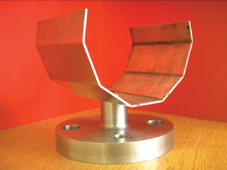
Laser forming shapes metals in a practical way
Source: Release Date:2008-08-19 326
Add to Favorites
Laser forming (LF) has become a viable process for shaping metallic components as a means of rapid prototyping, precision adjustment, aligning, removing distortion and creating 3D complex shapes. The laser forming process is of significant value to industries, such as aerospace, automotive and microelectronics, which previously relied on expensive stamping of dies and presses for prototype evaluations. In contrast with the conventional forming techniques, this method requires no mechanical contact and thus promotes the idea of 揤irtual Tooling? It offers many advantages in the process flexibility associated with other laser manufacturing techniques like laser cutting and marking. Laser forming can produce metallic, predetermined shapes with minimal distortion. The process is similar to torch flame bending used on large sheet material in the ship building industry but can achieve a more controlled final product.
Laser forming appeared at the end of twenty century and is still a developing area in the laser engineering world. The main advantage of this non-contact forming method is that there is no 搒pring back?effect. Some laser formed 3D curvatures can not be achieved by conventional mechanical methods. Rapid laser forming can be accomplished using a laser marker system equipped with fast galvo-mirrors. Fast scanning optics can change the LF regime and expand development of forming thin section components. Researches on laser forming since the mid-1980s addresses potential applications of thicker section 2D and 3D laser forming for ship construction and aerospace sectors. 2D laser forming encompasses laser forming operations that utilize two dimensional out-of-plane bends to produce three dimensional results e.g. a fold, while 3D laser forming encompasses laser forming operations that can utilize combinations of multi-axis two dimensional out-of plane bends and in-plane localized shortening to produce three dimensional spatially formed parts e.g. a dome. The application of LF to micro-scale components is currently generating increasing interest, with several groups recently undertaking studies on a varied range of materials and potential uses. Also recently the laser forming of tubes has become more relevant for industrial application. There has been a considerable amount of work carried out on two-dimensional laser forming, using multi-pass straight line scan strategies to produce a reasonably controlled bend angle in a number of materials, including aerospace alloys. A key area, however, where there is a limited understanding, is the variation in bend angle per pass during multi-pass laser forming along a single irradiation track, in particular the decrease in bend angle per pass after many irradiations for a given set of process parameters. Understanding of this is essential if the process is to be fully controlled for a manufacturing environment. Laser forming of thin foil by a newly developed sample holding method A sample holding method is newly developed for laser forming, in which the target material is held between two transparent plates. During laser beam scanning on the target, the target foil is kept flat. After the scanning is finished, the foil is detached from the holder; the foil bends toward the beam scanned surface. Experiments are carried out with a Nd:yttrium-aluminum-garnet laser beam for a spot size of 25祄 and for a traverse speed of 10 mm/s. A bending angle of about 30?is obtained for stainless steel (AISI 304) foil of 10祄 in thickness with a power of 0.3 W and a scanning repetition number of 20. On the other hand, if the laser beam is focused and scanned on the convex side along the ridge line of a curved foil, it bends toward the concave side and the bending angle increases. The increment angle of about 20?for a pre-bent angle of 45?is obtained for stainless steel foil 20祄 in thickness under the conditions of the power of 1.3 W and sLebron Soldiers XI 11
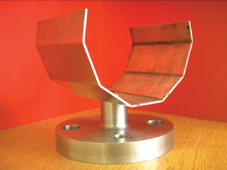
Add to Favorites
You May Like