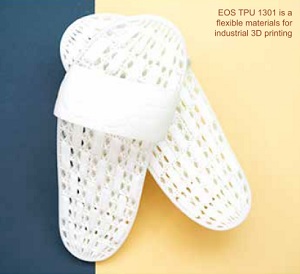
François Minec, Managing Director at BASF 3D Printing Solutions, an EOS development partner, adds: “We are committed to supporting the industrialisation of additive manufacturing and making it a mainstream production technology. As one of the biggest suppliers of TPU materials worldwide, we ensure the best match of powder properties to process requirements, a robust supply chain and batch consistency that meets or exceeds industry-specific quality standards – all essential factors in successful serial AM applications. Our close collaboration with EOS is key here."
EOS has also developed 3D printing solutions to enable the foam industry to employ 3D printing to produce products that are more comfortable, safer, lighter, and can be customised for each individual. The complexity of bringing 3D printed foam to-market has now been simplified by EOS North America (EOS) and its Additive Minds applied engineering team who have launched their Digital Foam™ programme – a hub orchestrated by EOS connecting CAD, materials, part qualification, and additive manufacturing (3D printing).
In this hub, rather than the customer needing to solve for all of these variables, Digital Foam paves the path and gets ideas to reality faster. It gives customers a fast-track to producing 3D printed protective headgear, individualised orthotics, or performance footwear, among dozens of other applications.
Using highly flexible polymer materials, like TPU or PEBA, 3D printing foam allows unprecedented fine-tuning of each voxel (volume pixel) for superior comfort, safety, and performance characteristics. But the process is a sophisticated endeavor that historically requires complex engineering and long cycle times to fully unlock its value – and one that Digital Foam solves.
“The level of engineering required to produce, say, a safer football helmet is massive, but the benefits are equally massive for end users," said Dr. Greg Hayes, senior vice president of applied engineering at EOS North America. “The Digital Foam programme was designed to make those huge improvements much easier and less time-consuming for organisations."
Digital Foam begins with powerful engineering software and one organisation helping simplify engineering design, analysis, and preparation processes is New York City-based nTopology. Bradley Rothenberg, CEO of nTopology, commented: “Digital Foam accelerates the adoption of 3D printing, enabling tunable architected materials like foams. This improves upon basic applications making them exceptional -- for example helmets that are not only safer, but also lighterweight and more comfortable."
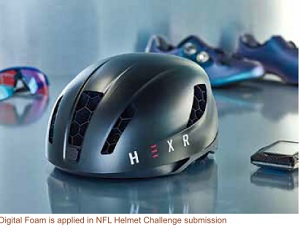
Already employing Digital Foam is Aetrex, a global leader in foot-scanning technology, orthotics, and comfort footwear. Through its partnership with EOS, Aetrex uses a Digital Foam approach to analyse customers' feet using its proprietary Albert scanning system, identify pressure points, and then produce custom 3D printed orthotics. The result is an individualised orthotics product, manufactured via mass customisation that is affordable, lightweight, and perfectly matches each individual's foot.
“What Aetrex is doing is a perfect example of how Digital Foam can make 3D printed foam applications mainstream in the digital-manufacturing era," added Mr. Hayes. “We have created a sophisticated but easy-to-use solution that connects dozens of dots in the value chain, delivering better products to the market faster than ever." EOS and its partner organisations will be submitting a Digital Foam entry as part of its NFL Helmet Challenge submission, competing to engineer and develop football helmets that outperform today's models. The winner of the NFL Helmet Challenge will be announced in May 2021.
Adidas Pure Boost