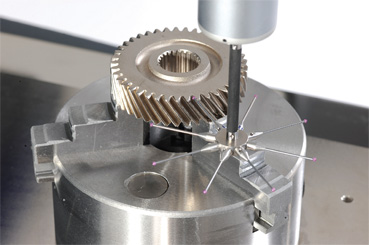
When considering an upgrade to your machine shop, Electric Discharge Machining (EDM) operations should be on your list. The primary goal for incorporating an EDM machine operation to your shop is to reduce the cost of manufactured parts and improving overall part quality. EDM is a general term that is used to describe any machining process that uses a charged electrode to produce a spark that removes metal. However, the process will work on any material as long as it is electrically conductive. One method uses a very thin wire as the electrode and the charged energy from the electrical sparks that are created between the wire and the workpiece melts and vaporises material on the workpiece. The work is performed in a fluid, like de-ionised water, to prevent premature spark discharge and to wash away the waste material and keep the workpiece material cool. EDM has some unique properties that can be exploited by any modern machine shop: hardness of the workpiece material does not affect the cutting speed and all the following materials can be machined - inconel, titanium, hastalloy, hardened tool-steel and kovar. There is no physical contact between the wire (electrode) and the workpiece so there are no physical cutting forces involved which allows very delicate parts to be machined. No special tooling or workholding clamps are required. No burrs are ever created on the workpiece. No mature machining technique today offers such potential for automation as does EDM. The process is a natural for the kind of unmanned operation managers' dream about for their shop. It's relatively clean, relatively safe, quiet and compact. It's a fully understood process which has, in 25 years or so, gone from exotic Russian invention to Swiss precision machine to Japanese production tool. It's a must for many hard and hard-to-cut materials and it's economical as well. EDM's growing role Although EDM first became recognised as an excellent alternative method of producing 3D cavities for mould and die work, many of the very early applications were devoted to hole-drilling. Not only did EDM work well on non-flat surfaces, but material hardness ceased to be a factor. The EDM erosion spark doesn't care whether the part is made of soft 1012 steel or hardened carbide. The only requirement is electrical conductivity in the workpiece. Since its development, EDM has been used for hole-drilling, even though penetration rates were quite slow. Its main advantage as a hole-drilling method was the ability to accurately drill holes in surfaces that were slanted or spherical. This is possible because there is no direct contact between the EDM electrode and the workpiece to generate mechanical forces. The alternative drilling methods, including EDM, account for about five percent of current hole-making production.
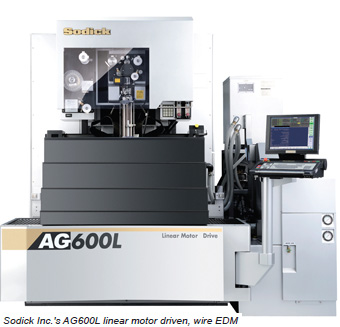
New EDMs for your shop upgrade The latest EDM machine developments were featured during the recent IMTS 2010 in Chicago. Technology providers are constantly reviewing the latest characteristics and trading development variables to develop the best set of machines for the industry to get the virtually millions of machine shops, serious (and maybe not so serious) hobbyists and students introduced and involved in EDM. This is a critical factor in seeding manufacturing interest in many locations at the same time. The access to EDM capabilities comes the ability to drive experiments and innovations. With the ability to learn the capabilities of lower-end machines, the need to upgrade and generate innovations into larger machines might be fostered. In essence, make the ability to get into the basics of EDM extremely easy and one will create and generate a steady flow of consumers for upgrades, extensions and accessories for years to come. Cost-friendly EDMs Sodick Inc.'s newest cost-friendly, wire EDMs, the VZ300L a
Air Jordan