The success stories of breakthrough blow moulding technologies are bringing the packaging sector into a higher level as they have been able to deliver the speed and quality required.
The all-electric KBB series from Kautex Maschinenbau has been well-accepted for its ability to offer short cycle times at lower energy costs. Kautex’s KBB40D machine with 2 x 5-fold production in three-layer ReCo execution was demonstrated at a major exhibition producing a 600-ml flat oval bottle for the personal care industry. The machine is linked to a continuous weighing machine for automatic weight adjustment.
BEKUM also made some advances in this area with its efficient blow moulding technology, EBLOW 407 DL, which offers price-performance ratio in the high-speed production of consumer packaging. The machine offers the benefits of a double-shuttle long stroke machine platen, however, with a focus on cost-efficient production of smaller bottles.
Maximising efficiency
Extremely short dry cycle times and low energy costs give the all-electric KBB series an edge in terms of saving resources and maximising efficiency. In addition, quick-change systems enable by far the fastest product change-over in the extrusion blow moulding machines segment. The first all-electric KBB60D was launched years ago and since then, demand for this series has grown considerably worldwide.
Under the show slogan “Setting benchmarks for high production performance”, Kautex Maschinenbau presented at NPE 2018 its KBB40D machine and demonstrated the production of 600-ml flat oval bottles for the personal care industry. The unit has already been ordered by Amcor and running at its plant. In the NPE demonstration, the bottles are produced on the double-station machine with 10 cavities in the three-layer ReCo process, whereby colour is only added in the outer layer of the bottle. The inner layer uses virgin material to minimise the migration of impurities into the filled product. The middle layer uses regrind or PCR, i.e. recycled plastic, to save both costs and resources, in line with the circular economy ideal. Leak testing of the bottles is performed inside the blow moulding machine.
A continuous weighing machine linked to the blow moulding machine was also shown. It allows deviations in product weight to be identified immediately and adjusted automatically in the machine. This step reduces the number of rejects and increases machine efficiency. Another benefit of automatic weight adjustment is saving in the cost of resin used.
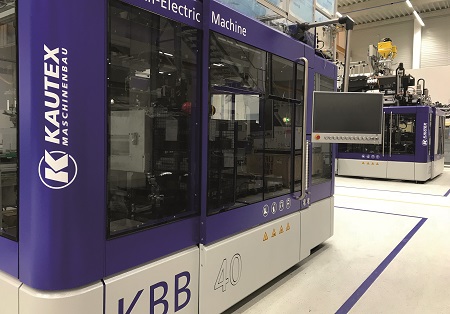
KBB40D from Kautex Maschinenbau offers short cycle times at lower energy costs.
In keeping with the “Industry 4.0” smart factory trend, Kautex unveiled the second generation of its virtual machine. This practical training tool enables the exact simulation of realistic production processes. The system comprising a compact workstation unit, two monitors, a projector and a real control panel allows machines of the KBS, KBB and the KCC series to be depicted in real time. The set up is integrated with Kautex Remote Service, which is based on a built-in firewall that allows a technician to begin detailed troubleshooting without having to travel to the machine location. In the ideal scenario, the fault can be cleared online after the instant analysis. If not, either the faulty part will be identified and a replacement part sent out for self-installation, or a technician call-out will be arranged. This ensures that Kautex machines are up-and-running again as soon as possible, thus minimising the costs of downtime.
When developing the all-electric KBB machines, Kautex Maschinenbau came up with an especially sustainable concept. The latest measurements of energy consumption based on Euromap 46.1 standards prove the concept is successful: Many KBB machines reached the highest energy efficiency classification 10. The industrial Euromap standards developed by the association permit the comparison of machines by different manufacturers on the basis of standardised parameters.
Effective and efficient system
A multi-cavity blow moulding technology was BEKUM’s response to customers expecting answers for the most effective and efficient blow moulding system that specifically focuses on their production conditions and applications. The EBLOW 407 DL blow moulding system from BEKUM offers an excellent price-performance ratio in the high-speed production of consumer packaging.
The North American blow moulding industry recognises that the BEKUM “07” Machine Series offers a full-range of bottle production potential - small bottles through large handled products. To specifically address the growing market need for a high speed, bottle maker, BEKUM has successfully introduced the 407 DL machine. This machine offers the benefits of a double-shuttle long stroke machine platen, however, with a focus on cost-efficient production of smaller bottles, especially those for personal care products.
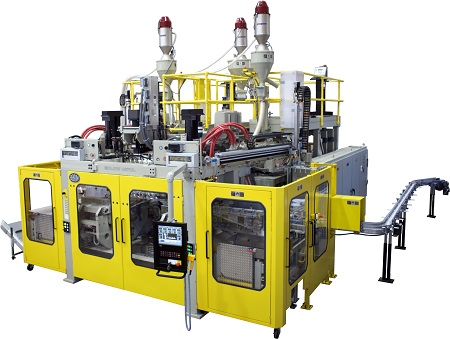
BEKUM introduced the EBLOW407DL multi-cavity model.
With the US-built 407 D and 607 D machine models, the 407 DL includes the patented C-Frame clamp design and is available in Electric (EBLOW) or Hydraulic (HYBLOW) versions as well as hybrid versions tailored to customer-specific needs. At NPE 2018 where BEKUM first revealed this innovative machine, the EBLOW 407DL version was demonstrated running an 8 x 100 mm CLD production of a 1-litre round, 3-layer HDPE personal care bottle in recyclable HDPE. BEKUM’s introduction of the US-manufactured EBLOW 407 DL machine focus on several key benefits. For one, the machine provides for multi-cavity production of a double-shuttle long stroke machine, however with a focus on speed and cost-efficient production of smaller bottles. Flexibility is provided with the newly developed integrated quick mould change system offering less than 15 minutes mould changes per clamping unit without the use of tools. It also makes use of a recently developed 3-layer spiral flow head technology for maximised middle layer HDPE PCR loading and precise circumferential wall distribution. Also, with Electric (EBLOW) or Hydraulic (HYBLOW) versions as well as hybrid versions, BEKUM can tailor the 407 DL machine to address specific customer requirements and operational/maintenance staff expertise.