Injection stretch blow molding (ISBM) for the production of various types of containers has been well accepted owing to its cost-efficiency and high-volume production capacity. The plastics industry has gained tremendous benefits from innovations in this area. The process has enabled the production of high quality and high clarity bottles. And the most commonly used material, polyethylene terephthalate (PET), has been able to match with the clarity and aesthetic appeal of glass, aside from having excellent barrier characteristics against carbon dioxide and oxygen, lighter weight, high breakage resistance, accurate dimension, thermally stable and suitable for hot filling, and recyclable.
Injection stretch blow molding of PET has taken a major leap with the introduction of a new ISBM technology by Nissei ASB Machine Co., Ltd. The company is set to hold the world premiere of its ASB-150DPX model with daily live molding demonstration of a complete molding system. The ASB-150DPX expands the company’s flagship ASB-150 based models to three variants: ASB-150DP, a single row molding up to 16 cavities, for very large bottles and jars; ASB-150DPW, a double row molding of medium sized bottles and jars up to 32 cavities; and ASB-150DPX, a triple row molding of small bottles in 36 or 48 cavities.
All models are built on a common architecture so factory layout, key functions, spare parts, maintenance and operator training are common to all, however the newly added DPX model has specific design features to maximize efficiency in small container molding. The model’s injection clamping stroke is optimized for short cycle small containers with upgraded hydraulic components provide faster cycle of injection clamping while maintaining smooth machine movement. Its servo hydraulic pumps offer up to 30% reduction in energy consumption, while the blow air circuit is optimized for small container production offering up to 50% reduced air consumption over standard systems.
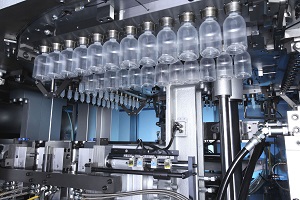
Although these features were introduced for the ASB-150DPX, some features are also planned to be available in future updates of its stable-mates ensuring that the entire model range maintains its lead over the competition.
This introduction of triple row one-step injection stretch blow molding is another in a long line of global firsts that Nissei ASB has achieved throughout nearly 40 years at the forefront of the PET container industry, with several areas of the machine design having patents pending or already approved.
Improving one-step molding technology
Held every four years in Munich, Germany, drinktec provides the role of world economic summit for the beverage and liquid-food industry. As such, in its role as world leader in one-step molding technology Nissei ASB takes great interest in not only monitoring but also in contributing to the industry trends on show at the exhibition. At drinktec, the ASB-150DPX will be conducting daily molding demonstrations of a 100ml, 5.3-gram yoghurt drink container. This lightweight container design requires a very short preform that would be impossible to handle and re-heat in a two-step system so the one-step molding process, where the container is formed directly from resin within one machine and held securely by its neck throughout, is the only practical choice. The smaller the container is, generally the more advantageous it is for production using a large one-step machine with high outputs.
With its triple row molding layout allowing 36 blow cavities, and at a cycle time of 6.4 seconds the ASB-150DPX will achieve a production rate in excess of 20,000 bph. Even if a container design such as this could be molded by re-heat blow molding, the required floor area for a similar capacity two-step production unit is typically 3-4 times greater, so this one-step solution provides not only technical superiority and enhanced quality, but manages to achieve it in a significantly reduced production space.
With the recent rise in prices of PE/PS materials, demand for PET conversion of this type of small container is increasing with numerous specific inquiries from major food manufacturers so the company is confident of good demand for this new model.
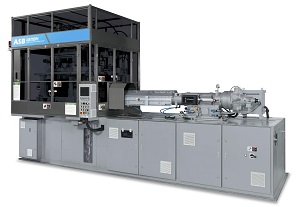
Nissei ASB Machine has brought several developments in the ISBM field during the K 2016 of which one of them was a version of the PF-24-8B/12 or the “1.5-step” ISBM system that combines the best of one-step and two-step processes to achieve high volume output rates in a compact model. The linear system has 12 preform cavities and four blowing cavities, and accumulates the preforms, which are allowed to cool only to the glass-transition temperature before blowing. A new sequencing system combines batch molding and cooling of preforms with continuous oven heating.
The enhanced model featured several advantages, among them is the ability to mold a deep pinch-style handle in large PET jugs. An external add-on hydraulic power unit is used to drive forming parts within the blow mold so that the shape of the cavity changes during blowing, to enable the production of shapes that were previously impossible. The same mechanism can also add inserted PP or HDPE handles that are mechanically locked into the bottle during blowing. Another feature is neck orientation with an integrated register on the neck of the preform to enable alignment to a specific thread position before entering the blowing station. This feature is said to be valuable with ovalized preforms for high-ovality or pinch-grip containers and for containers with flip-top caps or closures with some sort of pouring aid.
In January 2017, Nissei ASB Machine Co, Ltd. added a new capability as it started offering specifically adapted for molding high-end water bottles and baby feeding bottles with Eastman Tritan™ copolyester. To optimize processing and bottle quality using Tritan, Nissei has enhanced the daylight of its standard DPH machine to accommodate a longer preform, which improves ISBM results with Tritan. Enhanced clearance also allows a larger injection unit size than previous models. The versatile ASB-70DPH was shown at Plastivision 2017 producing high-quality sports bottles made with Eastman Tritan™ copolyester onsite. The one-step machine was running four-cavity mold to produce a bottle that weighs 90 gms, in a 14-second cycle time. The bottle offers all the advantages of Tritan, including crystal clarity, outstanding scratch resistance and durability, and the appeal to the health-conscious consumer of being made without bisphenol A (BPA-free).
Another development is the best-seller ASB-70DPH ISBM, a one-step machine with a double-blow system for heat-set PET containers. In the past, that feature was only available on two- station machines. The ASB-70DPH/ DB is a “mid-range” 70-ton machine for molding bottles for sauces and vitamin drinks that require hot-filling at 85-90oC (185-194o F). This four-station rotary machine accommodates two blowing cycles per injection cycle using two sets of molds in the blowing station with a servo-driven shuttle. Cycle time is said to be unaffected by double blowing. The machine has servo hydraulic drive and air recycling for energy savings. Injection clamp daylight has been extended up to 700 mm for molding longer preforms of non-PET resins, and an optional injection unit offers added capacity.