Quick mold clamping system for improved productivity
The presentation by HVR Magnetics Co., Ltd. in a seminar hosted by Ringier Trade Media Ltd in cooperation with InterPlas Thailand organizer, Reed Tradex, highlighted the importance of innovative quick mold clamping system to enhance the productivity of a plastics manufacturing operation. Ms. Vivian Qu, Overseas Sales Manager of HVR Magnetics explained that the company’s quick clamping mold system is very fast that it takes only 3 minutes with only one operator to finish the mold change.
As an overview of HVR Magnetics’ operations, Ms. Qu traced the history of the company, from 2010 when the company was first established. The founders of HVR Magnetics have long been engaged in the magnetic industry that by 2011, the company embarked in developing magnetic quick mold clamping system technology, an innovation to what today has made the HVR Magnetics a leading supplier of this innovative system. The company has obtained patents and certifications as a reflection of its product quality and operational excellence, according to Ms. Qu. She further mentioned that HVR Magnetics has cooperated with many big players in the industry, such as with Sumitomo Group in 2013, FOXCONN and KOBELCO in 2014, Hitachi and Fujitsu in 2015, and with over 30 agents worldwide since 2016.
Ms. Qu also enumerated the many products supplied by HVR Magnetics including Electro Permanent Magnetic Quick Mold Clamping System, Electro Permanent Magnetic Chuck, Electro Permanent Magnetic Fixtures, and Electro Permanent Lifting Magnet. These products are utilized in various industries, among them automotive steel manufacturing, pipeline, machinery, electronic equipment and hardware. In discussing the HVR Magnetics Quick Clamping Mold System, Ms. Qu explained how the clamping system can be used on plastic injection molding machine as it is composed of movable side magnetic plate and fixed side magnetic plate, control cabinet, operation box and other components. The system is applicable for 50-4000 tons injection molding machine. In general, the advantages of the system include: cost savings, time and energy consumption savings, cut down labor requirement, no mold drop off and enhanced safety, and improved end-product quality.
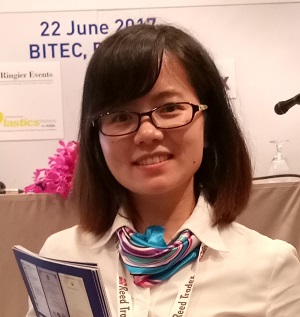
HVR Magnetics Co.,Ltd
Tel: +86-731-28679879
Fax: +86-731-28679979
E-mail: info@hvr-magnet.com
Website: www.hvr-magnet.com
Intelligent molding technology
Shine Well Machinery Co., Ltd of Taiwan was represented by its General Manager, Joseph Lung at the seminar on “Breakthrough Technologies and Materials for Sustainable Plastics Processing.” As an introduction, Mr. Lung talked about how the concept of Industry 4.0 is being practiced in different manufacturing fields. “For injection molding technology, this concept starts on intelligent production. Intelligent production should be Easy and Smart to end users. It consists of not only highly integrated facilities, which can be achieved via automation, but also on how each aspect of production can perform with high efficiency and at low cost. Being eco-friendly is a key issue in making production smart and easy,” Mr. Lung explained.
Shine Well presented its research results on Industry 4.0 specifically on injection molding machinery. In the presentation, three subjects were covered: i-Clamp force control on clamping unit; Induction heater technology on injection unit; and Auxiliary setup integration with injection molding machine (IMM).
Mr. Lung provided an overview of the IMMs that Shine Well offers. These include the horizontal injection molding machines (HIMMs) under the CX series that is a high-speed toggle type with energy-saving features; the MBE series which is a multiple cylinders (two-platens) type that is also energy saving; and the Servo E series Toggle type energy-saving model. The IMMs are ideal for the processing of PET, PVC or thermosetting (i.e. phenolic, urea, BMC, etc.) and ideal for the production of IML, disposable goods, preforms, optics, auto parts, thin-wall, color-mix, etc.
Shine Well has also innovated via the i-Clamp force control which enables equal quality of molding parts, complete air breathing of mold, less possibility of damage on parting surface due to proper clamping force, less friction caused on machine moving parts (e.g. toggle joints), longer life of toggle components, and avoiding tie bar break due to uneven clamping force distribution. The i-Clamp force control program can set proper clamping force with tolerance range for single mold production; while during production cycle, controller can collect data of REAL clamping force measuring through sensors and auto adjust mold height in case clamping force is out of pre-setting. Other important topics covered by Mr. Lung are the impact of efficient induction heater to the injection molding set up and the integration of auxiliary equipment in the system to speed up the process toward intelligent injection molding.
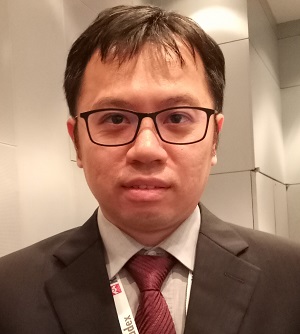
Shine Well Machinery Co., Ltd
Tel: +886-6-3563470
Fax: +886-6-3560082
E-mail: info@shinwell.com.tw
Website: www.shinwell.com.tw/en/index.html
Jon Wai stressed importance of speed in 2 major industries
At InterPlas Thailand, Jon Wai Machinery Works Sales Manager Harrison Chen delivered a highly informative presentation with tips on how to be successful in the automotive and packaging industries by utilizing the latest technologies available today. Found in 1971, Jon Wai Machinery Works already has over 40 years of experience in the plastics industry with its presence in various parts of the world, including two factories located in Taiwan and China, and several branch offices in Brazil and India.
Jon Wai, according to Mr. Chen, provides solutions for packaging, thin-wall container, in-mold labelling, preform/cap and its machines can range up to 3500 tons for bumper. The company’s machines are ideal for multi-resin injection molding.
The ultra-fast thin wall series features injection speed of 550/800 mm / sec, cycle time of 2.35 sec for 2+2 stack mold and electrical charging motor. The multi-resin TCW series is a rotation table-type model with two-color/two-material injection or sandwich injection molding suitable for automotive, electronics, and housewares. The multi-resin TCS model is a joint nozzle (complala) type with V-shape design for two-color/3-color and suitable for the production of furniture.
Another specialty of Jon Wai is the two-stage PET series, which according to Mr. Chen, has the lowest A/A (Acetaldehyde) level (< 8ppm) in Taiwan and features two plungers for short cycle time for pre-plasticizing and injection. It also has a cooling robot that is adaptable. The Toggle/Two-Platen Series is from 600 to 3500 tons and is known for long-term reliability that it has now taken over 70% of Taiwan big machine market, according to Mr. Chen.
In discussing the ‘World of 0.1’ Mr. Chen focused on the cycle time where Jon Wai has achieved vast improvement. He stressed that cycle time is a system and Jon Wai is now able to substantially reduce cycle time with its machines whether these be hydraulic circuit with servo motor power saving system, or hybrid model with electrical charging motor, and fully electric machines. He cited cases where the machines are used in the production of various containers or packaging products and automotive parts.
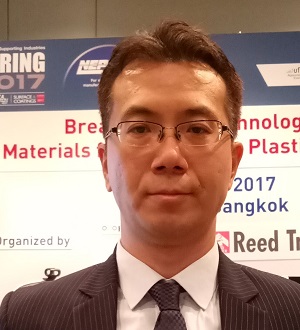
Jon Wai Machinery Works Co., Ltd
Tel: +886-2 2595 4867
Fax: +886-2 2593 2358
E-mail: infor.tw@jonwai.com.tw
Website: www.jonwai.com/index.php