在机械加工中通常把孔深与孔径之比大于5的孔称为深孔。深孔钻削时,散热和排屑困难,且因钻杆细长而刚性差,易产生弯曲和振动,一般都要借助压力冷却系统解决冷却和排屑问题。本文将为您分析深孔钻的一些动态。
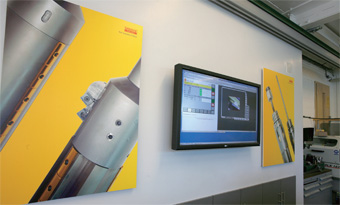
Hole drilling is the most common process performed among metalworking operations. A hole is defined as a deep hole when the depth-to-diameter, or aspect, ratio is more than 5-to-1. For example, a 5-inch deep by 1-inch diameter hole is considered deep, as is a 0.125-inch diameter hole that is 1- inch deep. In hole drilling, the goal is to produce holes accurately, repeatably, and with superior surface finish. For a drilling system to produce deep holes with both speed and precision, it must overcome the inherent problems and limitations of the deep-hole-drilling process. When drilling a deep hole, a shop must use a machine with at least 10hp for every 1- inch of drill diameter; a drill with a strong, sharp chipbreaker; and a lot of cutting fluid. Chip disposal is the main problem users of deep-hole-drilling systems must contend with. The deeper you drill, the farther the chip must travel from the tool's cutting edge to the top of the hole. The greater the distance, the greater the chance the chip will jam or bind in the drill flute on the way out. The difficulty of delivering cutting fluid to the drilling face at the bottom of a narrow hole further complicates the deep-hole- drilling process. If too little coolant makes its way to the drillhead, the risk of metal building up on the cutting edges increases. This built-up edge (BUE) hinders the tool's ability to break chips. Another function of the coolant is to fight friction between the drill, chip, and hole wall. If friction is allowed to build because of a lack of coolant, the resulting torsional forces can snap the drill. The basic principle in deep-hole drilling is to press the tool's carbide cutting edges into the work at high feed rates. This type of machining generates high cutting forces, and it takes a rigid tool to avoid deflection in the presence of these forces. Also, the adverse conditions typically found in a deep hole make it difficult for an operator to maintain straightness, roundness, diameter, and finish. If the drill begins to produce a hole with flawed geometry or finish, the problem usually becomes compounded the deeper the drill cuts.
"When drilling a deep hole, a shop must use a machine with at least 10hp for every 1-inch of drill diameter, a drill with a strong and sharp chipbreaker, and a lot of cutting fluid."
Drill geometry Drill geometry is a key factor in a successful deep-hole drilling. Flute size and spacing affects chip evacuation. Drills with open flutes enable chips to flow up and out of the hole more easily, especially with coolant-through-spindle systems. But without good coolant flow at the bottom of a hole, even open flute designs are subject to chip clogging and drill breakage. Today' s technology enables toolmakers to design tools for drilling with features that better facilitate chip evacuation and minimise overheating. Made of higher-grade carbide steel for longer life, these tools feature new shapes, which assist deep-hole drilling operations. Because the tools are stiffer, they are less likely to wander in deep- hole drilling operations.
Air Max 95 VaporMax