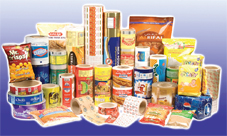
Integrated Plastics Packaging - a member of the prestigious Lufti Group - has made an unprecedented mark in the region's packaging industry. The company's commitment is reflected in the continued trust of brand manufacturers as it painstakingly works with customers to achieve their marketing goals. In a recent interview with Mr. Ziya U.I, Deputy General Manager of Integrated Plastics Packaging, he shared with the International Plastics News - Middle East (IRNE) how the company has successfully staged its approach to adjust its products and services along with the test of times. IRNE: What products and services does Integrated Plastics Packaging specialise in? ZIYA: Integrated Plastics Packaging specialises in the manufacture and conversion of customised flexible packaging materials for food, hygiene, detergent and other FMCG sectors. We are predominantly involved in bakery and pastry packaging, beverage, confectionary, dairy, dry foods, frozen foods, ice cream, spices and seasonings, detergent & hygiene packaging, along with the manufacture of plastic bags and underground caution tapes.

"We aim to create value for people we deal with by continuously upgrading our technology and production methods to come up with products that reflect effectiveness, efficiency and environmental responsibility" ----Mr. Ziya U.I, Deputy General Manager, Integrated Plastics Packaging, LLC. We serve the entire United Arab Emirates along with the Middle East and GCC region. On a global front, Integrated Plastics Packaging supplies to Australia, Morocco, Pakistan, Egypt, Columbia, Sudan, Spain, Yemen, Kenya, United Kingdom, South Africa and Ireland. IRNE: Are the products manufactured in the region? How many manufacturing units are in your network? ZIYA: All our products are manufactured locally. We currently house two manufacturing units, one in Al Barsha (Al Quoz Industrial Area) and Jebel Ali Free Zone each. IRNE: How do you maintain quality standards within the supply chain? ZIYA: At Integrated Plastics Packaging, extensive care is taken to maintain stringent quality controls over each incoming and outgoing consignment. Each batch carries a certificate of analysis (COA) without which, it would be declined. Random samples from each consignment are drawn and tallied with the details mentioned on the COA. On complete satisfaction, the materials are forwarded for production. Each outgoing consignment also carries a certification of analysis (COA), encouraging our customers to adopt similar quality control standards. On the production front, our raw materials mainly consist of films, adhesives and solvents which are procured from India, Europe, Saudi Arabia as well as locally. We believe in utilising state-of-the-art technology to improve the production process and product quality, hence all our machinery and manufacturing units have been procured from Europe, such as from Italy and Germany. IRNE: Does the company maintain its own R&D team and QC department, given the consumeroriented nature of the industry you serve? ZIYA: As of now, we don't operate an in-house Research and Development (R&D) wing, hence all our research and market analysis projects are outsourced to professional companies, specialising in this field. However, we are planning in the future to set up a holistic R&D Support structure within the company as we are very much aware on the importance of such part of the team to the overall improvement of our products and services. We have an in-house Quality Control team of professionals performing stringent checks and controls at every processing stage -- covering raw material procurement, pre-press, inspection and in-line product testing. Quality checks are made at every stage of the production process and benchmarked against ASTM (Approved American standards for te
Air Zoom Pegasus 35