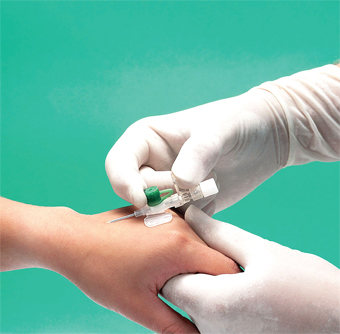
Injection mouldings are vital helpers in medical technology. There seems to be no limit to what injection moulding is capable of. Such specialised innovative methods as co-injection, in-mould decoration, insert moulding, foam injection moulding, gas-and water-assisted injection moulding, combined processes, thin-wall technology and, increasingly, micro- and nanotechnology help to satisfy the wide-ranging needs of the various user industries. It is in medical technology above all that injection moulding offers scope for endless possibilities. Along with ongoing progress in process engineering, the development of new types of materials is opening up additional fields of application. Sterilisability, biocompatibility, antimicrobial finishes, special barrier properties, nano- and microsystems technology, and biodegradable and absorbable materials are just some of the key areas in which materials developers are advancing progress in this vital field. However, anyone wanting to gain a foothold in medical technology has to be not only innovative and engage in high-quality and cost-effective production, but also master the guidelines that additionally apply in this sector. Safety and cleanliness across the board Compared to other branches of industry, the standard of quality and documentation here is outstanding with companies needing to adhere to Good Manufacturing Practice (GMP) guidelines. Continuous monitoring, compliance with the hygiene regulations and the full documentation of all process data over a period of years are integral to these guidelines. The production of medical and pharmaceutical injection mouldings is closely associated with cleanroom technology. For this, the manufacturers of injection moulding machines get together with cleanroom specialists to offer a variety of cleanroom solutions tailored to the article being produced and factory conditions. A simple and inexpensive approach is the mounting of a laminar-flow unit over the clamping plates for the injection mould. The most elaborate solution involves the operation of the injection moulding machine in the cleanroom itself. The all-electric injection moulding machines now rapidly gaining ground can fully exploit their advantages here. Compared to conventional hydraulic machines, they generate barely any waste heat and, as a result of their encapsulated drive units, are free of lubricants and other abraded particles that might contaminate the injection mouldings.
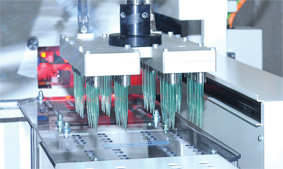
Within 0.25 seconds, this removal gripper enters the injection mould, removes the pipettes from a 32-cavity mould, checks and exits the mould Single-use medical articles are items that are usually mass-produced fully automatically and to an exceptionally high standard of quality under 100% quality control. For production to be cost-effective, every tenth of a second counts. The requisite speed is provided by ever lighter and slimmer removal systems with optimised drives. An extremely fast cleanroom-compatible removal gripper was launched by Hekuma GmbH, Eching (Germany), at the end of 2009. What the supplier claims to be the fastest removal system currently available for pipette tips achieves with its linear axis acceleration rates of up to 10 g and travel speeds of up to 1,200 mm/s. The injection moulds used for the mass production of medical technology items also of course have to be highly precise, cleanroom-compatible and at the same time economical. Along with the realisation of thin-walled products to save materials and cycle time, there is also a demand for multiple cavities and sophisticated cooling systems. However, it is not only single-use items that originate in the injection mould. For when it comes to replacement parts for the human body, injection moulding is a preferred process. Particularly spectacular are "components" for use in the inner organ
Encuentra zapatillas de la talla 36 a la 40 para Mujer