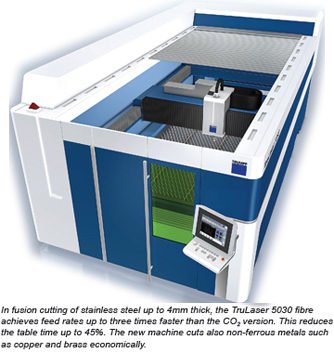
Laser cutting continues to grow in popularity with sheet metal fabricators in the Middle East. With developments in speed, cutting quality, and manufacturing economy in laser cutting, today's manufacturers have more options than ever before from which to choose the optimal manufacturing method for their specific applications. This process works by focusing the power of a high-power laser onto the surface of the material. The size of the focused laser spot is very small, typically about 0.1mm (0.004"). Because the power density in this small area is extremely high, almost all soft materials will be melted or vaporised. Depending on the applied power level, cutting, perforation, or even welding of these materials is possible. On modern laser cutting machines, most of the internal functions are automated. Focus point is changed remotely via a cutting database or technology table. Assist gas change and pressure are system-controlled as well. The numerically controlled cutting database has taken over almost all of the operational commands, leaving simple functions such as nozzle or focus lens alignment or change to the operators. Higher laser powers of 2,500 watts and more have advanced the technology too. These high powers can process thicker metal, but the real advantage has been increased feed rates on thin metals. Cutting speeds on metal have increased almost threefold with the use of inert gas. Ultrafast flying-optic laser cutting machines, introduced in the late 1990s, and punch-laser combinations have been gaining ground. Ultrafast laser cutting systems that use linear-drive technology offer fast part processing time in combination with accuracy and reduced setup times. With the integration of several work stages in the punching unit, the manufacturing of a variety of components becomes possible at a lower cost per component on punch-laser combination machines.
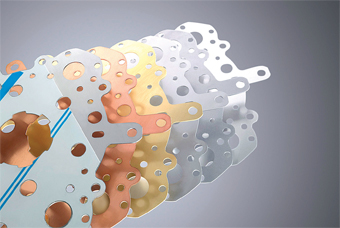
As a result of the harsh economic climate of the past two years, the need for higher volumes of the same part numbers is disappearing. Today, many manufacturers are looking closer at lasers and combined fabricating systems to meet low-run production while having the flexibility to accommodate any market requirement. However, it's important to understand how the features of the current technology will fare into the future. Evaluating which features will become obsolete and costly in the years to come is the real challenge. Material thickness Lasers can be used to process expensive alloys as well as traditional materials such as stainless steel. However, knowing the strengths and weaknesses of laser processing is the key to determining whether or not a laser is the right choice for cutting. Laser cutting becomes less effective when material thickness increases. For instance, lasers may be ineffective for cutting carbon steel thicker than .4-inches. Laser cutting thickness limitations are determined by heat conductivity, surface reflection at 10.6 microns, the vaporisation point of alloys, the types of alloys, surface tension of molten materials, and part geometry. As thickness increases, the likelihood of a blowout or thermal runaway also increases. By highly focusing its beam and reducing its spot size, the laser becomes a sharper cutting tool. For example, a laser's cutting ability increases significantly when the spot size is narrowed from even .004 to .011-inches in diameter. Ideally, the wavelength will allow 100 percent absorbability with the material. In many instances, the laser's ability to cut can be further improved by focussing the assist gas. The assist gas serves two purposes: to help in combustion, and to blow the debris or molten metal away from the kerf. Other conditions contribute to processing problems. If the thermal conductivity is high in a material such as aluminium, much of the energy is
Nike Air Max