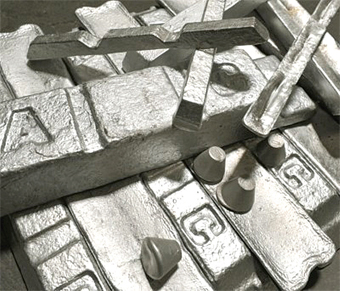
Alloys were originally developed in the early 1950s for aerospace applications, in which their high strength-to-density ratios were especially attractive. Although alloys are still vital to the aerospace industry for these properties, recognition of the excellent resistance of titanium to many highly corrosive environments, particularly oxidising and chloride-containing process streams, has led to widespread non-aerospace (industrial) applications. Because of decreasing cost and the increasing availability of alloy products, many alloys have become standard engineering materials for a host of common industrial applications. In fact, a growing trend involves the use of high-strength aerospace-founded alloys for industrial service in which the combination of strength to density and corrosion resistance properties is critical and desirable. The excellent corrosion resistance of alloys results from the formation of very stable, continuous, highly adherent, and protective oxide films on metal surfaces. Because metal is highly reactive and has an extremely high affinity for oxygen, these beneficial surface oxide films form spontaneously and instantly when fresh metal surfaces are exposed to air and/or moisture. In fact, a damaged oxide film can generally reheal itself instantaneously if at least traces of oxygen or water are present in the environment. However, anhydrous conditions in the absence of a source of oxygen may result in corrosion, because the protective film may not be regenerated if damaged. The nature, composition, and thickness of the protective surface oxides that form on alloys depend on environmental conditions. In most aqueous environments, the oxide is typically TiO
2, but may consist of mixtures of other oxides, including TiO
2, Ti
2O
3, and TiO. High-temperature oxidation tends to promote the formation of the chemically resistant, highly crystalline form of TiO, known as rutile, whereas lower temperatures often generate the more amorphous form of TiO, anatase, or a mixture of rutile and anatase. Although these naturally formed films are typically less than 10nm thick and are invisible to the eye, the TiO; oxide is highly chemically resistant and is attacked by very few substances, including hot, concentrated HCl, H
2SO
4, NaOH, and (most notably) HF. This thin surface oxide is also a highly effective barrier to hydrogen. Alloys, like other metals, are subject to corrosion in certain environments. The primary forms of corrosion that have been observed on these alloys include general corrosion, crevice corrosion, anodic pitting, hydrogen damage, and SCC. In any contemplated application of titanium, its susceptibility to degradation by any of these forms of corrosion should be considered. In order to understand the advantages and limitations of alloys, each of these forms of corrosion will be explained. Although they are not common limitations to alloy performance, galvanic corrosion, corrosion fatigue, and erosion-corrosion are included in the interest of completeness. Alloys are widely used in hydrogen containing environments and under conditions in which galvanic couples or cathodic charging causes hydrogen to be evolved on metal surfaces. Although excellent performance is revealed for these alloys in most cases, hydrogen embrittlement has been observed.
Producing quality aluminium alloys Lucky Alloys is renowned as one of the largest secondary and semi-primary aluminium alloy manufacturing facility in the Middle East and owes its strong industry position to a presence dating back to 1986.
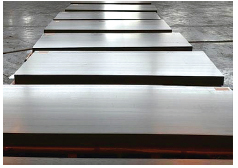
Lucky commenced as a producer of aluminium casting alloys for a range of industries and then expanded to embrace a wider range of markets like the electrical and automotive sectors. The year 1989 witnessed a str
Runners Alliance