
A growing range of building materials are now being made of plastic and subsequently painted or coated. Painting provides plastic surfaces with an attractive appearance and a pleasant feel. It also protects the substrate from mechanical, chemical and physical influences such as abrasion, scratching, stone chipping, environmental and household chemicals, weathering and UV radiation.
Pretreating plastic parts Depending upon the manufacturing process, plastic parts are contaminated with release agents or other impurities which make pretreatment necessary. The various characteristics of the plastic surface, for example cleanliness, wettability, paint adhesion and partial dissolving when exposed to paint solvents, play an important role in the painting process. Parts are usually cleaned in so-called power wash systems which work with aqueous cleaning agents. CO2 snow jet cleaning can be used as an alternative. This process makes use of liquid carbon dioxide as a cleaning medium, which is expanded as it passes through a nozzle and is accelerated with compressed air to ultrasonic speeds. Thanks to a combination of mechanical, thermal and chemical effects, the CO2 snow jet removes film-like contamination and particulates when it strikes the surface of almost any material, in a dry and residue-free fashion. The inline capabilities and minimal space requirements associated with this process allow for direct integration of cleaning into the painting process, thus ruling out the possibility of renewed contamination of the component, for example during transport or storage. Despite effective cleaning, adhesion problems may occur after painting, for example with non-polar plastics which demonstrate only minimal surface tension. Surface polarity can be increased by means of various processes. Flaming, during which the plastic surface is briefly exposed to a gas flame with excess oxygen. As a result, molecular bonds in the surface of the substrate are broken down, and free, active ions in the flame are integrated. Corona treatment conducted with an alternating voltage electrode by means of which atmospheric oxygen is ionised with the help of corona discharge, resulting in oxidation of the plastic surface. While plasma treatment which is suitable for processing individual parts and bulk goods, during which the surface is simultaneously cleaned and activated. This dual function is based on physical and chemical reactions involved in the process: The atoms released in the plasma "bombard" the surface of the component to be cleaned and function like a miniature sand-jet in the nano-range.
Increasing productivity and reducing costs Primerless painting is experiencing a strong upward trend, and is being used to an ever greater extent. The bonding function of the primer is integrated into the base coat used in these water-based paint systems. The objective is to speed up the painting process and increase productivity. Production throughput rates can be increased for many plastic components which are printed or painted through the use of infrared drying. In many cases, this also offers the advantage of reduced electrical energy consumption in comparison with hotair ovens, because the infrared radiator only needs to be switched on when heat is actually required. Where coatings for plastic parts are concerned, there抯 also a tendency towards powdered enamel systems as an alternative to liquid paints. Reasons for this include the outstanding environmental friendliness of the utilised powdered enamels, as well as possible cost savings.
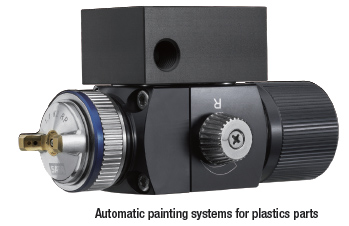
The use of UV paints is advisable where short cycle times and high-quality appearance are of top priority. These solventfree paints are distinguished by especially short drying times, thus allowing for high-speed production. At the same time, relatively little energy is
Nike Hyperdunk 2018