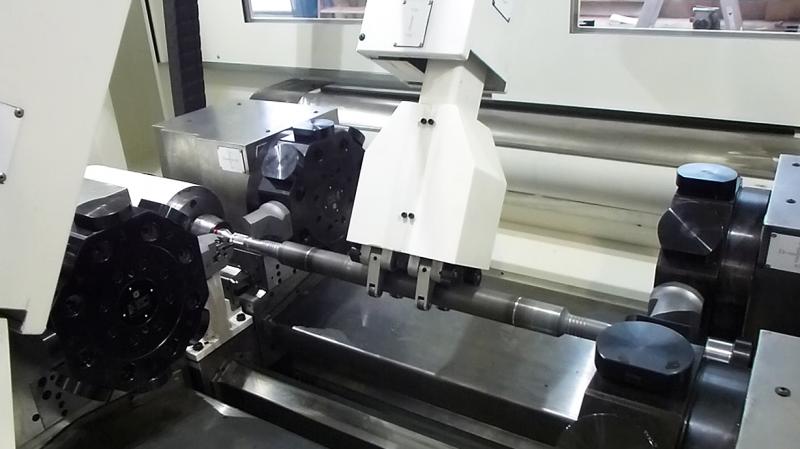
Werkzeugmaschinenbau Ziegenhain GmbH is the DVS TECHNOLOGY GROUP’s specialist for turning and combination machining of shaft-type components. Its new machine WMZ H200 offers an extremely time efficient complete solution for the serial production of vehicle shafts. Compared to other technologies currently in use, the WMZ H200 halves machining times and decreases process times by up to 35%. Therefore national and international OEMs count on the WMZ H200’s machining capabilities.
The H200 is based on a flat-bed design with a total of three slideways which are arranged next to one another. The workpiece spindle is firmly mounted to the centre slideway, and the tailstock is mounted in such a way that it can be moved or alternatively fixed to a moveable sleeve.
Shortened tool changeover time
There are two compound slides for fitting rotating revolvers on the slideways to the left and right of the workpiece. The four compound slides can be moved independently of one another, allowing shafts with a diameter of up to 100 and a length of as much as 1100mm to be machined with four lathe tools at once. Alternatively, the tool changeover times can be reduced by the revolver currently not in action by swiveling and positioning the next workpiece while the previous workpiece is being machined.
Reduced machining time
Wether soft or hard turning or while simultaneously creating recesses, the simultaneous machining with four lathe tools at once substantially reduces the machining time, often more than halving it compared with other technologies currently in use. As well as reducing the main times, the H200 also shortens the secondary times for loading and unloading thanks to its optimized 2-arm automation mounted at the top in the machining chamber. During machining, the loading arm is positioned above the blank gripping position and the unloading arm above the finished part, which is still being machined. Directly after the workpiece spindle has stopped, both workpiece grippers close and the sleeve and clamping device release the workpiece. Brief pivoting through 45° brings the next blank into the machining position and the finished part is transported to the set-down position. After the workpiece has been clamped briefly, the blank gripper opens again and the four revolvers start their turning work.
Minimized traverse distances
The use of one loading and one unloading arm divides the movement paths among two units, allowing the loading and unloading time to be reduced down to 5 seconds chip-to-chip time. As an alternative to the through-loading automation principle described above, the workpieces can be transported to the loading and unloading area at the side by means of a pallet belt and be loaded and unloaded from there using the two-arm automation, preventing the workpieces from touching each other. The combination of simultaneous machining with up to four turning tools and the integrated loading and unloading components is proven to be successful. Thanks to the WMZ H200’s shortened tool changeover time and the reduced machining time as well as the minimized traverse distances it is a first choice machine for the time efficient serial production of vehicle shafts. For a lot of OEMs the short cycle times are the most convincing feature of the WMZ H200.
Nike