Plastics recycling has become an all-important issue given the growing concerns for environment protection. Fortunately, the range of recycling technologies has become wider unlocking potential benefits in terms of cost-efficiency and productivity.
At the recent Fakuma 2017, EREMA, a manufacturer of manufacturer of plastics recycling systems once again extended its portfolio to offer the proven melt filter as individual components for existing extrusion plants. Prior to the founding of its POWERFIL business unit, EREMA implemented some technical modifications to the filter systems. In line with the motto "Plug in Performance" the POWERFIL business unit offers both the SW RTF partial surface backflush filter system and the Laserfilter as individual components from now on. This development enables potential users to upgrade their existing extrusion plant from alternative suppliers by adding one of the proven EREMA melt filters. "With the new POWERFIL portfolio we aim to show even more clearly that our filter systems represent a high-performance solution also for third-party extrusion systems – although the technology used is not new, but has already been tried and tested thousands of times. EREMA filters are in use on over 5,000 plastics recycling systems around the world. Customers who count on our melt filter can rely on EREMA quality", according to Mr. Manfred Hackl, CEO EREMA Group.
Besides fast availability, customers will above all appreciate the filtering quality and the quick amortization which comes with it," added Mr. Robert Obermayr, head of the new business unit POWERFIL. "In recent years the growing recycling market and the noticeable parallel increase in more heavily contaminated input materials have led to a growth in the demand for efficient filtration systems – also in the case of existing extruders. We can meet this demand with POWERFIL and offer – especially with the Laserfilter – a functional concept which unites high quality requirements and stable, inexpensive operating costs.
With the EREMA Laserfilter, a continuous filter system with screen fineness of 70µm is now in operation for the first time. An even gentler filtration process has been made possible by rheological optimization of the support breaker plate, enabling a reduction of flow resistance. Inquiries for the Laserfilter, which is already established in the post-consumer field, are also increasing from customers in the PET sector. The reason for this is that the increased use of rPET in end products requires high process stability despite higher degrees of contamination at times.
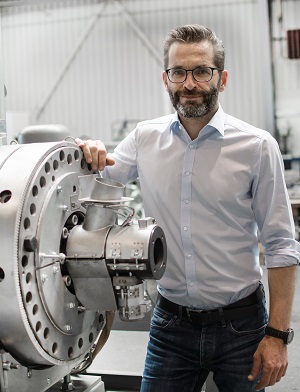
Mr. Robert Obermayr, head of EREMA’s new business unit POWERFIL
The Laserfilter processes input material with a degree of contamination of over one percent without any difficulty. The functional principle avoids dead spaces and makes for short dwell times which in turn prevents "black spots" with PET. Thanks to the newly developed discharge unit, melt losses are reduced from the normal 1 to 2 percent with piston filters down to a tenth.
State-of-the-art washing plants
AMUT GROUP confirmed its dedication to the Green Economy via its state-of-the-art range of washing plants for the treatment of PET, HDPE and PP plastics and urban and industrial waste sorting equipment.
The complex of the plants is represented by two typical machines. The first one is a turbo washer, TW 800 model, a machine that performs an intensive washing action and purifies the plastic material from inorganic and fine pollutants using centrifugal force. During the centrifugal process, dirty water, sand, paper fibers and soil flow through the basket holes, whereas flakes are retained. Available in different models, TW800 is the biggest one suitable to process up to 6000 kg/h of PET, 4000 kg/h of HDPE and 1500 kg/h of LDPE.
The ballistic separator, MPC model, is properly designed and developed to sort paper and cardboard. The inlet flow is divided into two different material streams, not only through the wave motion of paddles, but also through the holes with variable section, placed on their surface. Fractions of output material are the following: cardboard and material sized > A4; de-inked paper sized < A4; the paper material < A4 passes through the holes of the ballistic separator paddles, while the flat cardboard > A4 is pushed forward.
Minimizing downtime in PET recycling
Bottles are turned back into bottles: This is common practice at BTB PET-Recycling GmbH & Co. KG where 20,000 tons of PET input material from the German bottle return system PETCYCLE are processed every year. Founded in 2006, the company started operating a Starlinger PET recycling line type recoSTAR PET 165 iV+ the year after, and presently the system has 6 SSP reactors producing food-safe PET regranulate for reuse in the production of beverage bottles.
The company is in possession of a positive EFSA opinion concerning the food safety of its rPET; an extended EFSA-submission has been filed. In addition, BTB PET-Recycling is certified according to ISO 9001:2008 as well as ISO 50001:2011. A factor worth highlighting is its first-rate life cycle assessment: The geographical proximity of preformer, bottler and recycler reduces the carbon footprint to a minimum. BTB PET-Recycling has fixed customers for its regranulate; an internet presence is therefore not necessary.
Changing market requirements call for flexibility and constant adaptations on the part of the recycler. Over the course of the last 10 years, there have been massive changes in the design of PET bottles, e.g., the bottles have become lighter and/or their walls have become thinner (causing the bulk density to change significantly), and they may contain additives (acetaldehyde and oxygen blockers). According to one of the managing directors of BTB PET-Recycling, Mr. Andrzej Zajontz, the Starlinger recycling line is insensitive to variations in input material. These can be compensated by parameter adjustments alone, thereby ensuring consistent regranulate quality. To keep the machine up to date from a technical point of view, upgrades are provided on a regular basis. The recycler emphasizes the machine’s ease of operation – allowing for swift training of new personnel – as well as Starlinger’s uncomplicated service.
A definite advantage is the modular design of the Starlinger line at BTB PET-Recycling. By adding an additional vacuum SSP reactor, the capacity can be extended very easily, allowing for continuous growth. Company owner Mr. Richard Wüllner reports that the capacity was increased through adding one SSP reactor in 2013 as well as in 2015 to meet the growing demand for food-safe regranulate. In addition, upgrades were made in the areas washing, bottle sorting, and flake sorting. A further increase in capacity is planned for the near future. The regular investment in the recycling line shows that the recoSTAR PET at BTB PET-Recycling is far from being outdated, on the contrary: It is well equipped for the next 10 years.
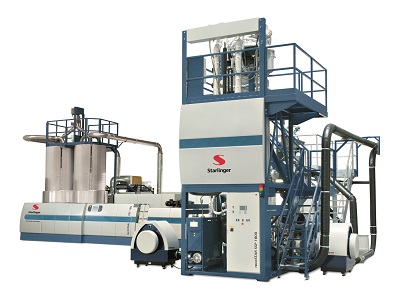
A Starlinger recoSTAR PET 165 iV+ with SSP 1800.
Consistent quality from a recycling line
As the largest LLDPE stretch and PE cling film producer in Taiwan with monthly production of 3,000 tons (achieved with several 5-layer cast film machines from Germany), in-house recycling is valued highly by the 30-year-old film producer as part of the production process to ensure quality and consistency in the end product remain high.
Ever since the company’s major expansion in 1991, it has been carefully selecting only the best and world-class machine manufacturers in the market as its partners. The company was the first Taiwanese film producer to bring in a 5-layer casting extruder from Germany and is now equipped with several multi-layer cast film and printing machines from Europe.
In 2016, the film producer has opted for the POLYSTAR recycling line to process its in-house waste generated from the extrusion lines. The POLYSTAR line was in fact the first equipment that the producer has ever purchased from an Asian manufacturer. Sharing his experience on the decision making process, the CEO was particularly impressed after seeing the trial runs at POLYSTAR’s facility, mainly for several reasons.
First, the recycling line requires simple operation and maintenance. The increase in labor and logistics cost in Taiwan has become more difficult for Taiwanese plastic producers to stay competitive. Hence, making sure that minimal labor intervention on the machine is crucial. Second, the recycling line also guarantees consistency and quality in the recycled pellets. The consistency in quality (uniform in size, reusability, minimal property change and degradation) of the recycled pellets can ensure that the recycled material can be reused again in the extrusion machines to produce high-end film product with the highest possible quality.
The POLYSTAR recycling machine is now running 24 hours a day and 7 days a week in the factory of the ISO 9002 certified film producer,with an average production of 250~300kg/hr with little operator intervention, setting another great example of effective and valuable in-house recycling.
The defected film-on-rolls are fed automatically via the nip rolls on top of the cutter-compactor, which is then compacted and fed directly into the recycling extruder for further processing and pelletizing. The rest of the occasionally generated scraps are fed via the conveyor belt. The two-way feedings are controlled automatically and simultaneously to prevent over-feeding or insufficient feeding of material into the machine.
Despite the difference and variation in film width, thickness, layer structure (mono, three and five layers), the machine can handle all these film scraps of different compositions with consistency and still produce high quality and uniform-sized pellets, which are then put immediately back into the cast and stretch film lines. The design of POLYSTAR recycling machine is also very compact and takes up very little space.
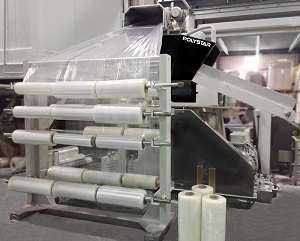
POLYSTAR plastic film recycling machine
womens nike shoes