
Changing parameters on quality and costs have pushed makers of injection moulding machines to take bolder steps. In particular, the growing popularity of all-electric injection moulding machines has opened the doors to several advantages for the processors and all these benefits are summarised in the following premises: lower power consumption from 25% to 60%; lower use of chilled water; less wastage; reduced downtime; reduced maintenance costs; and more environment-friendly. In response to complex demand As growth in demand for all-electric machines is inevitable, a large number of such models are expected to set the trend for more new machines to be launched. Injection Moulding Machinery is the largest of KraussMaffei's business units. The company offers four injection moulding machine ranges, the CX, MX, AX and EX, which cover not only standard applications, but also the whole bandwidth of process variants and special processes. Big machines (the MX series) are one area in which the company excels. Another core competence is solutions for the automotive industry. Other areas where KraussMaffei has intensive expertise are packaging, electrical/electronics and medical technology applications. In recent years, the business unit has expanded its specialised knowledge base in robotic systems and automation.

KraussMaffei launched its AX series of lower-cost, compact all-electric toggle machines for general-purpose use. The line ranges from 65 to 385 tonnes and promises energy savings of up to 60% as compared to hydraulic presses of similar size. The platen moves on roller-bearing guides that deliver up to 80% less friction than a sliding support. The unit also uses KM抯 MC5 touch controller. Its MX series is a range of big injection moulding machines between 800 and 4,000 tonnes.
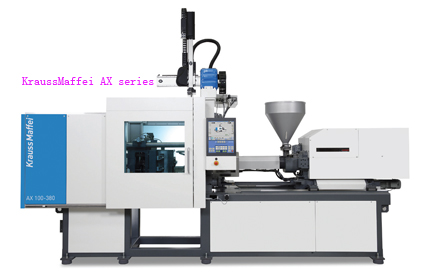
" The pace of technological change in the plastics industry is accelerating continuously. Around the world processors are looking to counter intense pressure on prices with efficiency gains and they need to see fast returns on every investment. The return on new production machinery depends on two factors - operating costs and productivity. This is why it pays to invest in complete manufacturing cells where the injection moulding machine and the robot are engineered as a perfect team," according to Dr. Karlheinz Bourdon, member of the board of KraussMaffei Technologies GmbH. With Allrounder A - "A" stands for Alldrive - Arburg offers an electric moulding machine that features modular drive technology. The main axes of the Alldrive machine - mould opening and closing, injection and dosing - have been equipped with electric drives as standard. The other movements such as ejection, nozzle movements and mould functions can be operated either hydraulically or electrically, depending on the operating requirements. In this way the customer can equip his electric moulding machine individually and use it in a very flexible way. This concept allows the advantages of both systems to be combined. The electric moulding machine has sufficient hydraulic power at its disposal precisely where it is needed, and the highest level of electro-mechanical accuracy coupled with economical energy consumption wherever this is desirable for the production task at hand. The current Alldrive series includes the four sizes 370 A, 470 A, 520 A and 570 A and covers clamping forces ranging from 500 kN to 2000 kN. As the production of high-quality, technical components is gaining increasing importance, the machine can meet the complex production needs. Dymotek and Arburg also joined to offer a two-component Allrounder 570 A with the Multilift V robotic system for processing thermoplastic and liquid silicone (LSR) integrated in a complex production cell. This involves combining complex mould engi
NIKE AIR FORCE