By DR MICHAEL BUNK TüV SüD Industrie Service
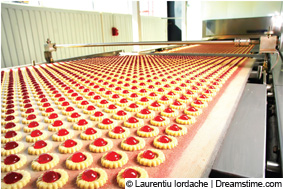
MORE and more manufacturers of systems and installations have the aim of optimising the energy efficiency of their products and documenting this achievement to third parties, primarily motivated by a commitment to sustainable development and the urge to gain competitive edge. However, straightforward types of classification such as those used for household appliances are not sufficient for complex systems. In addition to assessing individual components, the certification process must also examine their interaction during subsequent operation as well as the specific conditions under which the systems operate. The objective is to provide a certification service for complex system technology that serves as a reliable seal of quality for the producer while also identifying potential areas where savings can be made.
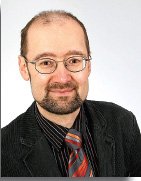
Manufacturers of systems and installations who aim for energy efficiency can now document this to their customers. In a pilot certification, TüV SüD Industrie Service evaluated two oven models of a German supplier of bakery machines and issued the first "Energy Efficient Systems" certification mark. In addition to examining the technical components of the ovens , the procedure also assessed how efficiently the systems will work during future operation. In an initial pilot process for "Energy Efficient Systems" certification, TüV SüD experts from Dresden, Germany, examined the energy efficiency and areas of potential savings of new bakery machinery produced by a German oven manufacturer. But what does this certification process involve in practice? The certification process Before the certification process begins, a complex energy audit is performed in which TüV SüD experts compare the actual condition of the product with the potential savings that would be generated by its use of state-of-the-art technology. Energy efficiency testing not only applies to the technical components that make up the systems, but also investigates whether the systems will function efficiently during future operation. To evaluate this, a variety of operating conditions and modes are analysed, taking general technological and economic conditions and the total cost of ownership into consideration as well as assessing economic aspects and the company's competitive position. The certificate is only awarded when all minimum testing criteria and requirements have been met. These criteria include proof that a continuous improvement process for the energy efficiency of the technology is in place and that options of influencing the system's energy consumption have been offered and presented to the future operator. A close examination of the machines reveals whether they incorporate the current state of the art in technology (and efficiency) in an effective way. Given the diversity and complexity of technical systems and the various modes of operation, a comparison of parameters is difficult, so that research on industry-specific benchmarks and parameters is conducted and incorporated to facilitate this process. If appropriate benchmarks are unavailable or insufficiently informative, energy consumption parameters for preceding models of the same systems or a comparison of components is helpful. In this case, the power and energy demand are generally measured and compared. Industry benchmarks: comparing baking ovens In the bakery industry, a comparison of energy consumption parameters for systems and installations is complex, since the design and construction of bakery machinery and ovens differ widely; the available baking area and technical specifications vary from oven to oven. A further option is to collect data and perform an analysis based on two different generations of the same product model. In the case at hand, whe
Nike Air Penny 5