Kim Walton, Takahiko Ohmura, Mahalia Soediono, Shuwen Peng* Dow Chemical Company 汽车行业需要更轻量化 的部件,OEM需要更薄壁的部 件,在这种市场环境下,人们 对TPO共混料有着更为清晰的性 能要求:更轻、更薄、发泡及 独特的外观等,而陶氏高熔体 强度ENGAGE™聚烯烃弹性体可 更好地满足TPO所需的独特性 能,如高填充、更自由的设计 及更优质的外观等。
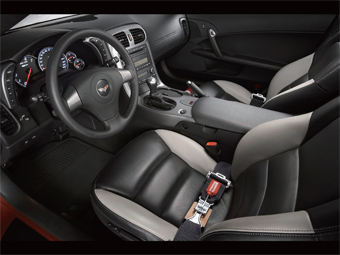
In the 1990s, Polyolefin Elastomers (POEs) made significant inroads in replacing EP rubber for automotive applications, particularly for polypropylene impact modification. The advantage of ENGAGE™POE was discussed. Recent Voice of Customer (VOC) results show that new rigid TPO specifications will call for an increase in flexural modulus with no change in low temperature impact resistance. Two study results show that high melt strength elastomers can enhance the performance of rigid TPO. In addition, one new impact modifier under development was also compared with normal POE. The results show that the new impact modifier can have improved stiffness-toughness balance.
Introduction The automotive market has seen significant adoption of elastomers over the last 20 years. Today, there are more than 3 billion pounds of elastomer used globally in the production of automobiles. The market is dominated by TPOs with 43% of the market. Talc-reinforced polypropylene (PP) impact modified with ethylene α-olefins (EAO) grew rapidly in automotive applications during the 1990抯 and is now the dominant rigid plastic material used in bumper fascia. These thermoplastic olefin (TPO) compounds continue to spread across other automotive applications in the interior as the raw material for instrument panels, door pillars, and knee bolsters.
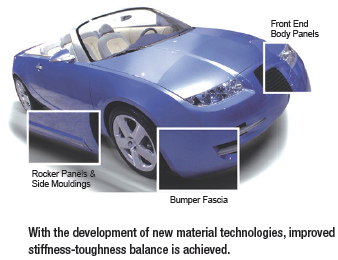
ENGAGE™polyolefin elastomers have been widely used as impact modifiers for this application. The combination of high impact efficiency, pellet form, bulk shipping capability, and excellent cost/ performance has enabled ENGAGE polyolefin elastomers to change the PP impact modifier market landscape. However, the automotive market continues to evolve. The need for increasing TPO performance demands continued development of new products. In order to better understand the market situation and to determine product needs for this market, "Voice of the Customer" (VOC) information was gathered. It was found that low temperature impact strength and high flex modulus are the two determining requirements for hard TPO in automotive bumper applications. In a paper prepared by a team from Dow Chemical Company, the utility of ENGAGE products in automotive is demonstrated. To meet critical customer requirements, i.e., maintaining ductile impact while achieving higher flexural modulus, high melt strength (HMS) ethylene/butene copolymer elastomers were compared with standard ENGAGE polyolefin elastomers for use in rigid TPO compounds.
POEs as replacement to EP rubber Before 1990, EP rubber dominated the market as an impact modifier in automotive application. In 1990s, Dow抯 ENGAGE™Polyolefin Elastomers (POEs) were created using INSITE™technology, a proprietary Dow single-site catalyst and solution process technology, enabling contr
Vans Old Skool Grise