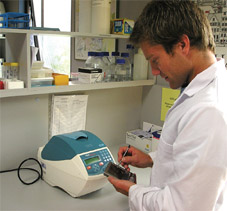
Automating Maintenance and Service of Medical Instrumentation Using Handheld Devices
Source: Release Date:2010-05-14 167
Naaman Shibi, Techs4Biz Australia Pty Ltd.
HAWTHORN, VICTORIA-Over the past few years, automation has proven to be an important tool in the management of biomedical inspections, maintenance and service activities. It enables effective equipment tracking, scheduling, service management and management of parts and inventories. Benefits include improved productivity, reduced downtime, increased equipment life expectancy, compliance with regulations and lower overall maintenance costs. In the past, many automation solutions offered "paper-based" software, which produced paperwork orders to perform field service. Once paper forms were returned to the office, they would be "manually" entered and integrated with the software product. The same concept applied to Web-based solutions, which required paperwork orders and computers to enter the data back onto the system. In recent years, the role of handheld devices and personal digital assistants (PDAs) has gradually increased from "toys" used by early adopters to day-to-day tools deployed by organisations that want to improve their staff's productivity and minimise unnecessary administrative tasks. Can a PDA (Handheld Device) Automate Biomedical Equipment Maintenance and Replace Paperwork Orders? Absolutely. Most handheld devices operate on either the Palm Operating System (PalmOne) or Pocket PC (Microsoft), and both platforms can easily handle biomedical inspection and service software. Handheld devices should provide information that already exists on paper forms or on the desktop and at the same time improve one's ability to access and utilise the data. For example, if a user fills out a monthly inspection report providing specific information, the handheld device should fulfill the same function. A handheld user can pick from a list of possible choices and/or write or type in information according to the organisation's requirements and preferences. Handheld devices make current, past and future information accessible and easy to use. Handheld software should also be tailored towards biomedical field service personnel who need to perform their tasks using easy-to-use screens and functions. Furthermore, by simplifying navigation buttons and minimising keystrokes, field technicians can learn to operate their PDA software in a very short timeframe. Handheld applications specifically designed for biomedical inspections, maintenance and service activities should deliver the following functionalities: List all information required by technicians, engineers, inspectors, and maintenance personnel to perform their tasks, including equipment list, task list, activities, parts, instructions, etc. Provide easy-to-use navigation, search capabilities and quick access to information. Allow technicians to enter as much information as needed. Automatically track labour and apply it to timesheets (if applicable). Enable technicians and inspectors to record recommendations and/or quickly create new corrective work orders. Provide additional value-added features, such as asset tracking and audit. Produce reports or invoices as required using portable printers. Handheld devices can include validations that allow or disallow data entry. They can also provide the user with historical information pertaining to previous service orders or particular pieces of equipment. Furthermore, barcodes, timestamps and scanners attached to handheld devices enable quick identification of devices and equipment, identify points of entry and exit, improve efficiency and minimise human errors. Handheld applications should also be designed to minimise the amount of data entry and keystrokes required by incorporating a variety of techniques, starting from pick lists, through checkboxes, to lookup lists and automatically generated results and shortcuts. Minimising the amount of data entry that the end user has to perform is rMarki
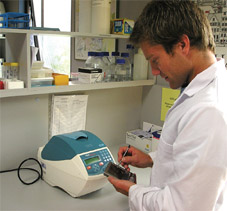
You May Like