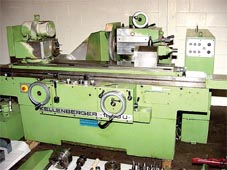
The United Arab Emirate has decided to massively increase infrastructure spending for 2010. About Dhs7.6 billion (US$1.56 billion), or 17.5% of the Dhs43.6 billion (US$8.99 billion) budget, has been devoted to infrastructure projects. Advanced manufacturing and assemblies, high dimensional accuracy and fine surface finish will play an important role in achieving UAE's proposed infrastructure projects. One of the best economical methods of producing metal parts that deliver double-digit productivity gains is by cylindrical grinding. While grinding a flat surface is the most common type of grinding operation, cylindrical grinding certainly has its place in precision machine tooling. This operation is not like the lathe where a cylindrical workpiece is rotated and a cutting tool is brought against it to cut it down to a desired diameter measurement. Grinding a cylindrical object achieves a similar effect, but offers a much greater degree of flexibility and sophistication. In cylindrical grinding, the external cylindrical surfaces and shoulders of the workpiece is ground. The workpiece is held between the centres or in the chuck of the machine. In a global economy, with cheap labour available but at great distances, and complicated by cultural barriers, time zones, and long supply lines that require high-finished goods inventory, adopting these improvements will help manufacturers to minimise or overcome their offshore competitors' cheap-labour advantage. Grinding can achieve a very high level of precision. Workpieces can be ground to an exceptionally high finish and to within plus or minus 0.002 millimetres in diameter, or better. For those who are still thinking in the older feet and inches measurement system, that's a very impressive plus or minus one ten thousandth of an inch-about one thirtieth of the diameter of a human hair. Of course, while a cylindrical grinding machine is capable of achieving this high level of tolerance, it does require a trained and experienced operator to routinely produce work to this level of precision. However, today's grinding machine tools use computerised programs to enhance their capabilities and level of precision. They can be programmed to perform complicated and involved operation in a way that can reduce operational time and ensure a consistent result. Grinding cylindrical workpieces differs from the operation of a lathe in one
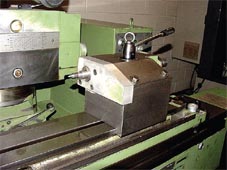
important manner in that the cutting tool, the grinding wheel, rotates as well as the workpiece. Both items usually rotate at different speeds, which require a precise calculation to determine the optimal cutting speed. As with most cutting operations, it is necessary to use a coolant fluid to keep surface temperatures within acceptable limits, as well as to lubricate the cutting operation to ensure a better and smoother finish. Depending on the type of material being ground, the coolant is usually light oil or water soluble oil that is recycled and reused through the system by a pump. Grinder wheels can be made from different materials. The hardest, and therefore the type generally used for heavy grinding, are made from industrial diamond or cubic boron nitride. However, aluminium oxide or silicon carbide grinding wheels are more commonly used as they are less expensive to produce and use. The surface finish of an efficiently carried out grinding process is usually much finer than that of a lathe operation. A smooth glassy finish lacking any obvious machine ridges is typically achieved. That, coupled with the extremely high-level of fine tolerance possible makes cylindrical grinding very suitable for operations that require absolute precision. Productivity There are computerised advances to process planning that allow multi-tasking in grinding. Second, there are advances in grinding wheels, from smaller siz
Air Max 95 Flyknit