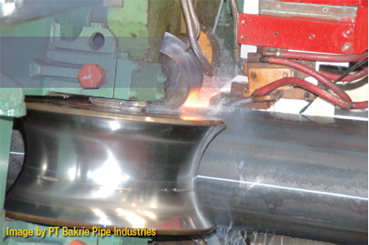
Fixing a coil shape problem begins with a close examination of the defect. While metal producers have greatly improved the quality of their flat-rolled products, customers these days have tightened their specifications. Quality is a moving target. What was good enough yesterday may not be good enough tomorrow. There are many types of metal grades available, and more equipment options. The coil world has become a much more complex industry. The assumption is that manufacturing and process managers must know what type of equipment they want or need. What processes they need to make sure their coil is flat? But what is flat enough? Much has been written about different types of coil shape control equipment and the theories behind them. You need to determine where you are at the start, where you want to end up, and how to get there. From a generic point of view, assuming that the equipment-builders' designs have enough horsepower, structure, and range of control, you can categorise the options. Shape defects There are two different classifications of shape defect, each requiring a different resolution. Both involve length differentials in one direction or the other. 1. A surface-to-surface length differential appears as longbow (coil set) or crossbow. The offset rolls of a straightener, flattener, and leveler can stretch the top and bottom surfaces to flatten the material. 2. An edge-to-edge length differential appears as buckles, waves, or camber. A leveler with adjustable roll bend can also differentially stretch the material in the rolling direction, from one edge to the other, to control waves and buckles. Adding tension to the process vastly improves the amount of elongation produced and, thus, the control of buckles, waves, and camber. None of these machines梥traightener, flattener, or leveler梚s effective for controlling crown. This is really not a shape issue; it is another problem. 3. A surface-to-surface thickness differential is called profile or crown. This may be either lengthwise or width wise. A rolling mill with opposed work rolls is required for crown control. The rolling mill can also do some flatness correction. The problem is that when the cold mill reduces thickness in one area, it also elongates that area in the rolling direction. Trying to control length differential (shape) and thickness differential (profile) at the same time is asking a lot. It is optimal to let the rolling mill do what it does best梒ontrol the profile. Once you have determined which shape problem you have, you can determine which type of equipment is effective in controlling it. How bad is the problem? In the past, stampers performed a visual inspection on sheets or plates to determine whether the coil is flat enough梟ot a very precise measurement method. Flatness tolerances are published for most products. They refer to a wave height of so many inches in 8 or 12 feet regardless of the distance between wave and valley. For close-tolerance manufacturing projects, they are not meaningful. It's best to apply some numbers to the shape problem. If you can describe these conditions in precise terms (in units) you can easily calculate the required reduction in strip length differential and compare it to the capabilities of equipment being considered. Increasingly, producers and consumers are using I-units to describe the flatness of their sheet, plate, and coil. An I-unit is a measure of unflatness based on wave height and wave length. It reflects both the wave height and length that must be overcome to level the material. The percent elongation (strain) required for levelling is directly proportional to the measured number of I-units. One percent length differential is equal to 1,000 I-units. Thus, one I-unit equals 0.01 percent length differential. The difference between the incoming shape and the desired outgoing shape can be shown as a perce
Adidas