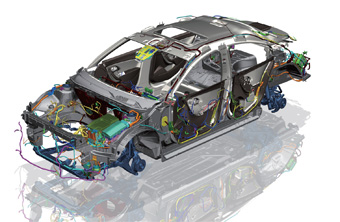
Manufacturers looking for ways to streamline all aspects of their businesses have begun to focus more attention on the product development cycle, as an area ready for improvement. Taking time and money out of the product development cycle can pay big dividends for makers of cars, as an example. In this day and age, cars are increasingly being created by distributed teams of engineers. Large OEMs are delegating significant design responsibilities to their key suppliers. Also, major manufacturers that have grown through acquisitions or mergers are seeking to realise the benefits of these business combinations by bringing together formerly isolated internal engineering teams to work together on major new projects. Hence, there is a growing interest today in solutions that will both optimise the development process and enable engineers to work more effectively together. A wide variety of engineering collaboration offerings is now available that address different aspects of this complex problem in different ways, and that provide different benefits to customers. Some of them focus primarily on creating inexpensive, Web-based interactive collaboration media, while others focus more on enabling actual engineering information to be shared quickly, completely and accurately. However, effective engineering collaboration has long been hindered by incompatible data formats among 3-D mechanical CAD systems from different vendors. This incompatibility has imposed huge time and cost penalties on companies that produce complex mechanical products. Extrapolating this figure worldwide and across other affected industries crystallises the magnitude of the problem. As design teams have become more heterogeneous, and the need for collaboration more pressing, this problem has become increasingly urgent. However, efforts to enable effective data transfer between disparate CAD systems to date have produced limited results and lagged behind the evolution of CAD software itself. A modern CAD user thinks and creates by manipulating higher-order features and constraints sometimes termed design intelligence, while prior generations of engineers were forced to work with more rudimentary geometric constructs, such as boundaries and surfaces. Up until recently, CAD translation software, services and standards only enabled the transfer of basic geometry between CAD platforms, facing engineers with the unproductive necessity of recreating much of a design manually or outsourcing the same task to a third party. Since a given part design for a new car may typically be iterated six to seven times before being finaliseFootwear