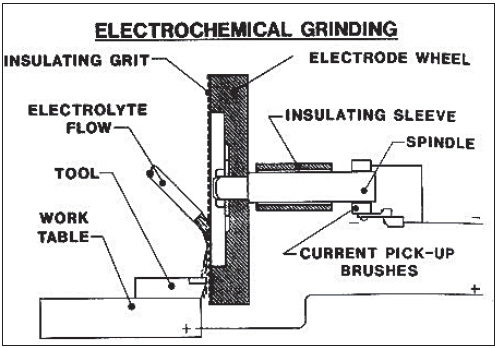
Technical and metallurgical advances have placed significant demands on the metalworking industry. The challenges faced by the industry are not only modern materials with high strength-to-weight ratios, but also with new fabrication requirements demanding greater precision and surface integrity. Electrochemical grinding equipment (ECG) is an ideal machining process that provides a better, faster, and more cost effective metal cutting and grinding solution for today's toughest materials. ECG is an electrolytic material-removal process involving a negatively charged abrasive grinding wheel, a conductive fluid (electrolyte), and a positively charged workpiece with the physical removal of material by means of charged grinding wheels. It can produce burr free and stress free parts without heat that can distort delicate components, or other metallurgical damage caused by mechanical grinding, eliminating the need for secondary machining operations. Unlike conventional grinding techniques, electrochemical grinding offers the ability to machine difficult materials independent of their hardness or strength. This is because electrochemical grinding is an entirely different machining process in which electrical energy combines with chemical energy for metal removal. Almost any conductive metal can cut with electrochemical grinding, such as steel, aluminium, copper, stainless steels, inconel and hastelloy. Nickel/titanium, cobalt alloys, amorphous metals, berilium, berilium copper, iridium neodymium iron boron, titanium, nickel/titanium, nitinol, powdered metals, rene 41, rhenium, rhodium, stelllite, vitalium, sirconium and tungsten can also be cut effectively.
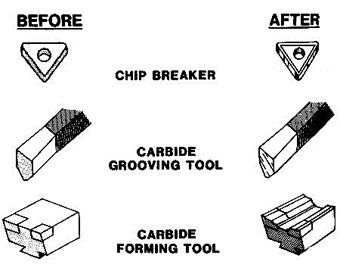
Why electrochemical grinding The most common reason customers choose electrochemical grinding is for the burr free quality of the cut. If a part is difficult or costly to deburr, then ECG is the best option. Materials that are difficult to machine by conventional methods, harden easily or are subject to heat damage are also good candidates for the stress free and no heat characteristics of electrochemical grinding. The stress free cutting capability of the process also makes it suitable for thin wall and delicate parts. In electrochemical grinding equipment, wheel wear is thus minimal and usually balanced with the level of productivity a shop wants. ECG wheels may last as much as 103 longer than those in a conventional-grinding process in some applications. There is also no wheel loading because an ECG wheel is simply wiping away decomposed part material. The electrochemical grinding process is as abrasive as a user wants it to be, and there is a limit as to how much electrochemical dissolution happens in a given timeframe. Metal removal is proportional to the amount of current flowing. Increasing the flow from 3V to 15V, for instance, decreases abrasive activity, while upping the machine feedrate increases it. The key is to come as close to a perfect balance between electrochemical oxidation and abrasive removal of the oxides. The application and the user's desired part finish and accuracies dictate a proper balance, which is not always a 50/50 split. While the mechanical aspect (the machine) of the process is accurate, the chemical part can affect tolerances. For instance, on a fairly light cut, an ECG machine easily holds tolerances within 0.001-inch. But when removing large amounts of material, such as in roughing cuts, those tolerances are closer to 0.005-inch. Conventional surface grinding typically uses shallow reciprocating cuts that sweep across the work surface to create a flat plane or groove. Another conventional surface grinding process, creep feed grinding, typically uses slower feeds than conventional surface grinding and removes material in deep cuts. Because of the abrasive nature of these processes, the equipment used
Alle Artikel