The global nylon monofilaments market is projected to hit $1.89 billion by 2020, according to a report by Radiant Insights, with growth of key end-use industries such as automotive, fishing and consumer goods. Growing application in the medical industry is also seen. In terms of volume, the global nylon monofilament market demand is expected to reach 476.4 kilo tonnes by 2020 from 337 kilo tonnes in 2013 growing by 5.2% annually from the period 2014 to 2020. Asia Pacific as the leading regional market accounted for more than 64% of the total market volume, and this position is expected to be sustained over the forecast period. Growth of fishing and automotive industries in China, India and Indonesia is expected to drive the regional market.
Monofilament extrusion systems have become more sophisticated, owing to R&D initiatives by leading producers of this product line. One company, PLASCO Engineering Inc. has maintained its pioneer position as a leading supplier of comprehensive range of plastic extrusion lines in Asia, and has also been successfully penetrating the international markets.
“Monofilament is used in our everyday life in various forms, and it is widely preferred in various applications due its flexibility, good shock strength, and cost-effectiveness. Monofilament is commonly used in fishing and agriculture net, ropes, fabrics, filters, textile conveying belts, medical devices, wastewater treatment, stretched tape, and sport strings. In this area, PLASCO has over 30 years of experience manufacturing monofilament extrusion line for the global market, offering customer ideal process system to capture the ever-growing market, enhance profitability, and sharpen customer’s competitive edge,” according to Tony Wang, General Manager.
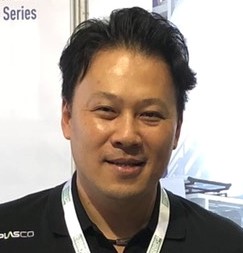
Mr. Tony Wang, General Manager, PLASCO
Strong global market demand has created opportunities for the company’s monofilament line, as well as its strapping band extrusion line, as these now account for almost 80% of PLASCO’s production. “The demand for monofilament and strapping band has increased significantly, and with our extensive experience in the industry and engineering background, PLASCO is able to provide the best solutions to the monofilament line producers and strapping band producers worldwide,” Mr. Wang stressed.
Processing made easy
The monofilament extrusion line from PLASCO offers a complete spectrum of possibilities, with various models available for processing nylon, polyester, and polyolefins (HDPE & PP). From standard monofilament line configuration, to custom-made equipment for heavy gauge monofilament, bi-co (bi-component) monofilament, crimpled monofilament, with different shape profile and diameter range from Ø 0.08mm to Ø 4.0mm for all domestic, fishery, agriculture, packaging, and various industrial application.
Driven by the fishing industry, the global monofilament market growth has increased significantly in both developed and developing nations. At the same time, the rapidly expanding textile industry coupled with rising application of new thermoplastic urethane (TPU) material in sportswear products fuel product demand. “Overall, Asia Pacific is the largest market for monofilament, and owing to upsurge in the fishery industry, and growing usage for textile and sport products, demand in the region will be sustained,” according to Mr. Wang.
With the growing demand of global monofilament production, PLASCO monofilament extrusion line has the advantages of innovative technologies and knowhow to provide customers with reliable and extremely efficient production system to facilitate the ever-expanding requirements of all the sectors, ensuring modest investment while delivering high productivities to meet and exceed expectations of each customer.
Diverse end-products from strapping bands
Strapping bands are widely used in the packaging industry in various application such as food and beverage, consumer goods, newspapers and other merchandise where protection ranks high for strapping that can combine, hold, stabilise and fasten goods.
PLASCO strap extrusion line is capable of producing strap sizes based on all international standards for both PP and PET straps - from the narrow 4mm strap to the customised heavy gauge 25mm strap. The product portfolio ranges from the standard PP strapping line configuration to the technical PET strapping line set up, with possibility for both embossed or non-embossed straps. The line can be customised for both manual and automatic operations. PLASCO strapping band extrusion line has the solution for various capacity requirements, from 700 tonnes/year and up to 3,000 tonnes/year.
The JC-SPP series PP strapping band extrusion line designed for production of PP straps, is commonly used for light to medium load packaging such as newspaper & magazine, carton boxes, pallets, and other industrial and consumer usage.
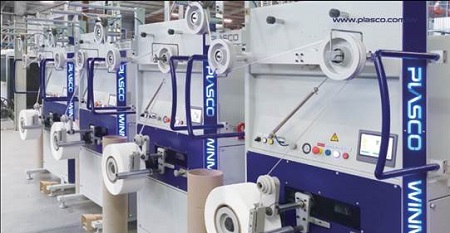
PP strapping band extrusion line from PLASCO
The JC-SPET series PET strapping band extrusion line is designed with advanced technology that makes it possible to process 100% rPET bottle flakes in a single production step, convert polymer to a value-added PET straps commonly used for medium to heavy load packing such as bricks, ceramic tile, cotton bale, lumber, and other industrial uses. “PLASCO strapping line offers a combination of efficient, reliability, and performance, ensuring the least investment compared with its high productivity,” Mr. Wang explained.
Moving ahead in Asia
PLASCO is in the best position to respond to the rising demand for energy-efficient machines. Machine modularly constructed with robustly engineering design, integrated with latest proven technologies to maximise power saving guarantees low energy consumption, low maintenance cost for reduced production costs.
The past few years saw PLASCO’s customers in Asia rising and this the company attributed to the dynamic industrial sector in Asia, in particular the Southeast Asian region. As Mr. Wang explained: “We don’t have a branch office in any of the Southeast Asian countries but we have trading agencies which handle sales and after-sales requests. But since the market in this region is quite stable, we feel it’s necessary for us to come here and visit our customers directly, as well as join trade events to develop new business contacts.”
Black Friday 19