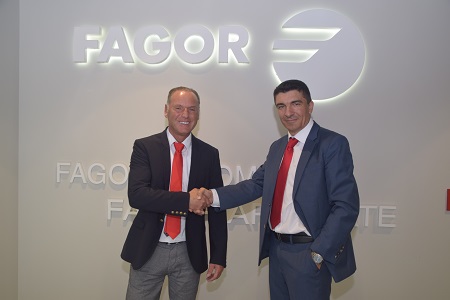
(L-R) Gerald Schulz and Aitor Ormaetxea
Fagor Arrasate has taken a new step forward in its strategy to position itself as a leader in the hot stamping industry by incorporating the talent, knowledge and experience of Gerald Schulz, hiring him as the new global sales director for Press Hardening. Schulz has a long history working in senior management and sales for AP&T, Magna, Gestamp Benteler, as well as Helmerding, Kemmerich, Hubert Schlieckmann and Siempelkamp.
Schulz, the former Sales Director (CSO) and Executive Representative in China of AP&T, the world leader in hot stamping, will add his experience and market knowledge to Fagor Arrasate's technological expertise.
In the last 5 years Fagor Arrasate has implemented important technological developments. The company has become a turn key OEM supplier and has completed several major projects with a delivery time of less than a year. As an OEM reference Fagor Arrasate has delivered two projects at Seat-Barcelona, one at VW Kassel and one at PSA/Opel Kaiserslaitern, as well as several press hardening lines in the TIER1 sector.
As such, Gerald Schulz believes that, with the level of technological development achieved by Fagor Arrasate, these recent benchmarks and the current quality-price ratio, "we have very good options for improving our sales in the global hot stamping market", particularly in Europe and China.
"I have been in the automotive industry for 29 years, and involved in the installation of many Press Hardening lines and the global business of the industry over the past 16 years. It is not just about the press; you have to see the whole process you need to have the knowledge and experience from production to offer the customer a profitable and customer accurate press hardening line. We at Fagor Arrasate have the experience and knowledge to succeed with our customers. In addition, our Mondragon Group offers its customers a stable, crisis-proof company with over 74,000 employees and a global turnover of 11.3 billion euros”, says Schulz.
"Thanks to Schulz’s sales experience and market knowledge we will now are able to exploit our technological potential to the fullest, which we have had the opportunity to demonstrate in recent projects. With the technical element mastered, now is the perfect time to strengthen our position in the Press Hardening sector, and Gerald Schulz is a key part of this strategy", declared Aitor Ormaetxea, the hot stamping director at Fagor Arrasate.
Hot stamping is an expanding market due to the need for vehicle manufacturers to redesign their platforms to adapt them to new market requirements. In particular, the need to lighten the chassis of vehicles resulting from the deployment of alternative energies and regulatory requirements on emissions, makes this technology the fastest growing in the stamping sector.
New equipment supplied to Volkswagen Kassel
The Turn Key press hardening line supplied for Volkswagen is equipped with two parallel roller furnaces, three freely programmable loading feeders and an end-of-line solution that allows fully automatic or manual racking.
It has three loading feeders and a powerful drive system for controlling the die. This new equipment enables each blank coming out of the furnace to be moved independently to the die instead of in groups.
This makes it possible for the furnaces to be smaller in size, given that after leaving the oven the pieces are separated to be stamped correctly. Thanks to this automation and the highly powerful hydraulic unit, the press is able to reach very high processing speeds.
The car manufacturer has placed trust in Fagor Arrasate for this project after the positive results of the two hot stamping lines installed in another of its plants. These lines are fully automated, both in the loading of forms and in the stacking of the pieces, and also have 2 parallel ovens for heating formats. For loading the press, they have a Fagor LR3-120 feeder that allows the hot formats to be transported quickly to the die, thus guaranteeing the quality and stability of the process.
The pieces, once stamped, are automatically placed in the stacking containers by a shuttle and 3 Kuka robots, so the process is completed entirely automatically. It also has an additional output belt for quality inspection of the pieces.
The endorsement received from earning the confidence of a manufacturer of this size, along with its significant experience in its own automation systems, provides Fagor Arrasate with the potential for major growth in the hot stamping industry. The company has a thorough knowledge of transfer and feeding systems, including milestones such as the installation of the first mechanical servo press in Europe.
All this expertise places Fagor Arrasate in an unbeatable position to consolidate itself as a leader within the hot stamping industry, a market which is expanding thanks to the progressive redesign of the new vehicle platforms. New requirements in emissions regulations and the need to lighten the chassis of electric cars make this technology the fastest growing in the stamping sector.
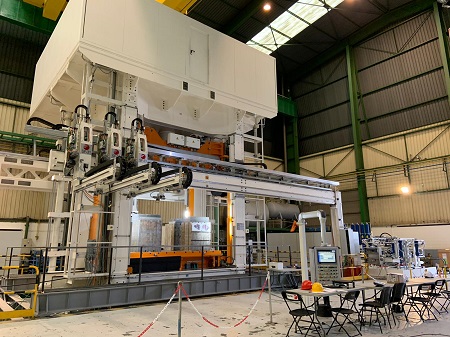
Fagor Arrasate hot stamping press
Nike Air Jordan 1 Mens