Without doubt, the plastics industry today is faced with many challenges - sustainability, recycling, circular economy. These challenges were the focus of many industry players who strive hard to come up with breakthrough solutions for recycling plastic waste and reducing the production costs for film manufacturers.
Film production has reached a turning point wherein innovative concepts are being adopted to develop technologies that meet the sustainability goals. Beyond the circular economy targets, the latest generation of film production technologies are breaking barriers by providing excellent mechanical properties and aesthetic qualities to plastic films. At K 2019, the floor was abuzz with live demonstrations of film production lines that take into serious consideration the global plastics industry’s quest for a circular economy.
Brückner Maschinenbau has embarked to make films with the highest possible recycling capabilities producible on film stretching lines. New line concepts for the production of biaxially oriented polyethylene (BOPE) films guarantees production efficiency while meeting the sustainability challenge. In another demonstration, Reifenhäuser presented definitive and innovative solutions through its new portfolio geared to reduce material consumption through resource-preserving processes. The machines that the company recently introduced are aimed at recycling plastic waste for a waste-free production.
Focus on raw material and energy saving
Brückner Maschinenbau is keeping to its own ambitious objectives for a decreasing raw material usage and an increasingly minimal energy consumption during film production. All legitimate demands about recycling and reusability, the challenge of climate change and the reduction of the carbon footprint throughout the entire packaging production chain have been taken into consideration in the various solutions offered.
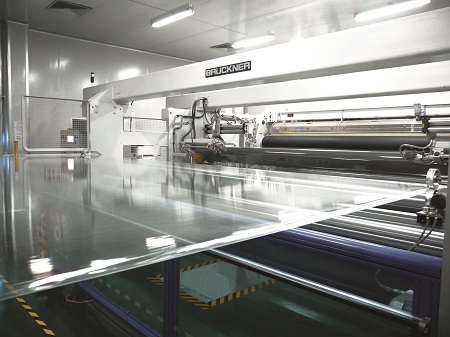
High-performance stretching lines from Brückner Maschinenbau
Brückner has been working on a means to make films with the highest possible recycling capabilities producible on film stretching lines. The focus is on mono-material film with superior mechanical and optical properties, which will be able to substitute previous multi-layer films made from different materials. These are ideal for the use in new, single-origin packaging and guarantee good sortibility in waste separation and optimal recycling.
At K 2019, Brückner debuted two completely new line concepts for the production of BOPE films. Film producers can chose between a working width of 6.6 m and an output of 3 t/h, or a working width of 8.7 m and an output of 5 t/h. These are 5-layer concepts for an extended range of films. The new lines also have the flexibility to produce BOPP films with specialities such as UHB films and coated films for high-barrier uses alongside conventional packaging film. As the demand for innovative BOPE films is only now starting to develop, film producers will be able to react swiftly and flexibly to market trends.
Alongside stretching lines for the production of packaging films, machines for speciality films are becoming more important in Brückner’s portfolio. The company has unveiled various innovations in film production such as the new high-temperature concept for BOPP capacitor film – which is interesting, for example, for the use in electrical components installed near motors. It also developed production systems for the production of stone paper based on BOPP or BOPE with a calcium carbonate proportion of over 60%: not only with good printability and waterproof, but also environmentally friendly in production. The company’s biaxially oriented polyester films (BOPET) for optical applications is made possible with. Brückner’s new, patent pending Relax System that ensures homogenous film properties and thus high film quality and better processability. The company has also gained another achievement with its line concepts for biaxially oriented polyimide (BOPI) which is perfect for flexible optical applications, e.g. flexible displays. The stretching ovens and systems need to be suitable for very high temperatures of up to 400°C, is in Brückner’s new line concepts. In the field of battery separator film for lithium-ion batteries, Brückner has also made a good name for itself in the market with leading film manufacturers.
As recycling stands at the forefront of a circular economy, new mono-material structures must fulfil the highest demands and must not be inferior to previous packaging films. In this aspect, Brückner has developed a new inline coater for all BOPP and BOPE lines, installed in the line before the transversal stretching, it makes the production of extremely thin functional layers within the nano-range possible. Due to the extreme thinness, the layers don’t disrupt the sorting and recycling, but cater, for example, for an improved adherence during metallising and excellent barriers in combination with the equally thin but effective aluminium oxide coating.
Ready-to-use sustainable solutions
Reifenhäuser is also focusing on sustainability and revealed at K 2019 its strategic approach ‘Reduce, Reuse, Recycle, Replace’ which was reflected in the 15 application examples from its all business units. Its R-Cycle concept for a closed-loop cycle provides for marking in film material so that it remains traceable throughout its entire life cycle – one of the preconditions for recycling.
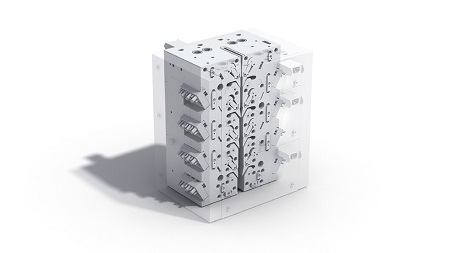
Reicofeed Pro with layer thickness optimisation from Reifenhäuser
Reifenhäuser also released its Reicofeed Pro with layer thickness optimisation. Replacing multilayer film by monomaterials with no loss of quality saves costs. With the Recofeed Pro coextrusion system from Reifenhäuser, lines adjust the functional layers of multilayer film to the exact thickness required without any loss of barrier properties. Not only does this lower raw material costs significantly, it also ensures full reusability.
The feedblock can adjust and optimise up to 11 layers with no line stops needed to change product. Optimisation occurs in ongoing production to ensure high process accuracy. The system corrects each single layer inline if a profile deviates. With the Digital Layer Control System upgrade, the process is even fully automated – to minimise reset times and maximise service life – with no loss of quality. Saving recipes and process settings guarantees constant high film quality, despite frequent product changes. The advantages are obvious: as material costs make up 80% of total costs, Reifenhäuser solution can achieve annual savings in the mid 6-digit range. By contrast, when monomaterials are used, this percentage drops below the 5% mark, thus going beyond the legal requirements for recycling.
The Reifenhäuser Technology Centre was also completed to serve as a fully modernised, largest research and development centre for plastics extrusion technology. Inhouse and customer applications are further developed under real production conditions using the latest plastics extrusion technology and extensive know-how. The centre houses seven high-tech lines at the latest state of the art for the development of blown film, cast film, polishing sheet, and nonwoven products. One of the highlights is the digital connection between the lines and the Reifenhäuser Digital Business Platform. At the centre, visitors and customers can experience production in operation, conduct trials, and develop line layouts and recipes in tune with their requirements in consultation with the Extrusioneers from Reifenhäuser.
The Technology Centre houses several machines, one of them is a world first - Reifenhäuser laser measuring system that detects film topography to ensure extremely flat film. The system measures film flatness in a closed loop automatically and continuously optimises production parameters. This guarantees both high energy efficiency and high process reliability. It achieves a visually excellent end product while significantly reducing the use of glue, raw materials, and ink. Customers who use EVO Ultra Flat in their production are certified by Reifenhäuser and receive a quality seal. EVO Ultra Flat improves the flatness of laminating and barrier films by up to 40% and reduces sagging by up to 90%.
Air Jordan XI 11 Wool