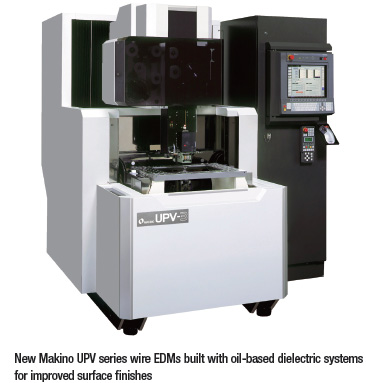
Wire EDM (electrical discharge machining) has been commercially available since the late 1970s. It has been configured with the wire in a vertical orientation for decades, so the appearance of a wire machine that orients the wire horizontally is truly a novel development. Looking beyond the novelty of its wire orientation, the machine is more properly noted for being designed to meet the special needs of micro-miniature machining applications. This is not a general-purpose wire machine reconfigured to hold the wire in an unexpected position. Rather, it is a piece of equipment specifically engineered for the machining of micro gears used in miniature moulds, fibre-optic components, inkjet nozzles and medical instruments. The demands of these applications dictated the horizontal wire and other features. Wire-EDM machines make it possible to achieve the small, odd-shaped angles and intricate contours and cavities required in the machining of stamping tools and dies. Traditional cutting techniques cannot achieve these angles in such hard metal alloys. EDM is a good machining solution for parts or materials that tend to leave tough burrs when machined by traditional methods. EDM leaves no burrs, making the deburring process unnecessary and, therefore, eliminating the dimensional changes caused by this process.
Energy-saving features reduce costs It is crucial for every company to be ever-mindful of operation and production costs. Make the most of your wire-EDM machining by purchasing units with energy-saving features, adopting efficient production practices and using the correct wire-coated wire can increase speed by 15 percent, not to forget reduce costs. Many EDM manufacturers are adding features to lower operation costs. For example, some machines offer a cost-saving mode that minimises wire consumption by slowing down the wire feed as it passes between upper and lower guides. When purchasing EDM equipment, pay particular attention to the power supply. Newer models on the market often have energysaving power-supply features that produce less heat and consume less resin, or include power regeneration circuits. Manufacturing lights-out or incorporating automation also will help minimise production costs and time. Maximise unattended run time by using multiple-parts setups and designing around unattended burning. Automating the EDM process by adding a robot for machine loading/unloading will help reduce labour costs. And, finally, for the most economical wire consumption, use the optimum wire for the application. Brass is the most cost-effective and commonly used wire for EDM. But for faster speeds, some shops use a zinc-coated wire. Although the per-pound price is slightly higher, coated wire can increase speed by 15 percent, for improved turnaround and productivity.
Edge and hole starting To save time and preserve accuracy when starting edges and holes, consider these pointers: Starting from an edge is easier on a submerged machine. For additional protection against wire breakage, use a thickness-adapting function for the edge start-up. Make the start hole as large as possible to minimise burn time in scrap. String punches together for longer, unattended burning. Cut parts off during the day while the operator is present. Minimise required operator intervention by using slugless (coreless) machining. Performing a slugless burn i s advantageous when the process will result in a slug that will move and pinch the wire, or when it is so small it could potentially get caught in the lower flush cup. Fur ther, some machines , when experiencing wire breakage due to a poor batch of material will, after a preset number of wire breaks, make stepped adjustments to complete the job in an unattended operation.
Preparing blanks Maximising conditions, such as flushing pressure when
Nike Air Max 90 Candy Drip