In designing injection moulding systems, precision, shorter delivery times, reliable operations and flexibility are certain requirements that must be met. Several injection moulding systems took centre stage at the recently-concluded CHINAPLAS 2019 which further put emphasis on the complex demands posed by today’s plastics manufacturers.
German quality meets Chinese agility, and at CHINAPLAS 2019, KraussMaffei presented a locally produced all-electric injection moulding machine for the first time. Starting immediately, the new all-electric PX Agile is being manufactured at the new Sanming location in accordance with the globally applicable quality standards of KraussMaffei. Customers in China can take advantage of short delivery times and excellent service.
"The new PX Agile is perfectly tailored to the needs of our customers in China. Both up-and-coming small and medium-size companies and established large companies increasingly request short response and delivery times in order to adapt to the rapidly changing conditions of the market. Furthermore, low investment costs and easy operability of the machines are in demand," explains Dr. Hans Ulrich Golz, President of the Injection Moulding Machinery segment of KraussMaffei Group.
The new PX Agile is produced at the KraussMaffei plant in Sanming, in Fujian province in the south-east of China. A special stock machine programme makes the delivery of standard machines ex works possible. Machines with additionally ordered options will be available for delivery within four to six weeks. Due to the local production of the PX Agile, the service response times will be very short. The machines will exhibit preparations for all options which leads to an easy and fast retrofitting and upgrading. Furthermore, the spare parts availability and respond time will meet the requirements of Chinese customers.
"The new PX Agile offers precisely the advantages that dynamic companies in China request: large platens and high performance, which permit varied, flexible application of the machines in production," says Dr. Golz. Furthermore, options for retrofits or upgrades are available for the PX Agile, allowing for a quick and flexible response to changing market conditions.
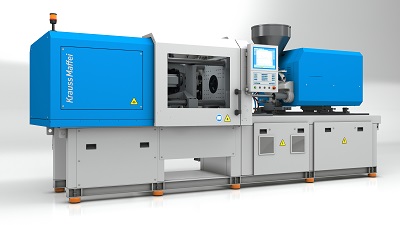
The new all-electric PX Agile from KraussMaffei
User-friendly human-machine interface
Customers in China additionally benefit from a user-friendly human-machine interface specially tailored to the requirements of Chinese markets. Easy operation and intuitive programming ensure that the machines are accepted quickly. The flexible sales options are also particularly attractive. They include a free trial phase and short-term and long-term leasing plans with flexible payment plans.
The new PX Agile features a German DNA that meets the highest quality standards and is based on decades of experience gathered at KraussMaffei's Munich headquarters. For example, this includes the expertise in the design of the plasticising unit, which corresponds to the established PX series from Germany. In addition, production of the PX Agile in Sanming observes the global quality standards of KraussMaffei, supported by cutting-edge programs in control and validation systems.
The new PX Agile is ideal for standard applications, for example for technical components, electric and electronic devices and for the automotive, packaging and medical industry. At CHINAPLAS 2019, KraussMaffei launched the PX Agile 80 and PX Agile 160 on the market with a respective clamping force of 800 or 1600 kN. Both machines demonstrated the advantages of the new PX Agile series: stability, precision, short cycle times and maximum flexibility for various applications.
Striking surface effects take shape on the new PX Agile 80 with its inductive dynamic mould heating (DMH) technology by the partner Roctool (HD Plastics). The decisive benefit is that the technical and financial effort of an additional film decoration or (secondary) painting becomes obsolete. At the example of a TV box finisher from the entertainment industry, KraussMaffei demonstrated to the market the wide and varied design options of the inductive mould heating technology. Different colour shading, hologram, gloss or matt effects—everything can be realised with the one-shot process without the need for additional post-mould processing.
Precision, fast cycle times and high component quality are the features of the new PX Agile 160, which was demonstrated producing a typical medical application—pipette tips taking shape in a 32-cavity mould.
Both machines, the PX Agile 80 and PX Agile 160, are equipped with the new LRX Agile from KraussMaffei. The new linear robot series is also produced at the KraussMaffei plant in Sanming offering short delivery times and an attractive price and performance ratio for customers in China. The new LRX Agile represents an efficient solution for simple pick-and-place applications and is suitable for all injection moulding machines. Three different programming levels ensure an easy and quick start even for beginners.
Compact two-platen solution
Another interesting market launch at the exhibition was the new generation of Haitian Jupiter III Series which is a compact two-platen solution with even more free space and open integration platform for intelligent control and digitisation of processes
The latest Jupiter III Series is now available worldwide. Benefited from Haitian’s extensive experience in development of two platen solutions in past two decades, the first Generation 3 Series from Haitian Plastics Machinery features an open system and control platform for digital process connections, in addition to design innovations and improvements.
As a product with “Technology to the Point”, the further development of the JU Series focused on flexibility, simplification and ease of control in the application.
The footprint of the already space-saving two-platen machine has been further reduced, while the opening stroke and dimensions of the mould cavity have been increased. Important for large-format products such as refuse containers, logistics pallets, white goods or long visible parts in the automotive sector. Tool changes are now also easier and maintenance work can be carried out more quickly.
Advances in production technology due to design innovations have led to more stable platen movements and shorter dry cycle times.
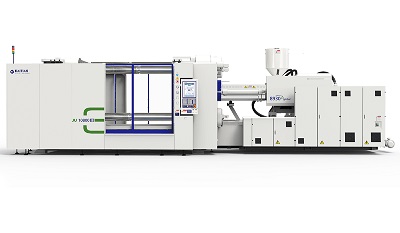
Haitian Jupiter III Series is a compact, two-platen solution
An important component of the 3rd Technology Generation is the digitisation of processes and thus the gateway to open integration for all future environments. With "Motion Plus", Haitian International has brought together existing and new technologies to ensure smooth human-machine interaction and support customer digitisation of production processes. An important component of the new platform is a sensor-supported control system that optimises the most important production processes and supports communication with all common interfaces.
The clamping unit has a compact design that allows for more space for large moulds, more free space in production and extended stroke for mould movement and ejector as option. Four independent short-stroke locking cylinders undertake precise mold height adjustment, balanced force of every tie bar, and the mould remains closed during parallel movement. The new parallel locking system enables fast, precise response and quiet operation with close movements for more precise and faster operation and shorter cycle times.
The injection unit features linear guides for the main linear movements that guarantees lower friction and lower energy consumption at higher precision. It also enables free choice between multiple injection functions for greater injection performance and extended application range of the process; while the swiveling injection unit allows for faster screw and barrel change, and overall easier maintenance.
The drive system is a new, highly dynamic drive unit providing for higher torque, greater efficiency, while occupying less space. The GreenVantage is an energy-saving, fine-stage drive unit with lower energy consumption and reduced noise level.
adidas