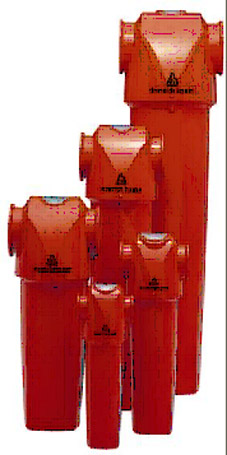
LEADING international dairy producers and packagers are adopting compressed air filtration available in Australasia that is designed to be the most energy-efficient in the world. Oil-X Evolution compressed air filters by Parker domnick hunter Filtration use aerospace technology to optimize air flow paths through the filter's housing and element to significantly reduce air turbulence and pressure losses, reducing system operating costs. John Davis, Parker domnick hunter Filtration business development manager, says the technology is eminently suited to the dairy industry, where production purity and energy efficiency are essential to efficient manufacturing. This has led to global acceptance of the technology in Norway and France. At Tine Norske Meierier BA of Klepp in Norway, which is one of the most modern and technically automated dairy packers in Europe, pneumatic machinery does most of the work of slicing, grating and wrapping cheeses and the compressed air driving this machinery must be of the best quality. A new central compressed air system was installed by domnick hunter/Hillevag Elektro Diesel AS and was fitted with a "Pneudri" desiccant dryer and Oil-X and Bio-X filters to ensure absolute purity and sterility. "Energy saving controls on this purification package will save the company more than 100,000 kWh per year in energy consumption, according to Gaute Nesse, the company's maintenance manager," says Davis. Similar technology has also been adopted by one of the largest independent French manufacturers of yogurts and fromage frais, which are now using domnick hunter filters to produce high quality steam and sterile compressed air. The steam is used throughout for general cleaning and sterilization of packing equipment while the sterile air is used in the transportation and packaging process itself. "Key in the selection of domnick hunter filters was their low pressure drop which helps to minimize energy costs," Davis claims.
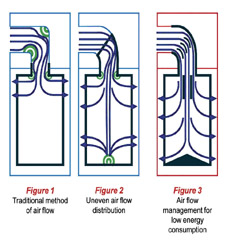
This high-efficiency filter is truly a generational evolution that results in the most energy efficient filter of its type in the world, Davis adds. Installed in a compressed air system using a 185 kW compressor, for example, the innovative design could save the user up to 60% per filter in energy consumption compared with a traditional filter. With nine new international patents pending, Oil-X Evolution filters have been designed to provide a very low initial saturated pressure loss which stays low throughout their 12-month guaranteed life, he says. To achieve this, the filter media is a borosilicate glass nanofiber with 96% open area or voids volume, providing an extremely high dirt holding capacity. A special oleophobic coating actively repels oil and water, ensuring the open area is maximized for dirt entrapment. The surface area of the cartridge has also been maximized with deep pleat media beds, which provide surface areas up to five times greater than filter elements using standard wrapped construction. This allows overall filter size to be reduced and ensures pressure losses start low and stay low.
Zoom Lebron Soldiers IX 9