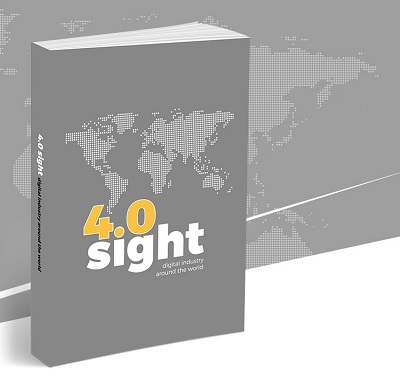
For the past several years, Industry 4.0 has been the buzzword going around the industrial world. Its description has morphed from modular automation, to cloud computing, and has been called by many names: Society 5.0, Smart Industry, Industrie du Futur, Industria Conectada 4.0, Manufacturing USA and Made in China 2025. A recently published book, “4.0 Sight: Digital industry around the world”, by Mark Proctor and Jonathan Wilkins, explores how the lasting impact of this shift from the current information age (Industry 3.0) to the Fourth Industrial Revolution has spurred countries to take action.
Covering a range of topics from the history of Industry 4.0 to the latest trends in automation, the book features interviews from leading experts from ABB, Toshiba, Renishaw and GE, who presented their unique insights and personal experience of their respective industries’ ongoing transition to Industry 4.0. As Mr. Wilkins puts it: “The digital finishing of production plants and industrial products through to everyday products with integrated memory and communication capabilities, radio sensors, embedded actuators and intelligence software systems, creates a bridge between the virtual 'cyber space' and the real world through to fine - grained synchronisation between digital models and the physical reality.”
Aside from the latest trends in automation, the big nine technologies changing industry were tackled: social media, big data & data analytics, artificial intelligence, cloud technologies, Internet of Things (IoT), mobile services, robots & automated machinery, cyber-security solutions, 3-D printing and finally artificial intelligence (AI).
Although most businesses agree that technology will change the industrial sector in the coming years, many have been reluctant to adopt digital technologies. Social media, big data & data analytics, artificial intelligence topped the EU Commission's Digital Transformation Survey with less than 35% of the respondents adopting the listed key technologies. 3-D printing and AI ranked lowest in the EU survey with less than 5% of respondents.
It did not come as a surprise that social media leads the list of the key technologies across the board. Mobile device users topped at nearly 4.7 billion in a 2017, based on Vaciniti Media survey, with the prediction of the number going way over the 5 billion mark by 2019. More than half of the users are located in the Asia-Pacific region. As such, "there are now more than 50 million small businesses using Facebook Pages to connect with their customers,” according to Sheryl Sandberg, Facebook's chief operating officer (COO).
Consumers have certainly upped their game. 32% of social media users expect a business to respond within 30 minutes and more than 42% expect a response within 60 minutes. Likewise, firms that have adopted social media have found it a great platform to engage with customers. Aside from Facebook, LinkedIn counts as one of the business social media leaders with its publishing platform, sponsored posts, company pages and forums. Both are great ways for industrial businesses to reach their targeted audience.
Transition to new technologies
Most business in Asia, especially plastic manufacturers combine two or three of the key technologies in their bid to transition to Industry 4.0. A combination of big data & data analytics, cloud technologies plus IoT, are what early adopters use to optimise and transform their manufacturing operations.
It used to be that data was a stagnant and paper-downloaded item not really prioritised by companies and business. In this digital, Internet-driven world, data is churned out in huge amounts every millisecond. Businesses see the importance of collecting and harnessing these data, segregating the “chaff” from high-quality relevant information. The next is to find insights from the gathered relevant data and use it to get ahead of other competition in the market. As such, companies can now use business intelligence (BI) and computerised maintenance management systems (CMMS) to do much of this legwork.
According to the 4.0 Sight book, cloud technologies adoption also varies in terms of company size, with 10% of adopting companies having more than 250 employees. The same survey, conducted by DTS, reveals that the figure rises to 30% for companies that employ between 10 and 50 staff. Despite this, over 88% of all companies surveyed said that the adoption of cloud has generated positive outcomes, with some using it to enter new markets and others to gain new customers. Those who are reluctant to migrate their data to cloud technologies cite data privacy and cybersecurity concerns as the main reasons of the sluggish adoption.
The main concept associated with the Fourth Industrial Revolution is the Internet of Things (IoT), which consists of physical devices that use embedded electronics, software, sensors and actuators connected to the internet. IoT encompasses home appliances, such as kettles and toasters as well as industrial machines such as pumps and motors. By integrating the physical and digital worlds this way, the network can exchange data to deliver efficiency improvements, reduce costs and free-up man hours.
Research firm Gartner estimated that there are more than 11 billion connected things used worldwide in 2018. In smart factories, IoT allows engineers to improve traceability, add remote monitoring and predictive maintenance, which alerts the plant manager of an imminent equipment breakdown before it fails. Connectivity also enables the plant manager to transform previously 'dumb' legacy equipment into smart machines that can be tracked in real time from anywhere in the supply chain.
To illustrate the successful merging of these key technologies, one Southeast Asian company has fully digitised over 30 facility operations, in a bid to rise from a Tier 2 supplier to Tier 1 status. This would push the company not only as a local producer for the Asian market but as a world- class supplier with capabilities to provide just-in-time premium products.
Industry 4.0 seems to be an easier idea for the tiger economies to implement despite the challenges. One example is Singapore, which has embarked on ambitious projects such as the SMART Nation Vision and provided tremendous support for SMEs and MNCs to modernise, upgrade and improve productivity and efficiency. Singapore has the perfect tools such as highly educated populace, along with a well-connected physical and IT infrastructure, to become the global leader in manufacturing productivity and quality. But Arcstone Pte. Ltd. CEO Willson Deng warns that this may not be enough to support Singapore in the next 50 years: “Just as Singapore set out to establish the infrastructure and framework to bring about the first wave of manufacturers to flock to the island nation, Singapore must now look at setting up the new digital and intelligent infrastructure and ecosystem to keep and attract the next wave. Individual SME and MNC support will not be sufficient to ensure the manufacturing sector as a whole remains competitive. Driven by market forces, price competition and ever higher quality requirements, manufacturers are faced with a host of new obstacles to overcome. Therefore, the need for an intelligent manufacturing ecosystem and mindset will be the make or break factor for the future.”
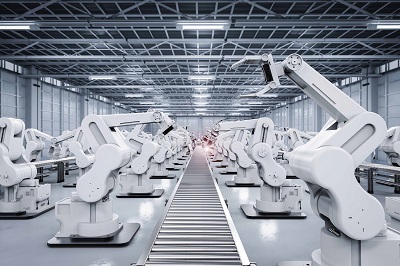
China has taken lead in automation and robotics in its industrial processes. In an interview CEO of TM Robotics, Nigel Smith, shares that: “China is one of the core markets for Toshiba Machine, which is why it recently opened a manufacturing facility in China, within the already existing Toshiba Machine Shanghai Co. factory. This facility predominantly manufactures SCARA robots for the growing electronics assembly market in China.” However, this high-volume demand is creating an industry-wide shortage of many second and third-tier components used in robots. Parts such as Harmonic Drives, RV gears and ball screws are responsible for delivering the lightweight and high accuracy articulation and motion that we've come to expect of robots. Alternatives to these components exist from local suppliers in China, manufacturers value the high quality, precision and reliability of Japanese and German parts. As suppliers work to reduce lead-times, Mr. Smith expects supply to catch up with demand.
What these challenges show is the diverse range of journeys that different countries are taking to digitalise. If not addressed, the resulting fragmentation between nations may lead to the stunted growth of change initiatives around the world. There are also a number of insightful observations and predictions on how the technological landscape will change in the coming. The book is a good fount of information on the key trends and the challenges faced for Industry 4.0 proponents and the struggles and challenges they are encountering in the quest to embrace the future of advance manufacturing.