Thermoplastic components are fast gaining acceptance in various sectors, such as in the automobile industry, medical technology, telecommunications, electronics, safety engineering, packaging industry, household appliances, consumer goods and toys. When parts of macromolecular materials are to be bonded, ultrasonic welding is replacing conventional processes such as adhesive bonding or heat-staking. First and foremost, ultrasonic welding is sustainable and clean. Secondly, the process requires no additional materials (adhesives or fasteners) or expensive and time-consuming steps such as pre-treatment or drying.
The highly varied welding and bonding needs of different industries are being met by Weber Ultrasonics AG (www.weberultrasonics.com), a company that develops and produces standard and special solutions for ultrasonic welding. Equipped with innovative technology, the systems not only satisfy the tough demands for production speed, process reliability and reproducibility of welds, but also fulfill requirements for flexibility and long-lasting viability. Increasingly shorter product lifecycles, growing requirements for monitoring and documenting process parameters and the integration of quality assurance in the welding process demand flexible and intelligent systems like the ultrasonic welding solutions available with the Saphir platform. Additional challenges posed by networked production environments and globalized production sites can be met only with a system programmed to meet tomorrow's needs.
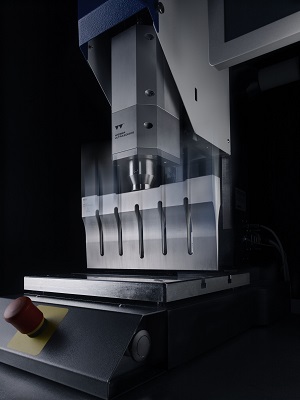
Maximum operational flexibility
As a modular welding solution Saphir can be used for standard machines and a variety of plug-in ultrasonic units for custom automation lines and can be expanded easily for other uses. The ultrasonic welding system is based on a ground-breaking generator and control concept. It satisfies prerequisites for the complete capture, monitoring and documentation of process parameters and integration of additional functions and processes such as automated elements and systems for sensory, optical and mechanical quality assurance. The integration of welding processes in networked production environments (the Industry 4.0 concept) can be realized with interfaces such as Ethernet, Profibus and Profinet.
The multi-functional process control and visualization are carried out on a modern touchscreen display, which combines quick access with user-friendly navigation. The pre-set operating modes – time, energy, absolute distance and relative distance– simplify parameter settings for the welding process. Access rights for process control can be protected by means of different password levels and, if required, can be personalized and expanded in keeping with the applicable medical standards (FDA CFR 21, Part 11). In addition, the system is equipped with many safety features based on the poka-yoke principle of preventing errors or incorrect parameter settings. All these features increase operational reliability, which is particularly important when machines are used at different locations around the world, and help to deliver consistently high-quality welding results. Remote maintenance of these applications ensures greater system availability. The extremely fast reaction times mean that breakdowns can be resolved rapidly and new functions can be implemented quickly.
The innovative process architecture enables the generator to make many settings automatically. Among other things, the welding parameters are automatically configured, monitored and optimized. For example, the generator measures working frequencies automatically prior to ultrasonic output and adjusts the system accordingly. The frequency is continuously monitored during the process and automatically adapted. This function makes sure that consistently high weld quality is achieved even under changing operating conditions and contributes to high process reliability and product consistency.
Welding systems customized
With ultrasonic frequencies of 20, 30 and 35 kHz and a power range from 400 to 5000 watts, the Saphir welding system covers a broad application spectrum in plastic bonding technology.
In the automobile industry for instance, Saphir is used to bond large surface engine covers with noise-suppressing foam lining and protective air plates with thermally stable and vibration-resistant welds. The insulating foam bond is made with welding points while the air plates are welded in a perforation process. To comply with the process reliability and documentation required by the automobile industry, the process monitoring system uses sensors to check whether the right parts have been inserted. After the automatic selection of the appropriate program has been made, welding parameters such as energy, force and distance, and the high frequency current received by the converters are monitored. Furthermore, during the welding process, information is captured and documented on the distance the sonotrode covers and how much time it takes along with the pneumatic retaining pressure and retention time. If all the values lie within the specified tolerances, the part is declared acceptable.
In medical technology, Weber used the Saphir system as the basis for a welding solution equipped with visual process monitoring. In this application, several single parts of a plastic pump are placed in the correct positions in the pump housing before the welding process is begun. Once the handling unit in the automation process has completed this step, an integrated industrial image processing system compares the photo made by the camera with the reference photo on file. The welding process is initiated only when the two photos match each other exactly.
Product consistency is extremely important in ultrasonic welding applications in the toy industry too. In this case the heads and bodies of small plastic figures are connected completely and automatically. To that end, the welding solution is equipped with a handling system that brings the two matching parts into the right position. A mechanical system is integrated in the welding equipment for quality assurance purposes. Once the parts have passed through the welding process, they are directed to a second handling unit in the testing system, where a tensile test is conducted with a pre-defined strength threshold. Only parts that pass this test are deemed acceptable. If a part fails, it is reliably removed from the production line via an ejection shaft.
By adapting ultrasonic welding solutions and peripherals to each type of application, Weber Ultrasonics makes it possible to design more stable and efficient processes which are capable of achieving consistently high quality.