The Asia-Pacific region retains its growth momentum with many of the countries in the region expected to post industrial growth from 2017 onward. Growth in the Asia-Pacific economies is projected to reach 6.3% in 2017, according to the Regional Economic Outlook for Asia and Pacific by the International Monetary Fund (IMF). Asia remains the engine of the global economy, exceeding the world economic growth outlook.
In particular, China has experienced rapid changes in the past few years, owing to both domestic conditions and international influences. Despite some challenges, China’s resilient plastics industry remains a key driving force in the global industry, and has performed well above expectations. Large demand has been noted from such sectors as automotive, electronics/electrical, packaging, medical/healthcare industries where plastics are increasingly replacing traditional materials.
Taiwan will sustain its role as a leading source of plastics processing machinery and tools and in 2017, the island’s major companies are expected to move forward aggressively in the global market with their innovative products. Recent developments have paved the way for Taiwan taking a strong position in the development of more advanced technologies in plastics production. In support of this trend, the Plastics Industry Development Center has set up a $10-million plastics medical research building. The center is also assisting the plastic processing industry in the research and development of more sustainable materials in the areas of composites, 3D printing, aerospace and automotive, functional films and other important sectors.
Member countries of the ASEAN are also fast catching up with the establishment of the ASEAN Economic Community (AEC), a single market of 600 million people, expected to significantly boost industrial production, trade and services within the region. The plastics industry in ASEAN remains strong in the wake of global developments. The sector’s production rates have witnessed a steady average growth over the recent years, especially in the ASEAN-6: Indonesia, Malaysia, the Philippines, Singapore, Thailand, and Vietnam, which account for more than 95% of regional GDP.
International Plastics News for Asia gathers the insights from representatives of leading companies in the plastics industry on the trends and developments in 2017 and how these would impact their operations.
TECHNOLOGIES AND EQUIPMENT
Simple, highly efficient systems to gain acceptance
Optimism dominates the auxiliary sector with many players constantly developing innovative products to support machinery manufacturers. According to Frank Kavanagh, Vice President of Sales of Maguire Products, Inc., the company has responded to the automation trend by launching a new breed of gravimetric blenders aimed at speeding up the transition toward an Industry 4.0 operation.
“For our range of gravimetric blenders, we have just launched the new Maguire® 4088 controller, which operates with seven times the speed of the previous controller, eight times the memory, and 45 times the resolution of the load cells used to weigh batch ingredients. Because of its far greater data processing capability, the 4088 controller helps plastics processors speed the transition toward an “Industry 4.0” mode of operation by substantially enhancing communications with other devices.” In addition, by combining centralized control of both blending and loading, it addresses the need on the part of many processors for a greater degree of factory automation.
“I cannot discuss our range of gravimetric blenders, however, without pointing out that 2016 is a landmark year for us—the year in which we have shipped our 50,000th Maguire® blender,” Mr. Kavanagh added. When Maguire company president Steve Maguire developed the gravimetric batch blender in 1989, it was the first affordable and easy to operate system for precisely controlling the composition of a raw material blend. Today the Maguire blender is the world’s most widely used gravimetric blender and has been installed in every type of plastics manufacturing operation, from compounding to extrusion to molding.
Another quite new product from Maguire is our LoPro™ vacuum loading system for conveying pellets and regrind from storage to single or multiple blenders. It is simpler to operate than standard systems and consists of autonomously controlled receivers that are fully 80% shorter than conventional material loaders and receivers.
For 2017, Maguire is looking forward to a surge in European business. “Industry-wide we see a move toward smarter, more intuitive equipment controls that integrate multiple features and functions to one simple interface. One example is the new 4088 blender controller, which, as I mentioned, provides centralized control of both blending and loading and facilitates communication with other devices in the factory setting,” Mr. Kavanagh explained. Mr. Kavanagh also sees a trend toward “seamless data,” where the push for simplicity and visualization is crucial. This allows managers to see in a moment how the process is running and that a plant is effectively controlling its raw material simply and efficiently.
“With the growing drive to the internet of things and being better connected, there is a sweeping movement in the industry to make operating systems simpler, easier, and faster, yet for that to be really true a huge amount of work and investment has to happen. With the speed of change in things like consumer apps, for example, what was great two years ago maybe completely superseded now. So a major challenge for us is to lay down a system “backbone” that looks both forward and backward. A key premise to equipment design for Maguire has always been the ability to have full compatibility from a system built today in relation to a system built in, say, 1990. We are committed to make sure this holds true with all our products.”
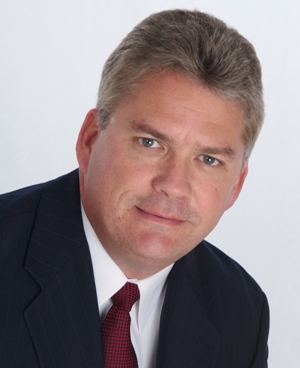
Mr. Frank Kavanagh, Vice President of Sales - Maguire Products, Inc.,
Maguire Products Asia Pte Ltd.
Tel: +65-6848-7117
E-mail: magasia@maguire-products.com.sg.
Website: www.maguire.com.
Non-European markets offer more opportunities
For Karl Schäuble, Managing Director of ILLIG, there are even greater opportunities from non-European markets now than before and the future is brighter in these new markets. The company has noted an increase in sales in the non-European markets, as well as an increased demand for packaging machines such as HSA, BSA, and FFS lines.
Mr. Schäuble said: “Because of the positive development in the non-European markets we installed a branch office in South America in 2015, and at the end of last year we started operation of an assembly plant in India. Currently, we are revising our service concepts in further markets. On one hand we meet the requirements there, and, on the other hand we find that numerous European customers are concerned with production in non-European markets. We can offer our support especially for service-related questions.“
Particularly southern European countries continue to show weak investment since their economic growth will most likely be very subdued. According toMr. Schäuble, this still also applies to the eastern European markets. In his opinion, the current politically unstable situation will limit the willingness to invest in this region even further.
Today ILLIG delivers more than 60% of its machines and lines to non-European countries. Customers in Asia, the Arab region, as well as in North, Central and South America employ this technology to meet the increasing demands with respect to packs in their countries. “Quality and hygiene demands for packs continue to increase in most regions. In economic terms this can only be realized with constant, high product quality and high productivity at the same time“, Mr. Schäuble added.
With a look to the future of thermoforming Mr. Schäuble sees the focus of development in the coming years on the expansion of automation and “clean” production. “We expect that in the future the increase of quality time for ILLIG lines will also be of major importance, with large batch sizes and a high automation level. This will result from the fact that we will continue to increase speeds in the thermoforming and punching process since quality and reproducibility of parts can thus be further improved.“ In this respect ILLIG supports the pack manufacturers with machines and complete lines for thermoforming, equipped with innovative control systems, and particularly the “ILLIG Intelligent Control Concept” (ILLIG IC) presented at the last K show.
The ILLIG IC is designed to achieve productivity, reproducibility, availability and operating convenience of a thermoforming machine or a complete thermoforming line. Installed, camera-supported quality control systems also contribute to achieve the target of speed increase; they record information on machine standstill and malfunctions. Checks of almost 100% performed on formed parts allow comprehensive data analyses for an identification of further influencing factors during extrusion or thermoforming and also for an early detection of wear or malfunction of the lines.
Mr. Schäuble said: "We are convinced that by optimizing the so-called planned standstill times we can considerably improve the productive running time of thermoforming lines.” ILLIG also meets the requirements of the trend that batch sizes of packs are getting smaller in many sectors which calls for shorter tooling times. Cleaning intervals are also a major factor. so increasing hygiene demands can be met. Here, ILLIG is developing solutions so dust development during material transport in the machine or during punching is prevented, as well as lubricant or oil ingress.
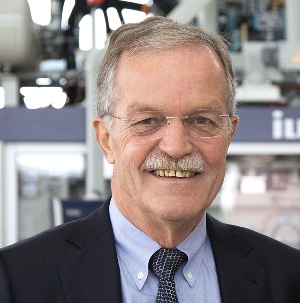
Mr. Karl Schäuble, Managing Director - ILLIG
ILLIG Maschinenbau GmbH & Co. KG
Tel: +49 (0)71 31 / 5 05-2 36
Fax: +49 (0)71 31 / 5 05-12 36
E-mail: info@illig.de
Website: www.illig.de
MATERIALS AND COMPOUNDS
Megatrends bring expanded use for plastics
Responding to Megatrends has become a main concern among many companies in the plastics industry. Clariant, for instance, has been focusing on the global Megatrends influencing the plastics industry and this was visible at its K 2016 presence as the company demonstrated how it is bringing true value to the industry based on the real needs of people arising from these trends.
Clariant's commitment to delivering Value for People was summarized by Executive Committee Member Christian Kohlpaintner in the context of the trends driving the challenges of its plastics industry customers. "Our customers in the plastics industry require a mixture of tailor-made innovation and volume driven support in order to address the needs being accelerated by global Megatrends. Our particular focus on innovations is underlined by sustainability because these are priorities connecting both. By supporting our customers developing innovative and sustainable solutions, this is how we can create most Value for People."
Mr. Kohlpaintner drew attention to four global Megatrends impacting the plastics industry: Health & Nutrition, Lifestyle, Mobility, and Urbanization. To provide optimum support to its customers and end-users, Clariant's services and solutions for plastics applications address aspects such as safety and comfort, more efficient and environmentally-compatible production, and reliable cleaner energy.
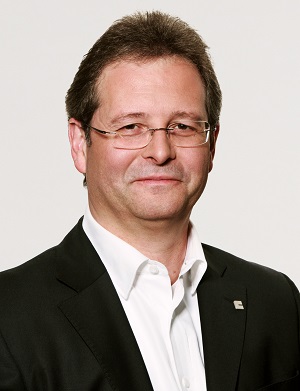
Mr. Christian Kohlpaintner, Executive Committee Member - Clariant
Clariant Masterbatches (Shanghai) Ltd.
Tel: +86-21 5442 6515
Fax: +86-21 5442 7961
Website: www.clariant.com
Advanced materials target ASEAN market
The demand for high performance materials continues to rise owing to the expanding requirements of customers for new compounds. For companies, the ASEAN market is an attractive destination but stringent regulations must still be met in terms of performance and environment impact.
Titan Plastics Compounds Co., Ltd of Taiwan sees the ASEAN market as a fast-growing region for its range of materials. According to Robert Chang, General Manager, the company launched its PA6T–high temperature nylon composite material under the PA series. “PA6T presents excellent temperature sustainability, and low water absorption that would solve the general problem of nylon’s high water absorption. The melting point is up to 315 Celsius. PA6T therefore meet the requirements for automotive and machinery industries that are exposed under long term high temperature.”
PAMXD6 aromatic nylon composites released by the company features high rigidity, stable size change (small alteration in rigidity and size before and after water absorption). It is suitable to apply in processing precision parts as in the electronics, automobiles, scooters manufacturing industries.
Mr. Chang sees several factors affecting the company’s operations and markets in 2017 and beyond. For one, China’s economic and market conditions would be a significant factor as this will affect industries including automobile, automation machines as well as the construction industry where huge amount of plastics is used. “Also, the economic situation in Europe and the U.S. would affect the people’s consumption behaviour, and would bring direct and indirect influence to cars, daily consumer products and also the housing market, which indicates impacts on plastics demand,” he added. The ASEAN bloc and emerging powers such as India are critical as well, and economies in these regions must keep growing to stimulate the demand for plastics, he stressed.
For 2017, the company’s high performance materials will play an important role in enhanced production process. “We are looking forward to the industrial automation issue. In order to realize automation, the machineries would need a lot of high-end and high capacity plastics materials. This demand fits Titan’s product features, and we are investing in developing high capacity industrial plastics that can be applied in green energy (electro cars, scooter), and also in automobile parts to reduce weight and cut energy consumption. In short, high capacity industrial plastics will replace metals, and Titan is closely following this trend to satisfy customers demand,” Mr. Chang explained.
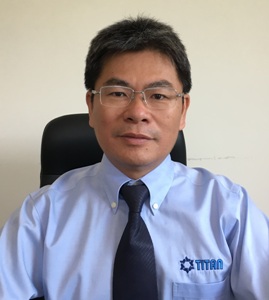
Mr. Robert Chang, General Manager – Titan Plastics Compounds Co., Ltd
Titan Plastics Compounds Co., Ltd
Tel: +886-8 752 2966
Fax+886-7-752 2066
email:robert@titan-plastic.com.tw
www.titan-plastic.com.tw
INDUSTRY SECTOR
Future of automotive lightweighting
Lightweighting still is the number-one automotive trend for plastics, according to Wim De Vos, CEO, SPE International (www.4spe.org). The continued substitution of heavy metallic and glass materials by lightweight plastic and composite structures is ‘fueled' by regulations and the rise of the electric-powered car. “We will start seeing more plastic wheel-rims, plastic engine parts, even more body panels, plastic glazing, etc. The vision of a full plastic car slowly becomes reality. Another trend is the so-called ‘plastronic’ parts where electronic functions are integrated into the plastic part. With the rise of ‘connectivity’ and ‘data intelligence,’ these become increasingly important,” Mr. De Vos explained.
Regulatory changes are only one element in the move toward lightweighting, according to Mr. De Vos, “but the encouragement comes mostly from several megatrends, such as efforts for greater environmental protection and conservation of natural resources, our continuous desire for more and better comfort, and ultimately the evolution of our social behaviour in which we strive for constant connection to our friends, family and to a diverse set of news feeds.”
Mr. De Vos sees several factors affecting the use of plastics in the automotive industry. “First of all there could be some small shifts within the plastics materials used. Plastic is not always replacing metal, sometimes a commodity plastic is replaced by a higher performing engineering polymer or even a polymer composite.” Regarding the overall polymer demand, in the end all trends are impacted by cost, so if oil and gas prices substantially increase again, then the use of plastics might be economically less interesting for OEMs. This is for me the only risk, he added.
The rise of the electric car will see an increased use of plastics in structural elements and large parts in an effort to reduce mass and increase vehicle range. “Compare it with what we saw in the racing industry some decades ago. Look at cars like the BMW i3 and the Reva (electrical car for Indian OEM Mahindra); these cars are using plastics for components that in most standard vehicles are still normally metallic. On the Reva, for instance, all the body panels are thermoformed ABS-PC-PMMA,” Mr. De Vos said.
One of the more difficult trends to predict is the increasing use of 3D-printed parts for serial vehicles, according to Mr. De Vos. While additive manufacturing has become standard in prototyping, it now makes its slow entry in very-low volume, small, complex serial parts. It is quite clear that for any real breakthrough into higher volume and mid- to larger part segment, the technology will have to make a quantum leap on production speed (faster) and material cost (lower).
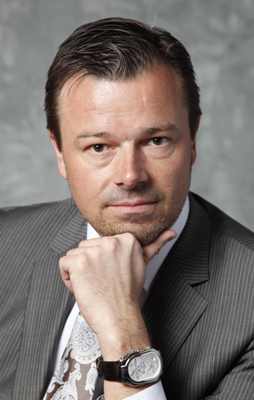
Mr. Wim De Vos, CEO, SPE International
Society of Plastics Engineers (SPE) International
Tel: +1-203 775 0471
E-mail: news@speautomotive.com
Website: www.4spe.org
Launch of new breed of medical polymers
The medical sector is benefiting from the latest developments in engineering plastics as most of the new high performance materials are geared toward the production of medical supplies and devices. Ever Polymer Co., Ltd, a leading manufacturer of materials and compounds in Taiwan, has launched several products geared for the medical/pharmaceutical sector. “We launched new product series EverMedi and Everseal. Evermedi is mainly for medical and pharmaceutical industry produced from our Cleanroom 100000. This material is ideal in the production of items such as medical stopper, tubing, sealing , medical equipment handle grips. It’s a good replacement for soft PVC and can meet customers’ requirement for more environmental-friendly material. Eversealis food grade material is widely use to produce cap liner and can provide flexible and excellent sealing for consumer products,” Mr. Tan, Asia Distributor General Manager, said.
The overall economic slowdown still affects the industry, especially for automotive and construction industry in 2017, according to Mr. Tan. “Despite this condition, we are still embarking on new developments for certain automotive models which we hope to launch in the years 2018-2019 and beyond that.” Mr. Tan expects the year 2017 to see sluggish market demand but the company intends to focus on specialty market where customers require customized material in medical and consumer industry.
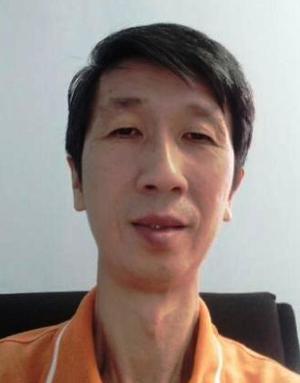
Mr. Tan Wei Kar, Asia Distributor General Manager – Ever Polymer Co., Ltd.
Ever Polymer Co., Ltd
Tel: +886-3 312 5717
Fax: +886-3 312 5718
Email: Everlon@everlon.com.tw
Website: www.everlon.com.tw
Expanding applications drive growth
GRECO (Great Eastern Resins Industrial Co., Ltd) sees emerging applications as important areas for growth and development. As Duke Shih, Sales Department Manager, said that the plastics industry is undergoing a period of transition and affected by various factors, among them, environmental concerns. “As a result, raw material suppliers are now struggling to protect the consumer’s welfare and this will lead to the development of advanced materials,” he said.
GRECO produces water-based PU adhesives, (ISOTHANE) TPU resins, dry-film Photoresists, and special chemicals as required by customers. “The exploration efforts to meet new applications of plastics is leading to the development of new products, and GRECO’s experiment on new materials is expected to become the basis for future products,” Mr. Shih explained. GRECO is actively developing a combination of long glass fiber in composites, becoming the first in Taiwan to be committed in the R&D of the new technology. The new material will have the strength and durability with rigidity that is 40% stronger than aluminum. “The next step for GRECO is entering a fast-rising automotive sector, where lightweighting has demanded increased application of plastics,” Mr. Shih said.
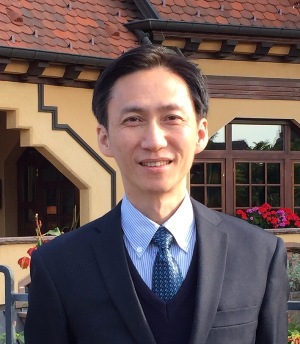
Mr. Duke Shih, Sales Department Manager - GRECO
Great Eastern Resins Industrial Co., Ltd
Tel: +886-4 2358 7676
Fax: +886-4 2358 1296
E-mail: angie@greco.com.tw
Website: www.greco.com.tw