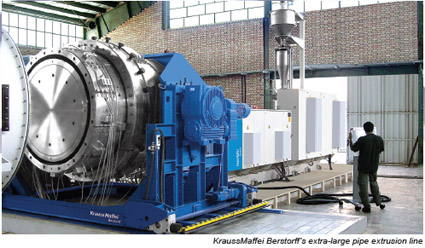
Global demand for high density polyethylene (HDPE) has been strong over the years mainly because it has remained an important material for a range of applications: for packaging products like bottles and containers; for industrial items such as drums, pallets, crates; for automotive parts such as fuel tanks; and for consumer products like toys and housewares. Demand has been on the rise in such regions as the Middle East and Africa, while Asia has become one of the fastest growing markets. Being the high density version of PE, HDPE is harder and stronger. It is lighter than water and can be injection moulded, blow moulded and welded together. It is also resistant to most chemicals and insoluble in organic solvents. With its strength and durability, HDPE has long been chosen as material for pipes. HDPE pipes are durable, lightweight and highly flexible-- providing long service life and leak-free protection for water, drainage, fuel, gas, plumbing and heating systems. Environment-friendly, HDPE pipes are energy efficient during production and can be used for a long period of time. Tests showed that HDPE used in sewerage indicate no significant change in the material's properties even after 20 years of use. HDPE pipes have been effective for underground, above ground, surface, underwater as well as floating pipe applications. Large-scale pipe extrusion With the surge in infrastructure development in the Middle East, the demand for large HDPE pipes has created many challenges for pipes manufacturers as well as those supplying machinery and technology. Iran-based P.E.S. Co. presented KraussMaffei Berstorff with its requirement for an extrusion line to produce extra-large, smooth-walled HDPE pipe with diameters of up to 2400 millimetres. Producing smooth-walled pipe in these large diameters is a world first. P.E.S. has been producing HDPE pipe, including extra-large pipe up to 1600mm diameter, on a range of Krauss Maffei Berstorff single-screw extruders for almost a decade. The extra-large pipes produced by the company in the Persian Gulf region are used in many applications, chiefly in the pipelines supplying seawater to desalination plants and cooling water to oil refineries. P.E.S. has many years of intensive experience in the production of pipes and in laying and installing complete pipeline systems. According to Mr. Mohsen Jamalian, P.E.S. Managing Director and Owner, "By working together with KraussMaffei Berstorff, we were able to set a new milestone in the world of large scale pipe extrusion. Thanks to KraussMaffei Berstorff and its top technology-from single-screw extruders to pipeheads and spiral distributor concepts-we can transfer the expertise we've accumulated with our 1600-mm extrusion line to the challenge of producing 2400- mm pipe. Also making a major contribution to our success in this area is the low-sagging polyethylene XLS12B from Total Petrochemicals." The extra-large pipe extrusion line ordered from KraussMaffei Berstorff will enable P.E.S. to advance into new dimensions and to add smooth-walled HDPE pipes 1800, 2000, 2200 and 2400 millimetres in diameter to its production spectrum. The new line, headed by a KME 150-36 B/R single-screw extruder and a KM-RKW 40- 2400 pipehead, has all the key features that have established KraussMaffei Berstorff as the technology leader in extra-large pipe extrusion. This includes the proven design of the 36D single-screw extruder, a pipehead concept where the spiral distributor design incorporates the latest rheological research, and a KraussMaffei Berstorff calibration system.
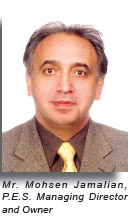
This industry-leading engineering produces pipe where wall thicknesses, outer diameter and ovality are kept within very tight tolerances. Considering that, for some types of pipe, the cost of material accounts for up to 90% of total manufacturing cost, keeping variati
Air Jordans