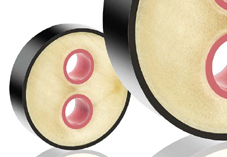
KraussMaffei Berstorff is now offering complete systems for continuous production of PU-insulated pipes. The extruded plastic pipe is given an insulating polyurethane layer, followed immediately by the addition of a protective polyethylene sheath. The pipe - made of PE-HD, PE-X, PE-RT or PB according to the application - is produced on a conventional pipe extrusion line. A barrier layer can be applied. The pipe coming off the line is wound onto large steel drums ready for transfer to the second production system unit for application of the insulation layer. Alternatively, the insulation layer can be added to bought-in pipe. In this second unit, the pipe is unwound from the steel drums, heated if necessary, and fed under tension into a shaping conveyor. A PU mixing head dispenses the polyurethane mix at the inlet throat. The aluminium shaping jaws define the outer diameter of the insulation layer by limiting the foam volume. A film prevents the polyurethane from adhering to the aluminium shaping jaws. Once the PU insulation layer has cured, the pipe leaves the shaping conveyor and a PE outer sheath is applied, using a single-screw extruder with a sheathing die. This outer sheath is cooled, the whole composite pipe is hauled off and wound on a drum. The system allows the integration of anti-diffusion barrier layers and/or wires to monitor leakage. www.kraussmaffei.com
Running Shoes, Trainers, Shorts, Spikes and Clothing