New information technologies, the products of the Industrial Internet of Things (IIoT) revolution (sometimes called Industry 4.0), are not only impacting manufacturing effectiveness but also equipping businesses with the ability to identify smarter ways to work. With IIoT technology, many organisations are beginning to realise that they can easily access tools that allow them to conduct improved analytics and better manage production.
Smart manufacturing environments throughout the supply chain produce information that can be accessed and used to produce actionable insights – all in real time. Huge amounts of raw information can now be used to virtually track capital assets, processes, resources and products, enabling businesses to look at their manufacturing operations internally, streamline business processes and optimise supply and demand. The autonomous networking of machines and systems along with the inclusion of big data analytics, smart sensors and cloud computing applications also help to predict maintenance issues or system failures and react to them accordingly, saving valuable time and money for companies.
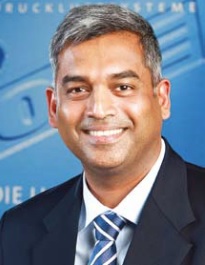
Mr. Nalin Amunugama, General Manager, BOGE KOMPRESSOREN Asia Pacific
“In today’s fast-moving global markets, manufacturers need to respond quickly to changing demands and maximise new market opportunities. By all indications, we are in an era of significant convergence, where information technology, operational technology, and global megatrends will drive changes in the way we do business and interact with customers,” says Mr. Nalin Amunugama, General Manager of BOGE Kompressoren Asia Pacific, a leading supplier of compressed air systems.
Worldwide, manufacturing companies are expected to spend $500 billion a year by 2020 on IIoT technology, and the value generated will reach $15 trillion per year by 2030. The explosive growth in connected devices and platforms, abundance of data, and the rapidly changing technological landscape are making it imperative for companies to adapt their products and manage this sea of information in both practical and cost-effective ways.
Rise of Smart Factories
Central to the operations of the smart environment are cloud-connected machinery and equipment that leverage collected data to monitor processes and keep production running optimally. The application of intelligence – in the form of sensors, motors and robotics – along the assembly lines also frees up manpower from repetitive tasks, and directs them to more urgent or complex roles.
As part of efforts to improve its capabilities, electronics manufacturing firm Infineon Technologies is implementing its own Smart Enterprise Programme (SEP). With a $105-million investment, the company plans to transform its manufacturing plant in Singapore into a Smart Factory over the next five years. Various technologies have since been deployed, including cloud robotics in the form of automated guided vehicles that transport chips across different parts of the facility.
With increased automation, Infineon expects to eliminate errors and accidents that typically occur in manual activities such as the handling of materials in and out of storage, and microscopic visual inspection for defects. Beyond work processes, the job demands of the company’s engineers, technicians and operators are also being revised. New workflows and technologies mean that workers are required to take on skill sets in trouble-shooting and operating man-machine interfaces, ensuring that they continually adapt as the system evolves. In the long run, the SEP, supported by a trained workforce, will give the company a leap in productivity – in this case, chip output of four times – while helping it maintain its competitive edge in manufacturing.
Power of predictive maintenance
Adding compressed air systems within the context of the smart factory promises major efficiency gains, largely because compressed air generation is a significant contributor to operational costs. Equipping compressed air systems with the ability to gather, compile, and analyse system data on a local level not only allows operators to continually track and monitor energy efficiency, but also schedules maintenance works even before an actual problem occurs – this ensures production remains undisrupted and downtime is eliminated.
In manufacturing plants, compressed air is a critical utility and is ubiquitous in the food and beverage sector, where it is used in a host of process applications including product handling, cooling and freezing, labelling, cutting and peeling food, bottle filling and packaging. When contaminated air comes into contact with a food product, it can affect its taste, appearance, colour and shelf life, as well as compromise hygiene standards.
To address these concerns, BOGE introduced a diagnostics tool for increased safety and transparency in compressed air production. Ideally suited to monitor and manage complex systems and plants, the BOGE airstatus enables measured data from any station to be called up, graphically displayed and evaluated. The system monitoring is turned on by simply locating the relevant compressors and components via the Modbus Scan. The system data can be transferred directly via GSM/GPRS or via a LAN connection in real-time and are accessed on the airstatus web portal or the BOGE app. The app gives users an overview of the status of their compressed air systems anywhere anytime, and sends maintenance messages on temperatures and pressures that allow operators to instantly identify and react to faults. The receipt of e-mail or text alerts when values go above or below defined limits further enhances safety.
“Through remote surveillance, users can make decisions that contribute to the optimal functioning of their systems based on the latest data while adhering to regulatory requirements,” Mr Amunugama stresses.
Cross-system integration
From process plants right to the plant floor, integrated systems offer immense potential to improve rigid back-end manufacturing. Manufacturing app engine Tulip recently introduced a self-service technology that allows operators to create customised apps that facilitate shop floor operations. Promising manufacturers a high degree of flexibility in creating their own digital solutions, the modular platform ensures customers’ unique, ever-changing needs are carefully addressed.
“Manufacturing software needs to evolve. Legacy applications neglect the human side of manufacturing and therefore suffer from low adoption. Tulip aims to change all this through our intuitive, people-centric platform,” explains Tulip co-founder, Mr. Rony Kubat.
The system makes it easy for manufacturers to connect work processes with machines and back-end IT systems, and also feeds operators with real-time data on their smart devices. Insights based on advanced analytics enable workers on plant floors to respond to changes quickly, while they perform their production tasks. With integrated access to previously isolated data streams, businesses are better equipped to monitor operations, reduce downtime, increase savings and support process improvement.
The Tulip system has yielded positive results. In its first four weeks of operation at Jabil, a global provider of intelligent supply chain solutions, production rose by more than 10 percent and manual assembly quality issues decreased by a significant 60 percent.
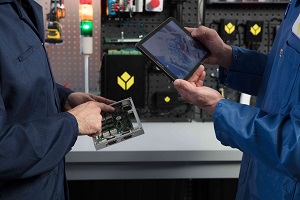
A future with digital ecosystems
Increasing digitisation has opened the door to tremendous business potential for manufacturers, but also puts tremendous pressure on them to disrupt current business models. Entire industries are scrambling to keep pace while emergent technologies continue to provide ways for businesses to shape a new future for themselves. To survive, this requires embedding the ability to track, understand, evaluate and harness emerging technologies and innovation that are taking place within and across those platforms as part of a company’s continual strategic process. Manufacturing ecosystems, and the processes that span them, will be among the biggest beneficiaries of IIoT solutions.
As technological innovations continue to drive significant responses to ever-changing market dynamics, businesses that embrace IIoT will not only be able to collect valuable data, but gain actionable insights that can result in preventive maintenance, huge quality improvements and positive sales forecasts.
The Industry 4.0 revolution is here to stay and will gradually become the default for business and industrial operations. It will continue to push the boundaries of connectedness and efficiency by empowering engineers, operators and whole businesses to build more coordinated data ecosystems and create more transparent and efficient supply chains