At K 2019, Starlinger is presenting a closed loop system for big bags made from woven polypropylene (PP). The sustainable concept “circular packaging” will be Starlinger’s main theme at the K show 2019 as well as at the Starlinger Open House in Weissenbach/Austria.
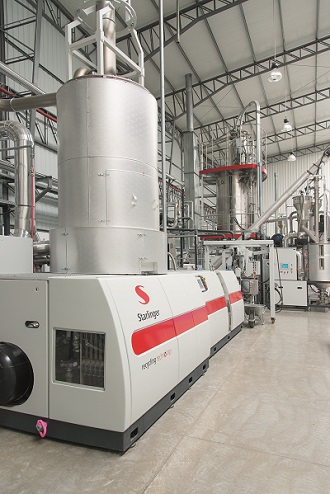
Worldwide, more than 380 million 4-loop big bags (called FIBCs in specialist vocabulary – Flexible Intermediate Bulk Containers) are sold every year; this equals an annual recycling potential of approx. 800,000 tons of material. To turn big bags into big bags once more, the Austrian Starlinger & Co. GmbH has now developed the concept “circular packaging” for big bags made from polypropylene fabric; the well-known FIBC expert Dr. Amir Samadijavan acted as consultant for this project. The sustainable concept will be presented at the leading plastics exhibition K 2019 in Düsseldorf/Germany; live demonstrations of the technology will be the highlight of the Starlinger Open House in Weissenbach/Austria.
With “circular packaging”, Starlinger introduces K show visitors to an elaborate concept for a closed loop for big bags that begins with PP granulate and leads back to polypropylene regranulate (rPP) through the process steps production, usage, recovery, and recycling. A closed loop has the advantage that production occurs within a quality assurance system, and the materials used are documented in a so-called “material passport”. In cooperation with the renowned big bag manufacturers Louis Blockx and LC Packaging, Starlinger has simulated this loop and produced new big bags from fabric with high rPP content. Samples are available at K show and prove that Starlinger rPP big bags show the same quality as big bags made from virgin material in terms of tensile strength, weight, and safety factor.
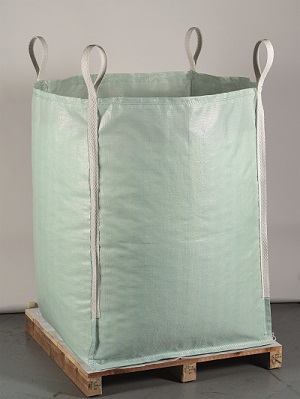
A circular economy for big bags
At the beginning of a closed loop stands the creation of a uniform material stream. After use, big bags are returned to the big bag filler; this guarantees that they are similar in composition and show the lowest possible degree of contamination, as they do not enter the post-consumer stream. At the FIBC manufacturer, the used big bags are shredded, washed, and processed into rPP on the Starlinger recycling line recoSTAR dynamic, thereby yielding secondary raw materials for the production of new big bags. Apart from saving costs for raw materials, the recycling of big bags lowers the carbon footprint of this type of bulk packaging.
“We have developed this concept because we would like to establish a circular economy for polypropylene fabric in which the recycled material is again processed into fabric – no downcycling involved,” emphasizes Hermann Adrigan, Starlinger Sales Director. “This can only succeed if the packaging is already designed with an eye on recyclability (design for recycling), and all process steps are perfectly matched.” To take an example, the “circular packaging” sewing process is performed without the use of polyester multifilament yarns.