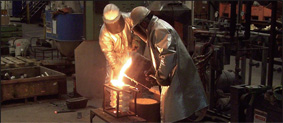
Investment casting can offer tool and die makers, machine operations, and their customers considerable finishing plus savings of time, material and labour. The process--forming metal parts in casting moulds--offers opportunities to create "near net shape" parts of virtually any metal. If an operation is fabricating parts out of bar metal, chances are its costing extra time and money. If those parts require machining, there could be a loss of significant money in scrap, especially if expensive metals or alloys are used. Investment casting offers flexibility of alloys while saving finishing time and material waste. The range of metals and alloys that can be investment-cast include: aluminium, stainless steel, cobalt and inconel. The process can also combine two or more parts into a single piece, saving on fabrication, welding or assembly, and machining time. Parts between one ounce and 30 pounds in weight can be investment-cast in close tolerances with surfaces that require little finishing. A growing number of operations that make intricate metal parts, or parts requiring repetitive, extensive machining, are finding that investment casting is a solution and forms precise and intricate metal shapes. Some fabricators look at the somewhat higher initial cost and don't realise all the savings of investment casting in time and materials. While reducing the demand on machine time is a savings, there is also added savings in costly metals used to fabricate many parts. The advantage of getting a near-net shape means less machining and also material. When you make parts with alloys, such as the nickel-based alloys, there is a pretty significant cost savings because you don't have to throw all of the metal away in chips. And of course, the machine time is less when you have parts that are cast pretty close to size.
Creating metal casting Metal casting is a useful skill that has its roots in antiquity. In order to make a casting of metal, you will need a furnace capable of melting metal alloys at high temperatures. Usually, individual metal casters will construct their own furnace. There are companies that will sell small scale furnaces but they are often costly. The most common type of casting is called sand casting, which uses sand or green sand to make the moulds where the molten metal will be poured into to form the finished product. The mould is a handmade item placed in a flask that has two parts, a cope and drag. The mould is usually made of sand, but can also be created using other ingredients like latex or even metal. It is in the mould that you will set the pattern to form the mould cavity. The mould cavity will be an impression of the pattern including the fine details, which will then be filled with the molten alloy. Pattern casting is an art form in itself, really, but anyone can create a pattern even if you have no artistic skill what so ever. The pattern is an original, which will be cast into metal. Common pattern castings include complex engine parts for models, replicas of Civil War era weapons, sculptures, and even jewelry. The pattern can be made of any material like clay, wood, and wax. The pattern material really depends on a few factors like the casting method and the availability of the material. If you are able to carve wood then you can use this skill to make patterns. There are some casting methods that call for the patterns to be made of certain materials. An example of this is the lost wax casting method, which will use wax as the pattern. When creating the mould, you will place the original into the drag of the flask and place more moulding material on top forming the cope. When the mould is dry you will carefully remove the pattern revealing an impression in the mould. If you are creating your own pattern you will need to make it with contraction allowances in mind. This contraction allo
Air Jordan