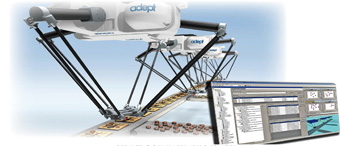
Improving product quality with flexible automation & software
Source: Release Date:2010-11-11 134
Precise and repeatable robots coupled with new powerful all-in-one automation software can deliver a complete system to help manufacturers produce high quality products, protect their image and increase levels of business
WITH recalls taking centre stage in today's media, manufacturers must closely evaluate the cost of poor quality (CoPQ) to their business. CoPQ is typically defined as the costs that would disappear if your manufacturing process were perfect. These costs include lost goodwill and expenses incurred from replacement, refund, rework, and scrapping. It has been estimated that CoPQ amounts to approximately 5 to 30 per cent of a manufacturer's gross sales. This means CoPQ is costing manufacturers millions per year and therefore every executive should recognise that quality must be addressed to remain competitive. In industries where the price of product is the most prevailing factor, quality can be a significant differentiator and can either help or hurt your reputation as a manufacturer. There is a common perception that improving the quality of products being produced can be a costly endeavour. And because of the pressure to shrink budgets and maximise the value of systems already in place, it is often an area overlooked in favour of getting product out the door. Flexible automation and intelligent automation systems are tools manufacturers consider adopting to increase production, streamline their processes and cut costs, but there remains the perception that implementing automation is cost prohibitive. However, when improved quality is included in the analysis, the return on investment associated with flexible automation frequently meets corporate hurdle rates. Expense of automating Probably the most stated reason given for a manufacturer's hesitation in investing in automation is cost. Many manufacturers claim robots are just too expensive. In the short run, it may seem too expensive to adopt new methods to increase the quality of the products you produce. But in order to remain competitive, you must look past the near-term expense and conceptualise ways to design a system that delivers products with quality assured. Although the cost of a robot isn't insignificant when factoring in the total cost of manual labour, you find that in actuality automation is generally more cost effective and efficient. Consider the cost of one employee. You have salary, benefits, training costs, worker's compensation, vacation, sick time and of course employees are limited to how long they can work during a shift. Coupled with the fact that automation can run 24/7, manufacturers find that their production increases and in most cases they see a return on investment in less than two years. "It is important to note too that the cost of automation over the last 10 years has dropped significantly," says Mark Beatty, automation project manager at Mecano Industrie Inc. of Quebec, Canada, a leading robotics integrator. "This coupled with the availability of new pre-engineered software, the ability to provide plug and play systems and pre-delivery testing of systems prior to installation at the customer's site all reduces the implementation cost of automation." "When considering the 憈otal cost of ownership' or the life of the product they're building and selling manufacturers should also consider that automating their systems domestically may be less expensive than incurring the high costs of poor quality and the rising costs of shipping products to and from off shore facilities," said Mike Koziel vice president of sales for Eagle Technologies a Michigan, USA-based automation systems provider. "We believe that in the long run automation, especially 慺lexible automation', will not only lower manufacturers' overall costs but building their products domestically will help restore the United States to the manufacturing power it once was. And that will be goNike Air Jordan 1 Retro
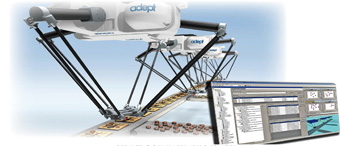
You May Like