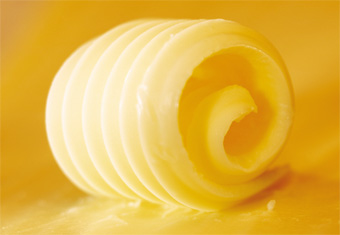
MARGARINE, like other food products in many factories today, is produced under strict traceability procedures. In order to be able to react fast, food manufacturers need to be able to trace the origins of the ingredients in case of contaminations. The traceability procedures covering the ingredients, the production and the final product not only result in an enhanced food safety, but also in a constant food quality since the raw materials have to meet distinct specifications and the products are manufactured and distributed under defined conditions. Traceability demands can easily be implemented in the control system of the factory. Apart from complete processing lines to the producing margarine and other crystallised fat products, Gerstenberg Schröder delivers the GS Logic system, which is designed to control, record and document important parameters concerning the complete manufacturing process. The system helps to improve plant performance by creating a consistent processing environment. The GS Logic exists in three versions: GS Logic Basic, GS Logic Advanced and GS Logic Professional. The latter version includes the web-based recipe editor and web-based report system with traceability for each component controlled by the system.
Quality control Margarine and crystallised products like butter and spreads are characterised as water-in-oil (w/o) emulsions in which the water phased is finely dispersed in the continuous fat phase. The ingredients used for margarine production can be divided into water-soluble and fat-soluble ingredients, and obviously the documentation is linked to these phases. The subsequent processing is divided into the following production steps: emulsion, preparation, pasteurisation, crystallisation, and filling or packing.
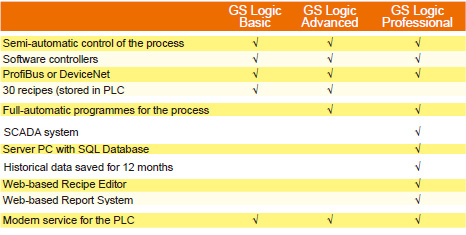
All raw materials are subject to quality control when received and can only be used in production when it has been verified that they meet the specifications. An example is the solid fat content (SFC) profile, which describes the amounts of solid at given temperatures for a fat is typically checked when fats are delivered. Batch numbers of the individual ingredients can be registered in the specific margarine batch for traceability. The specific margarine production is recipe-controlled and the production is typically divided into several batches of the same recipe. In this way, the final margarine product can be linked not only to the recipe but also to the individual batches of the product-related production. When the emulsion is created in the premix tank by adding the melted emulsifier blend to the melted fats and oils and adding the water phase subsequently, the flow meters or weight cells control and ensure that the correct amounts of the various ingredients are added. The control system registers and files these amounts for later reports along with the tank temperature in the incoming phases and final emulsion. The emulsion is pasteurize prior to processing mainly to guarantee destruction of any unwanted micro-organisms and of all pathogenic bacteria, but the pasteurisation process also ensures a constant and stable inlet temperature that facilitates the later process control.
Historic data logging The GS Logic system is equipped with a password system and features historic date logging of all temperatures, pressures, loads and speeds of the units involved in the margarine processing line including the capacity and output of the high pressure pump (litres/hour and back pressure), product temperatures during the pasteurisation process and crystallisation, cooling temperatures (or cooling media pressures) of the scraped surface heat exchangers (SSHE), speed of the SSHE and the pin rotor machines, load of the motors running the high pressure pump, SSHE and the pin rotor machines.
KD VIII N7 Glowing