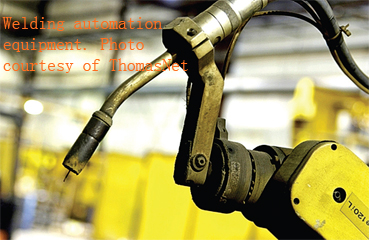
Automating welding operations
Source: Release Date:2009-12-07 212
Choosing the correct automating welding system for your company's operations is crucial to ensuring a wise investment. In most purchasing decisions, successful investment in automation depends almost entirely on planning and preparation. The rewards can be significant, but when you make the wrong decision, so can the costs Why automate A single automated welding system can do the welding done by as many as three employees. Often with better-quality results and eliminate bottlenecks that occur at the welding stage of the manufacturing process. In addition, an automated system can lower consumable costs by using only as much filler metal. A filler metal is a metal added in the making of a joint through welding, brazing, or soldering. Four types of filler metals exist: covered electrodes, bare electrode wire or rod, tubular electrode wire and welding fluxes. Also, business perception is important. If you are in an industry where your competition is still welding by hand, investing in an automated system can provide you with a real, though not quantifiable, competitive advantage in the minds of customers.
Payback While the benefits generated by automation can be significant, those benefits come at a price. Many companies, especially smaller fabricators and those with frequently changing production lines need to see a payback period. On the other hand, companies that know their production needs will not change for years can often justify a longer payback period. Take a cold, hard look at your company's business, and determine what sort of work it does, and what projects are likely to be coming along in the foreseeable future. Looking strictly at current production requirements, calculating payback first involves determining your current product cycle times, and comparing those values to the cycle times an automated system can achieve. If you need to produce X number of parts per week for example, and an automated system can produce those parts in 1/4 the time required by manual welding, it's obvious that productivity can be increased by 75%. Bear in mind that about 70% of a welding operation's costs are for labour. Overwelding is a common and costly occurrence in semiautomatic welding. Automated systems also use bulk filler-metal drums, which can further reduce filler-metal costs by requiring fewer changeovers and yielding bulk-purchasing discounts. Making the leap Automating a welding cell won抰 be the right course of action for everyone, but the capabilities of automated systems and their increasing affordability is making cell automation a good choice for many companies. If the system is to be automated, shop floor personnel must be able to provide the robot with a consistent supply of material, and ensure that the parts being welded do not accumulate in another part of the plant. Repeatability and measurability is a precursor something that proceeds. The company that does not have a blueprint (preferably an electronic blueprint) probably won't be able to automate the welding of that part. A thorough understanding of existing productivity is also required to provide a baseline from which to measure the improvement delivered by the automated system. Further, for successful, economical automation, parts should have large batch runs (although there are some exceptions to this rule), tolerances within thousandths of an inch, and configurations that allow access by an automated gun. Independent Make sure your company employs the workforce needed to automate its operations. An automated welding system requires a trained operator to make sure it runs properly. It takes longer to become a skilled welder than it does to learn how to operate an automated welding system, it usually makes sense to train a welder to operate the automated system, rather than trying to train a tech-savvy employee in proper weld-quality identification and troubAir Foamposite One Glowing
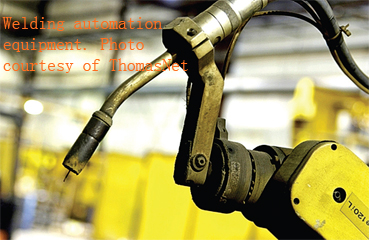
You May Like