As global efforts to promote plastics recycling intensify, the stage has now been set to adopt recycling technologies as a viable solution to this environmental concern. Without urgent action, global waste will increase by 70% on current levels by 2050, according to a World Bank report on solid waste management. Driven by rapid urbanisation and growing populations, global annual waste generation is expected to jump to 3.4 billion tonnes over the next 30 years, up from 2.01 billion tonnes in 2016, the report finds. The report further stated that the East Asia and Pacific region is responsible for generating close to a quarter (23%) of all waste.
Thus, it has become apparent that the recycling equipment and machinery market is majority driven by the growing awareness of industries such as automotive, industrial machinery, building and construction on the benefits of using recycled materials in their final products. The need to urgently curb green house emissions has also resulted in the development of eco-friendly materials which will reduce the carbon foot print globally. In addition to this, stringent laws and regulations imposed by local governments especially in developed regions of Europe and North America will fuel the recycling equipment and machinery demand, according to a report by Global Market Insights, Inc. The report further estimates the recycling equipment and machinery market size to reach $ 1.2 billion by 2025. Asia Pacific is the largest market for recycling equipment and machinery as majority of plastic recycled is imported and processed in China. Other important markets for recycling equipment and machinery are South Korea, Malaysia, Singapore, Thailand, Australia. Asia Pacific recycling equipment and machinery market will grow at around 6% and will surpass $450 million by 2025.
Recent developments point towards eco-friendly and economical recycling where machines are on the route to being able to process and re-process even multi-material waste.
Reprocessing of mixed waste
Every year, tonnes of old textiles that cannot be reused or sold end up in incineration plants or even go to landfill. The textile industry is growing, and the proportion of multi-material textiles, i.e., mixtures of various natural and artificial fibres, is steadily increasing. Society and lawmakers rightly demand rapid technological solutions for the recycling of this kind of waste in order to protect the environment and save material resources. Besides closing the loop from raw material to raw material, the project aims at efficient recycling that yields an end product with virgin-like characteristics.
Starlinger has launched a recycling technology for the separation and reprocessing of mixed textile waste. Within the textile network PlasTexTron©, Starlinger recycling technology is searching for an ecologically and economically sound solution for the recycling of mixed textile waste of multi-material composition.
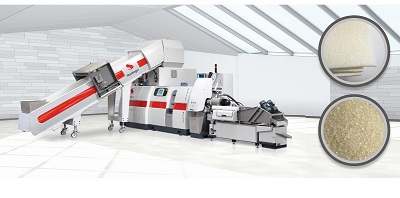
PlasTexTron© from Starlinger
Three universities and eight Austrian companies are involved in the COIN-project TEX2MAT, which is led by the Plastics Cluster of ecoplus, the business agency of Lower Austria, and funded by the Austrian Federal Ministry for Digital and Economic Affairs (BMDW). The project TEX2MAT addresses the recycling of different kinds of old textiles that consist of a mixture of polyester and cotton.
Starlinger recycling technology - a business unit of Starlinger which manufactures recycling lines and has already developed solutions for closed loop production in the field of polyester textiles - provides recycling services and expertise for the project. To achieve an optimal result, regular controls of the material properties are performed by the University of Leoben. The project partners are working on specific case studies. One study focuses on the mixtures of polyester and cotton from the production of towels as well as old textiles in the form of bed linens and working clothes are shredded by Starlinger recycling technology and then undergo enzymatic treatment. The goal is to develop a sample process for closed loop production. Another case study involves technical nonwovens made of polyamides which are shredded and turned into regranulate by Starlinger recycling technology. Substances such as glass fibres, additives and/or colours are added as needed (a process commonly known as compounding) and the customised material is used in the production of highly technical plastic parts such as components for fire extinguishers.
The project TEX2MAT started in November 2017 and will be running over the course of two years. The project partners meet in regular intervals to align the individual steps and discuss the overall progress. In September 2018, TEX2MAT will be presented at the international fibre congress GFC in Dornbirn; initial results are expected to become available until K show 2019 in Düsseldorf.
Recycling of clean edge trim
INTAREMA® K recycling system posted high sales before the end of 2017/2018 with over 40 of this processing systems already sold by the end of March 2018. EREMA Group’s Business Development Manager Andreas Dirnberger pointed out that customers are concentrating more on the recycling of clean edge trim as a result of the increasing demand for high-quality film products and the associated expansion of production capacities.
INTAREMA® K's road to success comes from its profitability. The material alone accounts for around 80% of the manufacturing costs of flexible packaging. If one considers the usual edge trim figure of around 10 per% in blown film manufacturing, recycling is a must-have in terms of cost efficiency. The edge trim which accumulates in production can be transferred directly from the blown film plant – without pre-shredding – to make high-quality recyclates. And 100% of these recyclates can then be put back into the production process.
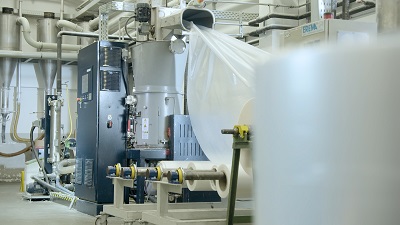
INTAREMA® K from EREMA is ideal for the recycling of clean edge trim
This is also substantiated by Manfred Goellner, Head of Process Engineering at Hosokawa Alpine, a leading producer of blown film plants. The INTAREMA® K is available to OEM customers such as Hosokawa Alpine as part of standardised system packages but there is also high demand for it among end customers.
The INTAREMA® K is ideal for the processing of a wide variety of clean plastic waste. PE mono or multilayer films, PE films with PP, PA, EVOH or EVA or also breathable films such as PE with calcium carbonate can be processed. A low mass temperature ensures very gentle processing of the polymer. Thanks to the interplay with integrated control the INTAREMA® K's preconditioning unit enables automatic adjustment to varying input quantities. In the event of brief material shortages the system switches to standby in the interest of maximum energy efficiency.
Zoom Kobe XII ZK12