Upgraded design and added features are keeping the blow moulding sector alive. In Asia, interesting updates in injection stretch blow moulding will be witnessed at Chinaplas 2019.
For instance, Nissei ASB Machine Co., Ltd. is set to present its “Zero Cooling” Technology and revised machine design from its ASB series which are seen as a quantum leap for high quality and productivity. The company is set to hold a live moulding demonstration at its booth together with a display of some of the most interesting recent updates in injection stretch-blow moulded packaging technology. Given that the exhibition has grown in terms of significance far beyond China’s borders and with year-on-year increases in overseas visitors it makes an ideal venue for ASB to reach potential customers across the eastern hemisphere.
Improving moulding efficiency
“Zero Cooling” pushes moulding efficiency a step further. “Zero Cooling” PET container moulding technology modifies the standard moulding method to achieve greatly increased productivity and container quality. This patented technology is ASB’s revolutionary in preform cooling technology as it enables significantly faster moulding cycles than seen previously while at the same time actually increasing product quality.
“Zero Cooling” pushes moulding efficiency a step further. “Zero Cooling” PET container moulding technology modifies the standard moulding method to achieve greatly increased productivity and container quality. This patented technology is ASB’s revolutionary in preform cooling technology as it enables significantly faster moulding cycles than seen previously while at the same time actually increasing product quality.
Taking full advantage of ASB’s proprietary 4-station, 1-step moulding method, virtually all the required preform cooling is shifted away from the injection station and into the second, conditioning station enabling dramatically reduced injection cycle times. Crucially, the Zero Cooling moulding method enables these fast cycle times to be achieved while avoiding the need for thin, non-optimised preforms that are susceptible to several quality related problems, most notably “fisheye”, “body ring” and “orange peel”, all of which are undesirable.
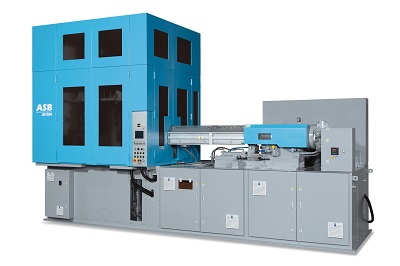
In standard moulding, preform cooling requires a significant portion of the total cycle time. By shifting the necessary preform cooling from the injection station to the conditioning station, it can be combined with the appropriate temperature profile adjustment. The injection station is now available to start filling the cavity for the next injection cycle while cooling of the previous shot continues simultaneously in the conditioning station. It is this removal of cooling from the injection station that enables average productivity increases of 1.5x and gives rise to the name of “Zero Cooling” for the process.
Since the cooling rate of PET resin is a fixed property, in standard moulding, the only way to shorten cooling time is to make the preform thinner, which for a given container weight means the preform also becomes larger. Doing this reduces the overall stretch ratio from preform to finished container so the positive effects of strain hardening from biaxial orientation, that increase the stiffness and tensile strength of PET, are significantly reduced. Smaller preforms have the advantage of providing higher stretch ratios resulting in excellent material distribution and topload strength around 15% higher than standard moulding or that of competitor’s products, but with standard moulding, thicker preforms would require longer cooling resulted in reduced productivity. But now with Zero Cooling, this limitation has been overcome, the new process allows for the use of smaller, thicker preforms that can be moulded much faster than previously possible because cooling is conducted in the conditioning station simultaneously with the next injection cycle. Furthermore, since the material strength has been improved by better orientation, more scope is available to apply additional light-weighting to a container’s specification.
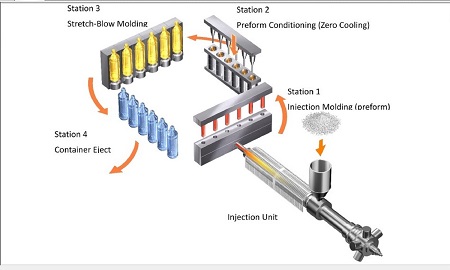
This groundbreaking moulding technique effectively eliminates the traditional need to compromise the preform design between cycle time and container quality. It is made possible by the four-station moulding process of the ASB Series machines having the preform conditioning station between the injection and blow stations.
Also at Chinaplas, Nissei is set to demonstate its ASB-70DPH One-Step Injection Stretch Blow Moulding Machine model. The mid-range ASB-70DPH model has been a best seller for over 30 years due to its economy, flexibility and convenient size – and due to regular technology updates, it has stayed at the forefront of 1-step moulding technology with class leading efficiency. The version being demonstrated at Chinaplas 2019 is a pre-production model of the next generation design that showcases a wide range of updates and options that further enhance flexibility but most importantly, complements the Zero Cooling moulding process to dramatically increase productivity over previous models, especially for smaller containers. The key points include: revised hydraulic circuit provides faster, smoother motion of clamping; adjustable stroke in all clamping stations reduces machine indexing time for shorter preforms, while adjustable daylight also allows longer preforms, a feature especially useful for non-PET moulding resins; fully revised blow station reduces index time, simplifies blow mould changeover and reduces maintenance; compatibility for existing ASB-70DPH moulds is maintained; and optional integrated height adjustment system for injection unit reduces mould changeover times in high product mix moulding scenarios.
With these updated machine features giving a 40% reduction in indexing time, the demonstrated 30ml container using a short preform can be moulded at up to 2.2 seconds faster than that achievable by the previous model. This saving is in addition to the reduced cycle time obtained from the use of Zero Cooling technology in the mould design. Combining the aforementioned machine revisions with ASB’s Zero Cooling mould technology that enables more than 1.5X increase in productivity, the 8-cavity, single row mould producing a 30ml, 3.8gram, 18mm screw neck container for medical or toiletry use will provide over 6,200 bph.
Buty sportowe Nike