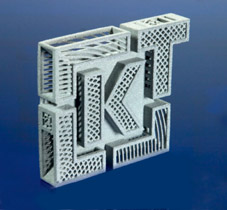
Contrary to classical plastic processing methods, the choice of materials for selective laser sintering (SLS) - and thereby also the range of possible application areas - is limited. Recent work has shown that plastics, which previously were unsuitable for SLS, can now be processed into powders for the fabrication of complex components. First trials with POM resulted in parts with appealing surfaces and good mechanical properties. Additive processes such as selective laser sintering (SLS) permit layered buildup of three-dimensional components directly from CAD data. Contrary to conventional forming methods like injection molding, this toolless approach offers practically unlimited geometric freedom. Thanks to new developments, this technique has outgrown the established application area of prototyping and is now suitable for manufacturing small series of functional parts. Although many different processes are available, their breakthrough into production applications has been prevented by material-related restrictions. As soon as specific demands are placed on components and their properties processors are frequently forced to compromises. However, for the manufacture of mechanically stressable prototypes in particular, selective laser sintering has become accepted.
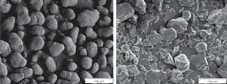
A prerequisite for SLS processing is that the material is available in the form of a fine powder. So far, partially crystalline PA12 was mainly used for mechanically highly stressed plastic components. Although other thermoplastic materials such as polystyrene (PS) or polycarbonate (PC) are available as powders, the results are highly porous components with poor mechanical properties. Such materials are typically used for manufacturing lost cores in precision casting. In addition, thermoplastic elastomers (TPE) are used in a limited number of applications. Research work at the Institute of Polymer Technology (Lehrstuhl f焤 Kunststofftechnik, LKT) at the University of Erlangen-Nuremberg is focused on eliminating these material-related restrictions. As a number of requirements are placed on the material by the manufacturing process, material characterizations derived from knowledge of the interactive mechanisms are decisive for successful processing of new polymers.
Demands placed on plastic powders plus thermal constraints The properties of laser-sintered components, e. g. density, surface structure are determined by the interaction of the process parameters with the material. Investigations have shown that particle geometry affects the component?s surface roughness. Similarly, melt behavior and pourability of powders as well as their application determine the component?s density. Size distribution and the geometry of PA12 particles have a great influence on the porosity of the sintered components, as these depend greatly on the packing density in the powder bed. As a result, higher bed packing density leads to improved strength, density, and dimensional accuracy of the sintered components. Commercially available, free-flowing laser sintering powders consist of spherical particles with a close size distribution of about 60mm (Fig. 1). The utilized plastics must be specially stabilized against thermal decomposition, as they must be maintained close to the crystallization temperature for several hours. At the end of the manufacturing phase, the unmelted but thermally aged powder is separated from the component. Ideally, the powder should not be agglomerated after the buildup process, so that during removal it separates from the component simply through gravity. Apart from the application of material, the properties of the finished components depend on precise temperature control during the buildup process. The temperatures are different from partially crystalline and amorphous thermoplasti
Air Jordan X 10 Shoes