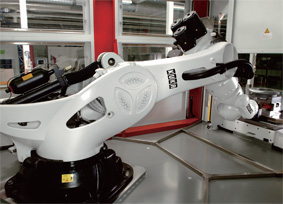
When it comes to automation of its machining centres, Maschinenfabrik Berthold Hermle AG relies on the competence of Augsburg-based KUKA Roboter GmbH. In the new RS 4 manufacturing system, the company has opted to exploit the strengths of the KR 1000 titan. The impressive 1000kg payload capacity of the titan is suitable for fully-automatic loading and unloading of Hermle machining centres with heavy workpieces, such as those found in tool and die-making or in mechanical engineering. "The components that are important for the precision and long service life of a machine tool are developed and manufactured entirely in-house," explained Rainer Kohler, managing director of Hermle-Leibinger Systemtechnik GmbH, a Hermle subsidiary that specialises in the automation of machine tools. The company places great emphasis on the designation "Made in Germany" and stands by Germany as a production location. Robotic app increases spindle service life All C series machine models from Hermle can be fully automated with KUKA robots. The RS 4 machining centre combines a KUKA KR 1000 titan robot, a pallet magazine and one or even two 5-axis C 50 U dynamic machining centres to form a high-performance production system. The robot system can transport loads weighing 1000kg and is used in production for the fully-automatic machining of heavy castings and aluminium workpieces. A sensor-monitored changeover station allows the manufacturing system to be loaded and unloaded without interrupting the machining process. The KR 1000 titan is responsible for loading and unloading the pallets with clamped workpieces. With its automatically exchangeable grippers, however, the KUKA robot can also directly handle the most varied workpieces with ease. Pallet handling and workpiece handling are thus possible in an "on-the-fly" changeover without the need for operator intervention. The titan is positioned in front of the machining centre and safeguarded by means of a sophisticated door safety system. Two operations can thus be executed in parallel, while one machine tool is machining a workpiece, another can be upgraded. Depending on customer requirements, the system can also be expanded to include a variety of heavy-duty racks for workpieces. Payback within a year "The KUKA robot is a highly flexible element in the machine tool," explained Kohler. The unlimited degrees of freedom of the titan make it possible to load and unload a vast range of pallets and workpieces of any size in a cell. The great flexibility allows the operator to convert the system quickly to meet new challenges. The robot ensures optimal utilisation of the Hermle machining cantre in three-shift operation - even at the weekend. Automation of the machine tool with the KR 1000 titan boosts the productivity of the system, reduces unit costs and shortens the payback period. Safe interaction Safety is of paramount importance in Hermle machining centres. Where operator and robot work together in close proximity, it must be ensured that the robot cannot move out of its defined workspace. The software transfers safety-relevant control tasks directly to the robot controller, thereby eliminating the need for an external safety PLC. "The key factor in the face of global competition is to increase the service life of the machine! A robot system will always be costeffective," said Kohler.(the end)
Air Max Mercurial R9