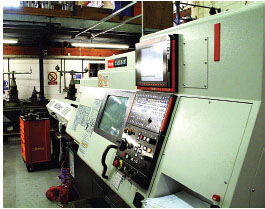
CAD/CAM for Medical Machining
Source: Release Date:2009-12-08 169
Manufacturing Engineering: How can CAD/CAM software help boost productivity for machining medical parts? Hanan Fishman:Broadly speaking, CAD/CAM boosts productivity for machining medical components by speeding up CNC programming and reducing machine setup time. CAD/CAM speeds programming time by allowing the programmer to automatically generate an NC program from engineering design for a particular component. The more complex the part, or complex the machine on which it is being manufactured, or some combination of the two, the greater the time-savings provided by a CAM system. Perhaps the even more important productivity benefit of a CAM system for machining medical parts is its ability to reduce machine setup and prove-out time. With the appropriate CAM system matched to an application, users can visually prove out the machining process and catch any errors on a part before tying up valuable machine time. This is especially critical in medical manufacturing where lot sizes may be small, as in the field of medical machining, one size rarely fits all. ME: Describe your 'divide-and-conquer' approach to machining. Fishman: PartMaker's patented 'divide-and-conquer' approach allows the programmer to view the part the same way the multiaxis lathe on which it is being machined sees it. The software does so by breaking down a part into a series of machining tasks for different part faces programmed in 'Face Windows.' It lets the user see a multiaxis turn-mill for what it really is, which is to say, not just a mill and a lathe, but really a lathe with up to nine different types of milling capabilities, depending on the capabilities of the machine and the engineering requirements of the part at hand. Each Face Window in PartMaker serves a dual role in automating the programming of a part that will be made on a multiaxis turn-mill center or Swiss-type lathe. First, the Face Window automatically establishes a coordinate system for a specific task. For example, Part-Maker lets the user, through the selection of a given Face Window, choose whether a feature will be turned, will be milled on the face of the part, milled on the diameter of the part, or milled in some inclined plane. Second, the choice of Face Window automatically determines the type of machining that can be done in a given coordinate system. Each of these machining functions corresponds to a different mode of operation for a multiaxis lathe. Thus, this approach lets a user quickly program a part in the exact way his machine will cut the component.
ME: What types of medical components are made using your software? Fishman:The range of medical components can be very broad, from the parts that go into the assembly of a hospital bed to the tiny bone screw used to hold pieces of the body together in surgery. The most common medical parts machined with PartMaker are of the second category, a group collectively known as implants, or components that end up inside the human body during and after a surgical procedure. Additionally, a number of the medical components made with PartMaker go into making medical devices, including surgical instrumentation. "The importance of quality and traceability is paramount in medical applications." ME: What does your software's new seamless solids programming capability offer users? Fishman:PartMaker's recently improved solids programming allows a user to directly program onto a solid model and automatically detect the engineering data resident to that solid model. This further automates programming when a solid model is available. More and more, medical parts are designed in 3-D using solids modeling, so having the ability to automatically generate an NC program using the inherent properties of that model with minimal intervention can greatly speed up programming. ME:How critical is simulation for machining medical parts? Fishman: The importance of machining simulatNike
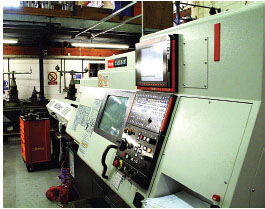
You May Like