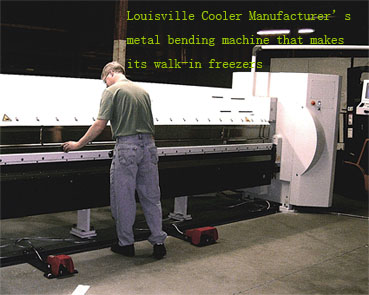
Bending changes metal to different shapes
Source: Release Date:2010-03-29 165
Bending metal is a process in which metal is changed by deforming the material and then changing it to many different shapes. The metal is stressed beyond the yield strength but also below the complete tensile strength. This does not cause the surface area of the material to really change that much. The bending can refer to deformation about 1 axis. A standard die set is used to produce a great variety of different shapes. Once the material is placed onto the die, it is then positioned in place with gages and stops. It can be held in place with things called, " hold-downs." The upper part of the press uses the ram with the right shaped punch that descends and forms the V-shaped bend in the metal. The bending can be done using press brakes. Press brakes normally have a capacity of around 20 to 200 tonnes that allows them to accommodate stock from 1 millimetre to 4.5 millimetres. Bigger and smaller presses can be used for more specialised applications. Programmable back gages and multiple dies sets currently make it a very economical process. Air bending, bottoming One type of bending is air bending, it is done with the punch touching the piece of work in question and not bottoming in the lower cavity. As the punch gets released, the piece of work ends up bending under the pressure of the air. The amount of space that it springs back depend on the thickness of the material the grain, temper and the actual material itself. The spring back can usually range from five to ten degrees. Normally, the angle is used in the punch and the die to reduce the setup time. The inside radius of the bend will be the same as the radius of the punch.
Bottoming is also known as coining. It is the process of the punch and the workpiece bottom on the actual die. This controlled angle will give very little spring back. The pressure needed on this type of press is a lot more than air bending. The inside radius of the workpiece will be at least a minimum of one material thickness in bottoming. Rolling Rolling is the best known way to bend metal, perhaps because it is the least costly. Rolling uses an appropriate size die that adjusts to the steel tube, angle, pipe, channel, bar or steel beam and revolves at the same peripheral speed, turning in opposite directions. As the metal passes through the roll, the machine applies pressure to bend the tubing or the beam to the desired radius. It is effective when the material, metal, must be bent a great deal. For instance, it can produce bends up to 360 degrees. This method is suitable for producing steel coils, spiral staircases and the like. There are different kinds of rolling processes. Hot rolling, above the re-crystallisation temperature, mostly produces sheet metal. Most non-ferrous metal structures are rolled cold, but steel is usually rolled hot. Because rolling requires less set-up work and uses pre-made dies, the cost is less than other ways to bend and form steel, so companies often choose this when it suits their specifications. Sometimes it may be necessary to be able to bend a metal when no heat or air is available. In this case, it will be possible to bend the metal providing you have a secure area to fix the metal to before you begin bending it. You can use similar steps to bending with hot metal, but take note not to use the cooling steps that you would normally use. If for example the metal was brass, you may not need to bend it when it is cold at all as you may even shatter it or crack it. Do not bend any type of rod or even rectangular bar when cold past sixty degrees as it will most probably crack the metal. The best way to bed the metal would be with an anvil, you could also use some tongs to make sure the metal is in place before you attempt to bend it. Mandrel, press, table forming bending Mandrel bending is also fairly well known. In this process, a metal shaft, or mandrel, is fittedNike Air Flight Huarache
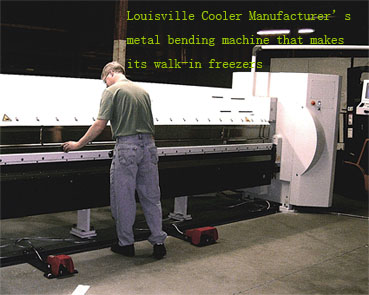
You May Like