The AGRU group is one of the world’s most important single-source suppliers for high-quality products made from engineered plastics. With the $40 million investment into a new production facility for large diameter pipes in Charleston, South Carolina, the Group is expanding its presence in the United States and setting a milestone unseen before in the industry with the start-up of the AGRU XXL pipe production facility that allows the extrusion of the world’s largest high-density polyethylene pressure pipe.
Half a century of experience in plastics processing is what it takes to manufacture the world’s largest high-density polyethylene (HDPE) pressure pipe. AGRU had to overcome major technical challenges to achieve perfect roundness, homogeneous wall thickness, and completely smooth surfaces at the largest scales. Today, The Plastics Experts have the capability to extrude HDPE solid-walled pipe strings in continuous lengths between 5 m (16 feet) and 610 m (2,000 feet), with outside diameter ranges between 630 mm (24 inches) and 3,500 mm (138 inches). These XXL pipe strings are designed to be installed near- or offshore, but can also be utilized for onshore installations of process pipes or transition pipelines.
A pioneering production facility
AGRU’s XXL pipe production facility is pushing the boundaries in plastic pipe production. Inside this path-breaking facility, the world’s largest solid-walled HDPE pressure piping systems are manufactured on-demand. And with a maximum outside diameter of 3,500 mm, AGRU is establishing new industrial standards. The state-of-the-art production facility is in full compliance with the strictest quality criteria according to ISO 9000 and ISO 14001 standards. As a result, AGRU XXL pipes and fittings meet and exceed both EN 12201 and ISO 4427 requirements. AGRU uses only high-grade PE 100 or PE 100-RC resins for the production of its XXL pipes and fittings.
The facility is located directly on the shore, providing the perfect conditions for the production, storage, and towing of XXL pipe strings. The extrusion into the Cooper River estuary and the marine storage in front of the building are unique in North America. Furthermore, the facility’s close vicinity to the Charleston harbor makes it easy to tow the XXL pipe strings worldwide. AGRU purchased this former industrial site and cleared the pollution damage caused by a century of coal processing. The futuristic plant was designed to withstand hurricane wind speeds up to 150 miles per hour. The new production site causes minimal environmental impact and operates on a 24/7 basis.
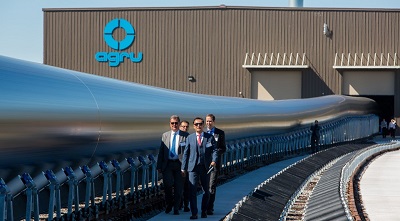
XXL diameter HDPE pipes for marine installation
HDPE piping systems are the best choice for many applications on- and offshore. They are nontoxic and are approved for potable water transport. Thanks to their high fatigue strength, AGRU’s XXL pipe strings that are installed offshore can be lowered to the seabed in a fast and safe manner. Since HDPE is also noncorrosive and there are no welding beads inside the continuously extruded pipeline, it is ready for long-term operation with a low-head loss, saving energy. Together with its high abrasion resistance and resilience to shocks, polyethylene is a much better solution than steel, GRP, or concrete piping for many applications. AGRU is able to extrude XXL pipe strings in SDR ratios between 11 and 33.
Because HDPE pipes are in the “featherweight” class compared to steel or concrete pipes, and with a density of only 0.95 kg / dm³, it is able to float in the water without assistance. This feature enables a unique form of delivery. Towing on-demand manufactured pipe strings over the ocean in the required dimensions to marine job sites is the most effective and cost-saving form of transportation. For this reason, the brand new AGRU production facility is located at the delta estuary of the Cooper River in Charleston, SC. Pipes can also be stored on the waterway right in front of the new plant, expediting the tugging process. When a pipe is sealed on both ends, the air captured inside provides additional buoyancy for easy towing operations.
Customers will enjoy many benefits of the new production site, but the most significant is its logistical contribution to near- and offshore projects resulting in shortened installation time and a range of cost savings. AGRU XXL pipe strings don’t require welding work at the job site and can be quickly joined with flange connections. Such a ready-to-use pipe string of up to 610 m long in conjunction with factory-assembled flange connections represents significant cost and welding work reductions compared with the effort necessary to join 10 m long pipe sections with butt welding.
Nike Special Forces Air Force 1 Boots