Injection moulding machines producers offer machines in various sizes and variants to meet the diverse requirements of customers. Manufacturing sectors such as automotive, packaging, healthcare, and others, create high demand for various types of injection moulding machines. This trend is further spurred by the changing lifestyle of consumers whose preference for frozen foods, as well as convenient and ready-to-eat foods raised demand for injection moulded plastics products. The global injection moulding machine market was estimated at $15.26 billion in 2017, and is projected to reach $22.32 billion in 2025, growing annually by 4.7%, according to ReportLinker. A large segment of the industry focuses on automated injection moulding machines to ensure energy efficiency.
Servo-hydraulic injection moulding machines have carved a special place in the market. This type of injection moulding machine is run by a servo motor to drive the hydraulic pump, creating a cost-efficient operation that can meet the needs of plastic products manufacturers as well as those in the automotive sector.
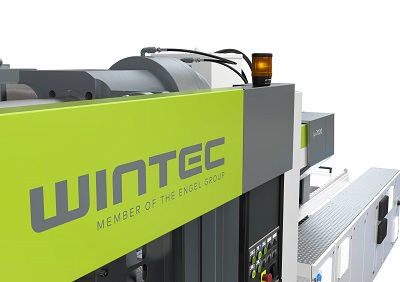
The t-win injection moulding machines from Wintec are available in 6 sizes with clamping forces of between 4,500 and 17,500 kN.
One example of a machine that has been designed and developed in Europe but built in China is the t-win series of servo-hydraulic machine produced by Wintec. A member of the ENGEL Group, Wintec offers injection moulding machines for single-shot applications. The streamlined portfolio is targeted to best meet the requirements of standard plastics production.
.
Wintec t-win series of servo-hydraulic two-platen presses from 500 to 1900 U.S. tonnes are currently used mainly in the automotive and white-goods sectors. Their clamps ride on linear guides and they have a KEBA C2 controller with tilting 15-in. touchscreen. The t-win series boasts of a high degree of energy efficiency and sensitive mould protection. The hydraulic injection moulding machines of the series are offered with clamping forces from 4,500 to 17,500 kN, and are thus ideal for the production of large or three-dimensionally complex components. At an exhibition in China, a t-win 10500-7000 injection moulding machine with a clamping force of 10,500 kN was demonstrated to highlight the performance of the series with the production of automotive interior door panels from polypropylene. The shot weight is 650 grams, each cycle takes 30 seconds.
Reduction in energy consumption
Even in the standard version, the t-win machines are equipped with the servowin servo-hydraulics, which reduces energy consumption by more than 60% as compared to conventional hydraulic injection moulding machines. Additional factors that contribute to a high degree of energy efficiency are the operating point optimisation and the dual-platen design of the clamping unit with low moving masses and exposed tie-bars. The linear guidance of the movable mould mounting platen reduces friction and keeps the mould area free of lubricating oil.
The dual-platen clamping unit was developed in Europe and guarantees maximum platen parallelism throughout the machine’s service life, which results in sensitive mould protection, excellent dynamics and short dry cycle times. Parallel auxiliary movements such as the ejector, core pulls, or jets, are optional possibilities.
The C2 control installed on all Wintec injection moulding machines is characterised by an intuitive operator guidance that reduces the risk of operator errors. The entire machine status is displayed on a clear-cut single screen. A quick adjustment page groups the most important setting parameters in a compact way. In addition, the C2 offers ample flexibility in terms of connecting robots of various types and brands. As a member of the ENGEL Group, Wintec is in a position to deliver integrated production cells from a single source, with robots developed and produced in-house. The t-win 10500-7000 can be equipped with a viper 20 from ENGEL's linear robot series. The viper removes finished parts from the mould and places them on the conveyor belt.
The servo-hydraulic two-platen t-win is the economic machine for single-shot application. Applying decades of experience in injection moulding the entire machine design is focused on fast and energy efficient production: from white goods to automotive or technical parts.
High output, consistent part quality and maximum machine availability are key to high productivity. With the t-win series Wintec is looking ahead, offering an alternative to reduce Total Cost of Ownership. The combination of high productivity, energy efficiency, easy operation and maintenance ensure return on investment. The extended service life – guaranteed by proven design, premium components and highest quality standards in production – makes the customer’s investment profitable for many years in the future.
Upgraded solutions
In the spirit of continuous improvement, several upgrades and new features have been added to the best-selling Mars Series injection moulding machines from Haitian (from 67 to 3,709 U.S. tons). Haitian Plastics Machinery’s Haitian Mars Series servo-hydraulic injection moulding machines reached a historical record of more than 200,000 installed machines worldwide in 2018. The MA II S Series is more efficient and precise version of this best seller and steps up its capability including: deduced overall footprint for higher productivity per square foot; faster clamp movement for improved dry cycle times yet lower energy consumption; ball-type linear guide rails on the clamp reducing friction resulting in smoother clamp movement; lower platen stress and improved mold force stability reducing mould wear; reduced oil capacity requirement for lower cost and improved environmental sustainability; copper graphite bushings for the rear platen, stationary platen and toggle that are high load bearing, providing good abrasion resistance and decreasing the need for lubrication; balanced twin injection cylinder design with additional guidance; improved injection unit pivot design for easier screw and nozzle changes; and increased open space at clamp end for conveyors
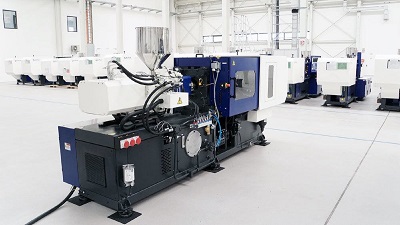
The MA II S Series is more efficient and precise version of this best seller from Haitian Plastics Machinery
The diversified range of injection moulding machines in the Haitian Plastics Machinery portfolio covers all the applications in the standard sector, and fulfill international quality standards. The Mars IIS series is one of Haitian’s best-selling models.
Changes from Mars II include the screws and cylinders, whose design has been upgraded (shorter screws, longer screw tips). There are important upgrades in the system pressure and injection unit. In addition, the oil tanks on the MA IIS have been downsized in order to lower the consumption costs and increase eco-friendliness. The clamping force has been increased with the new FAP frame structure (60-250 tonnes) and optimised toggle for mould close movement has also been made possible.
The injection-unit linear guide has been enhanced for more stability and less friction, with swivel-out injection unit for faster screw exchange. The optimised injection unit achieves higher pressures. Moreover, the standardised interior design of the MA IIS and the eco version works towards even shorter delivery times. The machine also features improved V4 software, improved built-in oil cooler and greater oil cleanliness from modified oil filter system.
Kids Nike Cortez