EHLA is significantly faster than conventional laser deposition welding.
The new EHLA method capable of extremely high laser deposition welding speeds enables laser systems to coat large-area components at a rate of over 250 square centimeters per minute.
In Germany, EHLA stands for extreme high-speed laser deposition welding. EHLA is significantly faster than conventional laser deposition welding. The laser system manufacturer TRUMPF is putting the new EHLA method into series production.
“For EHLA, we can draw on similar techniques that we’ve been using for laser deposition welding,” explains Antonio Candel-Ruiz, an expert for laser surface methods at TRUMPF in Ditzingen. The Fraunhofer Institute for Laser Technology (ILT) developed and patented EHLA, with the primary aim of executing coating processes very quickly with low layer thicknesses for rotationally symmetric components.
A tried-and-true method in metal coating for many years, laser deposition welding delivers high-quality results. This method makes it possible to manufacture crack-free and virtually pore-free coatings with metallurgical bonding to the substrate out of a variety of materials.
“For large-area coating tasks, however, lasers have lacked the necessary speed,” says Candel-Ruiz. In addition, the minimum layer thickness was around 500 micrometers; thinner layers simply were not possible.
How EHLA works
Laser deposition welding normally proceeds as follows: a laser generates a weld pool on the surface of a component and fuses the metal powder, coaxially added simultaneously, to create the required shape. The powder then fuses with the surface, gradually forming a protective coating. In the EHLA method, the laser light strikes the powdery filler material above the weld pool, heating the material nearly to its melting point while it is still on its way to the component.
Consequently, the particles melt faster in the weld pool. This makes it possible to use energy much more efficiently. Whereas normal laser deposition welding can coat only 10 to 40 square centimeters per minute, the EHLA method achieves rates of over 250 square centimeters per minute. In addition, much thinner coatings with layer thicknesses of 10 to 300 micrometers are now possible. What’s more, EHLA permits a much finer laser focus, rendering the process considerably more energy-efficient.
TRUMPF meets EHLA
The new processing optics developed by Fraunhofer ILT can be integrated directly into existing TRUMPF systems.
“Our diode lasers and our disk lasers are suitable for EHLA, depending on the laser focus required,” says Candel-Ruiz.
With diode lasers, a focus of around one millimeter is possible; with disk lasers, a focus as small as about 0.2 millimeters. In addition to the laser beam source, another decisive factor is that the machine has a rotational axis that permits high speeds.
Depending on component size, TRUMPF has various laser machines that are candidates for EHLA. The TruLaser Cell 3000 is suitable for small and medium-sized components, while the machines in the TruLaser Cell 7000 Series are suitable for large ones. Apart from these turnkey systems, manufacturers can integrate the EHLA method into their existing systems. The DepositionLine technology package from TRUMPF can also be equipped with the new powder feed nozzles developed by Fraunhofer ILT.
EHLA developers Thomas Schopphoven, Gerhard Maria Backes, and Andres Gasser said that EHLA better at corrosion protection. In terms of thermal spraying, EHLA offers a much more efficient and economical use of resources – while the new process uses about 90% of the coating material, thermal spraying wastes a lot of the material and gas. Only about 50% of the material used during thermal spraying actually coats the surface of the component, and the layers only have a weak bond to the substrate; in addition, because thermal sprays are so porous, you need to apply several 25-50 micrometer thick layers. Comparatively, the individual layers of the EHLA process are non-porous, and have a firm substrate bond.
Hard chrome plating is one of the most common processes when it comes to applying corrosion and wear protective coatings, but it also consumes a large amount of energy. Not only that, but because chromium (VI) is harmful to the environment, it can only be used with specific authorization starting this September. For companies that want an eco-friendly alternative, the EHLA process is the way to go. It offers chemical-free application: each layer is metallurgically bonded to the base material and won’t delaminate like hard chrome layers will. EHLA-produced layers offer more efficient long-term protection because they’re non-porous, as opposed to the cracks and pores that riddle hard chrome plating layers.
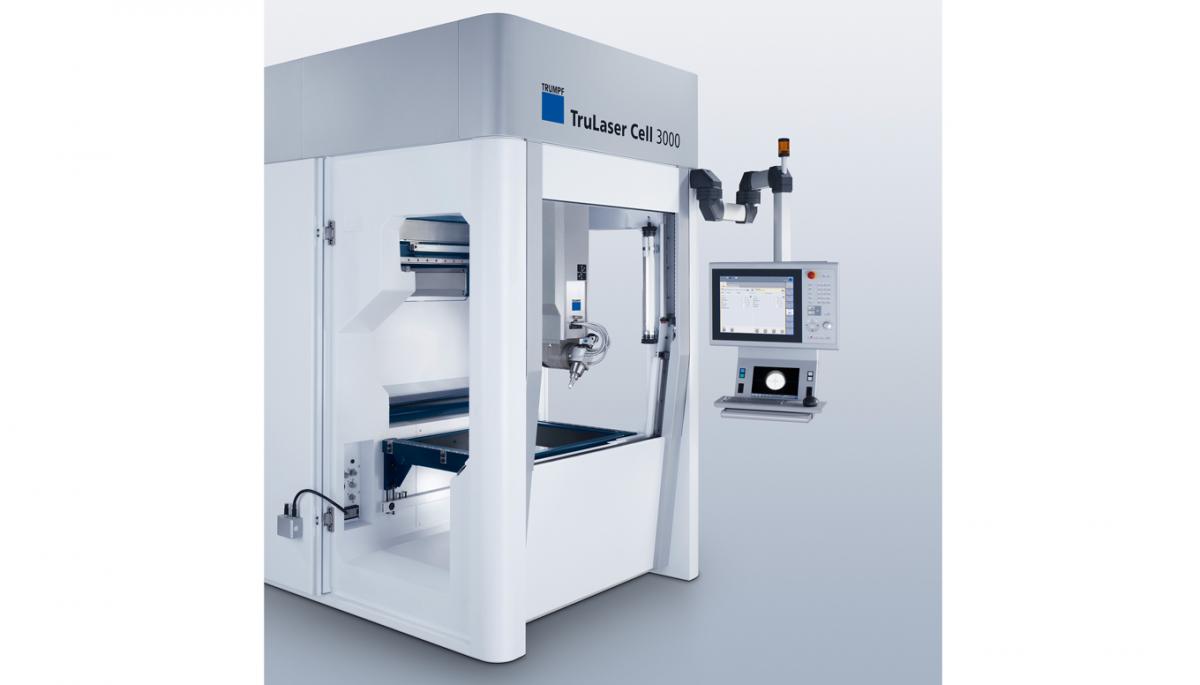
Nike Air Max Plus TN