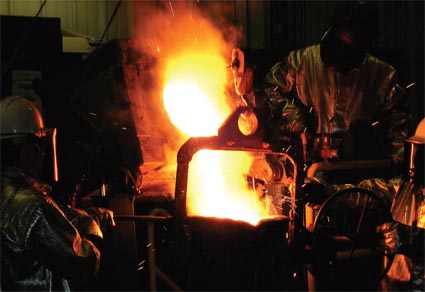
Metal casting is an ancient technique that has a variety of applications and purposes. Reports showed that metal casting technology using moulds originated in the Middle East, since the oldest preserved cast parts, such as weapons and cult objects, made of copper originated from the region. The process of metal casting involves melting metals at high temperatures and using moulds to then shape the metal into new items. The furnaces used in metal casting helped pave the way for the industrial revolution, without which the course of history would be dramatically different. Metal casting is just one form of metalworking that has seen a recent surge in popularity as resources are becoming more affordable and communities are springing up to share information, ideas, and projects. Cast metal products are found in 90 percent of manufactured goods and equipment. From critical components for aircraft and automobiles to home appliances and surgical equipment, cast metal products are integral to the global economy and our way of life. High-pressure die casting High-pressure die casting is a versatile manufacturing process in which molten metal is injected with a die casting machine using considerable pressure into a steel mould or die to form products. These moulds, or dies, can be used to produce complex shapes with a high level of accuracy and repeatability. Die castings are among the highest volume, mass-produced items manufactured by the metalworking industry. They are used in numerous applications for industries, such as automotive, locomotive, agricultural, marine, plumbing and lighting. There are several alloys that can be used: zinc, aluminium, magnesium, brass, and copper. Every alloy offers a unique advantage. Aluminium is one of the commonly used alloys because it is light-weight, very strong, corrosion-resistant, and is easily polished or painted for an appealing finish. Zinc offers high-impact strength and is the easiest to cast. Brass is heat-resistant, highly corrosion-resistant and provides excellent electrical conductivity. High-pressure die casting is an efficient, economical process that offers a broader range of shapes within closer tolerances than many other metal manufacturing techniques. They can be produced with smooth or textured surfaces, and they're easily plated or finished with a minimum of surface preparation. They can even be designed to complement the look of a surrounding part. There are several more benefits to choosing die casting over other manufacturing processes. High pressure die castings are heat resistant, highly durable, and provide close tolerances. They reduce or eliminate secondary machining operations making them cost efficient. High pressure die casting is ideal for anyone who needs a large quantity of intricate metal shapes that are highly durable.
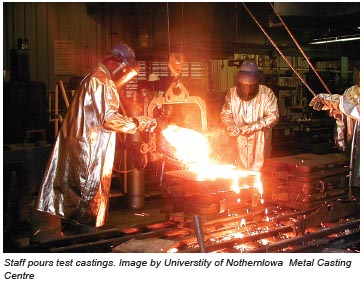
Usually, bigger casting parts are made through sand casting as metal moulds normally weigh from 10 to 100 times as much as the components they manufacture. Where as, small casting parts are fabricated using metal moulds that assure dimensional accuracy of the casting they produce. In die casting process, large and high cooling rates results in air to be trapped in the casting. This procedure produces high amount of porosity at centre of casted products. Though, R&D has been done to find a way for lowering the porosity but this is also the true fact that it is impossible to eradicate entire porosity. Thus, die casting products are lower in strength as compared to low-pressure or gravity-fed permanent mould castings that have slower cooling rates, but produce strong components. Coating aluminium The life of aluminium and magnesium die castings dies can be extended considerably with the process. This already has been proven using the coating on dies, especially those affected by heat checking. When the treat
Air Jordan