Preform moulding solutions are now capable of meeting the most challenging tasks through enhanced machine performance that can cut down production costs.
Husky Injection Molding Systems has introduced its next generation HyPET™ HPP5e system. Building upon the proven industry-leading technology of the HPP platform, HyPET™ HPP5e is the result of significant technology improvements that work together to create industry-leading system solutions - delivering better energy savings, system reliability, preform quality and user friendliness.
“Husky originally launched the HyPET™ HPP5 system as the world’s most productive and fully integrated preform moulding solution capable of delivering the most challenging preform applications, without compromising system performance, output or quality,” said Rob Domodossola, Husky’s President of Rigid Packaging. “We have now taken this industry-leading solution to the next level by implementing a number of significant technology improvements that work together to deliver a smarter, more intuitive, more productive system that will increase customer value and competitiveness on multiple levels.”
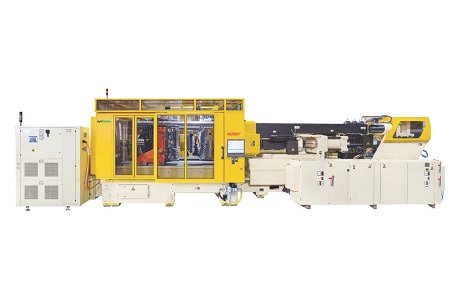
HyPET™ HPP5e from Husky Injection Molding Systems
Improved performance combined with energy savings
System intelligence is the key to HyPET™ HPP5e’s ability to intuitively reduce energy consumption, resulting in a considerable decrease in operating costs for customers. At the heart of the platform is an intelligent, adaptive technology that uses feedback from pressure and actuator sensors to determine the optimum pressure required to effectively and efficiently mold every application. This innovative smart system monitors and automatically adjusts for optimal energy consumption without impacting system capability, cycle time or part quality.
A number of modifications have been made to make HyPET™ HPP5e more robust and reliable. New conveyor technology significantly reduces preform bounce when parts are ejected from the CoolPik® unit to the exiting conveyor. This bounce reduction results in improved part quality, reduced scrap, more streamlined operation and decreased cycle interruptions. CoolPik® is an integrated part cooling handling system which features up to four cycles of balanced cooling on the preform’s inner and outer surface. When compared to alternate post-mould cooling systems, which only cool the outer surface, CoolPik® results in faster cycles, better part quality, improved effectiveness in downstream equipment.
Enhanced mould alignment software supports faster system set-up and troubleshooting. Other advancements include new robot linear bearings to maximise longevity, upgraded Altanium® Inside ICC cards for more integrated, accurate temperature control and a new nozzle shut-off cylinder to promote component longevity.
An evolution of the previous generation system, HyPET™ HPP5e has adopted new intelligent features and real-time control enhancements to simplify operation and optimise the moulding process. By integrating more intelligence into the system, operators of all skill levels are able to achieve maximum productivity and part consistency. HMI screen upgrades, software updates and improved EtherCAT diagnostics promote user friendliness, making the system easier to navigate, more convenient to set-up and issues faster to troubleshoot.
Husky HyPET™ systems are available in various tonnages for moulds. All components are specifically designed to work together as a fully integrated and optimised workcell. This makes it possible to achieve a stable process and reliable operation, which results in fast cycles and leading preform quality. All components of the HyPET™ system, including the hot runner, mould, machine, robot, and post-mould cooling are specifically designed to work together as a fully integrated workcell.
Accelerating the digitalisation process
Recent developments point towards delivering solutions that indicate Husky’s efforts to embrace digitalisation. The company unveiled a new groundbreaking digitalised end-to-end manufacturing execution process, the state-of-the-art Next Generation Operating Model (NGOM). During the launch of this model, Husky stressed the advantages of this pioneering new digitalised NGOM moulding solution.
“The world is experiencing an accelerated pace of digitalisation and it is influencing every aspect of our lives. Husky recognises this shift and we have been actively working to embrace digitalisation for some time,” said John Galt, Husky’s President and CEO. “The NGOM program revolutionises the way we do business, offering enhanced capabilities designed to deliver solutions with speed and flexibility, reduced overall cost, and a heightened, more accessible experience. Having an end-to-end fully digitalised architecture allows us to leverage our global capability and quickly scale to new opportunities, so that we can enable our customers to be more competitive and effectively respond to continuously changing consumer buying trends. We are very excited about this development and the possibilities it creates.”
Husky’s pioneering NGOM process has streamlined hardware ordering and manufacturing from a practice that historically takes several weeks down to a few hours. and showcased how the company has partnered with the Luxembourg Government Departments of Economy and Labor, as well as fellow industry leader Siemens, to develop a pioneering new digitalised NGOM moulding solution.
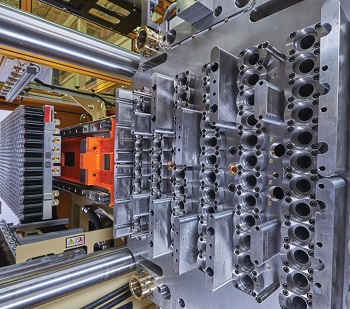
A mould in the HyPET™ HPP5e
For the first time ever, customised stack components can be configured through a web interface and are then manufactured in a state-of-the-art laboratory through a completely automated process. In addition, because the virtual and physical environments work together within a closed loop, the system is able to continuously improve on the products and services delivered. Information is fed back into the system so Husky’s subject matter experts can regularly improve upon quality and speed.
“This project is a tangible example of our digital innovation strategy in the priority sector of Industry 4.0. The project is fully aligned with our sustainable economic development policies that aim to support the use of digital technologies in the manufacturing industry. Our competitive business environment allowed such an innovative project to be implemented in Luxembourg, which contributes to the technical and human development of Industry 4.0,” said Etienne Schneider, Deputy Prime Minister, Minister of the Economy.
“An ever-increasing number of industrial enterprises worldwide are well on the way towards Industrie 4.0 and are already improving their competitive standing with digital solutions,” said Klaus Helmrich, Member of the Management Board of Siemens. “This applies to all sectors of industry with rapidly changing market demands in which products must be manufactured ever more quickly, flexibly and in diminishing quantities. We look forward to continuing to work collaboratively with Husky on advancing their capability in this area.”
Kicked off in early 2017, Husky first began working with the Luxembourg Government’s Ministry of the Economy and Luxinnovation to support research and development of an end-to-end digital environment proof of concept. As the project has gained momentum Husky is training a larger NGOM team, which is supported by the Luxembourg Digital Skills Bridge Program.
Throughout this same year, Husky also worked with Siemens on software development and overall process flow. NGOM began taking orders from pilot lines in 2018 and is now fully operational, producing parts for customers in real-time, with ongoing validation and closed loop to industrialise the solution. The system can connect to different Husky locations in both Luxembourg and Canada, providing global consistency and transparency among multiple manufacturing sites, while enabling unprecedented capability in speed to market for customers.